Single-Minute Exchange of Dies (SMED)
In today’s manufacturing world, downtime is the enemy of productivity and competitiveness. One of the best ways to beat downtime is Single-Minute Exchange of Dies (SMED), also known as the ‘minute exchange of die’, a core concept from the Toyota Production System.
SMED is a lean manufacturing technique that reduces setup and changeover times to optimize the changeover process, with the goal of achieving quick changeover and minimizing downtime. This guide will cover the concept, benefits and implementation of SMED so you can get your processes streamlined and efficient.
What is Single-Minute Exchange of Dies (SMED)?
The SMED acronym stands for Single-Minute Exchange of Dies (also referred to as SMED Single Minute Exchange), a term coined by Japanese industrial engineer Shigeo Shingo, one of the pioneers of lean manufacturing. The meaning of SMED lies in minimizing the time required to switch die or tooling on production equipment using the SMED technique. Originally developed for die changes in manufacturing presses, SMED today applies broadly across various manufacturing sectors such as automotive, electronics, and food production, and can be used to optimize the entire production process in these industries.
SMED as a Lean Manufacturing Methodology
SMED is fundamentally a lean manufacturing technique aimed at optimizing setup and changeover processes. As a methodology, it follows a structured approach to reduce downtime and improve operational efficiency by separating activities into internal and external categories and streamlining each. The SMED process is a systematic approach that plays a crucial role in process improvement by reducing equipment changeover times and enhancing overall productivity.
The core changeover steps of the SMED process are:
- Observation and Documentation: Analyze the current changeover process in detail.
- Separation of Internal and External Activities: Identify tasks that can only be done when the machine is stopped (internal) versus those possible during operation (external).
- Simplification of Internal Tasks: Use quick-change tools, reduce fasteners, and design easy-to-handle fixtures.
- Standardization and Training: Document the optimized process and train employees accordingly, which helps to streamline processes and drive continuous process improvement.
SMED Analysis: How to Analyze Changeover Processes
Conducting a thorough SMED analysis is critical to identify inefficiencies and prioritize improvements. This involves:
- Data Collection: Measure changeover times, record every activity via video or direct observation, and maintain checklists. Track the time spent on each activity, especially during the actual changeover, to identify where delays occur.
- Metrics Evaluation: Compare times before and after SMED implementation, assess cost reductions, and monitor improvements in Overall Equipment Effectiveness (OEE). Measure the duration of the actual changeover and analyze where time is lost to target specific improvements.
- Task Categorization: Break down each changeover step as either internal steps or external steps. Identify internal steps and explore strategies to convert internal steps or convert internal elements to external ones, reducing downtime and improving efficiency.
Example Table of Internal and External Activities
This table distinguishes between the internal and external elements of the changeover process, helping to identify which activities can be performed as part of external setup to reduce downtime.
Benefits of SMED in Manufacturing
SMED in manufacturing delivers:
- Less Downtime: Faster changeovers means less idle equipment, more OEE, less waste and less downtime.
- More Flexibility: Smaller batch sizes and quicker response to customer demand.
- Higher Productivity: Operators spend less time on setup, less production time and more time on production.
- Cost Efficiency: SMED reduces costs by lower manufacturing costs and overall manufacturing costs through less labor and material waste from longer changeovers.
- Quality: Standardized setups reduce errors and defects.
- Operational Excellence: SMED drives continuous improvement and efficiency.
How to Implement SMED
SMED is a 4 step process:
- Observe the Current Process: Start by documenting the current changeover process. Get all employees involved to ensure every step is captured. Record all activities, timing and challenges. This is the baseline for waste.
- Split Internal and External Activities: Categorize each activity as internal or external. Focus on internal tasks and identify which can be done externally to reduce downtime. The goal is to minimize internal elements through optimization.
- Simplify Internal Activities: Simplify and optimize internal tasks. Use quick change tools, reduce fasteners and design fixtures for easy setup.
- Standardize and Train: Write down the new process and train staff. Review and refine the remaining elements of the process regularly.
SMED can optimize business processes beyond the shop floor, across the entire organization.
SMED in Action
Automotive
Car manufacturers use SMED to reduce changeover time between models on a production line. Standardized tools and modular components means what used to take hours can now take minutes. By using multiple operators to perform simultaneous tasks — like a NASCAR pit crew or NASCAR pit crews — teams can coordinate tasks efficiently and minimize downtime during changeovers.
Food Manufacturing
In food manufacturing SMED enables quick change from one product line to another by pre-organising internal and external components, for example from one snack flavour to another. Preparing internal components in advance simplifies the whole process, minimises waste and downtime and meets consumer demand for variety.
Electronics
Electronics manufacturers use SMED to change between different circuit board designs. By pre-organising tools and materials and identifying internal and external components that can be prepared while the machine is running they can adapt to changes in production schedules more quickly. Functional clamps allow for faster tool changes and less setup time, more efficiency.
SMED in the Context of Industrial Standards and Industry 4.0
SMED integrates well with modern industrial practices such as Lean Manufacturing, TPM (Total Productive Maintenance), Six Sigma, and ISO standards. The SMED system’s methodology complements continuous improvement frameworks and quality management systems.
Challenges
While SMED offers many benefits, implementing it can be tough. Common hurdles:
- Resistance to Change: Employees don’t want to change how they do changeovers. Communication and training is key to get them on board.
- Initial Outlay: The cost of new tools, fixtures or equipment modifications can seem high. But the payback is usually worth it.
- Complex Processes: Highly complex setups require more analysis and creative thinking to get each internal element right.
Advanced SMED Strategies
Once you have the basic SMED principles in place, advanced strategies can take it to the next level. Advanced SMED strategies are specifically designed to optimize equipment changeovers and focus on reducing equipment changeover times even further. Smed implementation is a strategic approach within Lean manufacturing aimed at minimizing changeover times to improve operational efficiency. These include:
- Technology: Automation and digital tools like sensors and software can monitor setup times and identify internal and external weaknesses. Predictive analytics can help predict delays and schedule accordingly.
- Modular Design: Design equipment and components to be modular so that replacements and setups are faster and external components are always ready. This is especially useful in industries with many product variations.
- Kaizen Events: Run focused improvement workshops or Kaizen events to help teams identify and implement SMED improvements especially in internal setup. Collaboration during these events gets employees on board.
- Cross-Trained Employees: Train employees across multiple roles so that setups can be done efficiently even in case of absenteeism or high demand.
Future of SMED
As industries change the principles of SMED still apply to optimise the manufacturing process. With Industry 4.0 SMED can be integrated with smart manufacturing technologies to make it even more efficient. For example IoT devices can provide real time data on machine performance so you can make quicker and more informed decisions during changeovers.
And with the focus on sustainability SMED plays a part in reducing waste. By allowing smaller batch sizes and minimising equipment changeover downtime SMED is leaner and more green manufacturing.
Summary
SMED is a lean manufacturing methodology that stands for Single-Minute Exchange of Dies. Its meaning is to minimize equipment downtime by optimizing changeover times through analysis, separation of tasks, simplification, and standardization. By applying SMED principles and methodology, manufacturing operations can achieve changeovers in single-digit minutes, supporting greater efficiency and competitiveness by reducing equipment changeover times. Integration with modern industrial standards and Industry 4.0 technologies ensures SMED remains relevant and effective in today’s dynamic manufacturing landscape.
Simplify the way people work and learn at the frontline
See the industry-leading how-to platform in a 30-minute live demo.
Learn more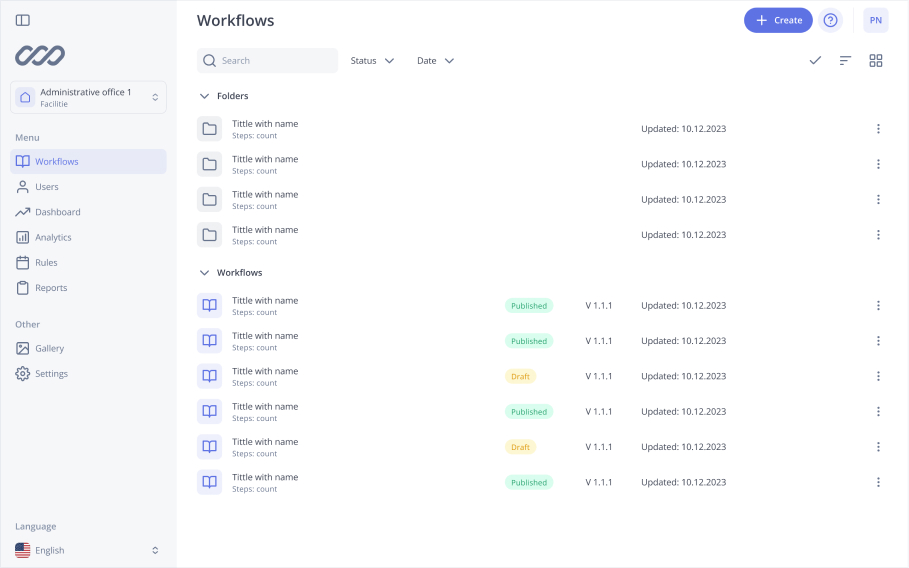
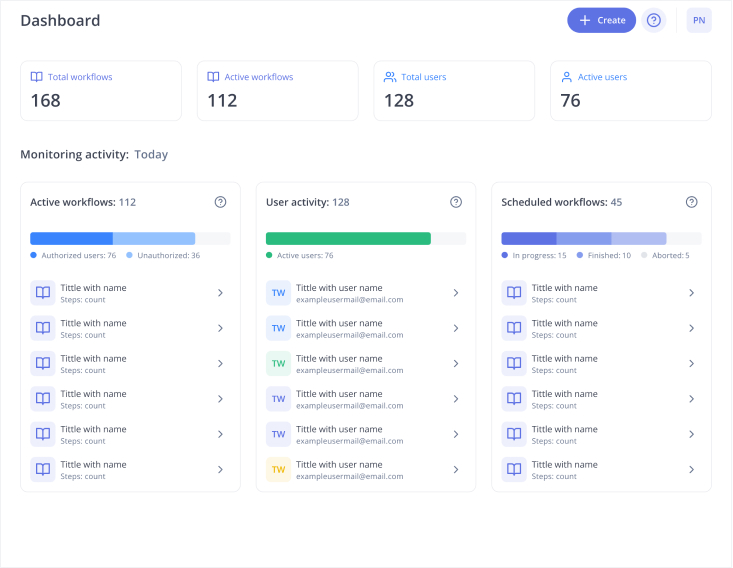