Safety Walk
Safety walks are a key part of workplace safety and hazard control. They involve management, safety officers or designated employees carrying out regular checks to identify hazards, ensure compliance with regulations and promote a safety culture. Companies that do safety walks consistently have fewer workplace incidents, better employee morale and better operational efficiency.
Being a safe workplace is a legal and moral obligation. A well run safety walk programme helps with OSHA compliance and avoids costly fines and legal issues. Employees working in a safe environment are more productive and engaged which benefits the business overall.
What is a Safety Walk?
A safety walk or safety inspection is a proactive way to check the condition of your workplace. It’s where you methodically go around the workplace to spot safety hazards, check safety procedures and ensure employees are following the rules. Risk assessment during a safety walk allows you to determine the level of risk associated with the hazards you’ve found, prioritise actions and allocate resources to improve safety. Unlike formal audits, safety walks are more frequent and focus on immediate issues before they become big problems.
Safety walks aren’t just about finding faults – they’re also an opportunity to engage employees in safety conversations, reinforce good behaviour and build a safety mindset. By including safety walks in your daily operations, you can build a culture of continuous improvement and shared responsibility.
The Benefits of Conducting Safety Walks
- Hazard Identification: Safety walks help find hidden dangers, like exposed wires, slippery floors or blocked fire exits, before they cause accidents. Health and safety’s role in proactive measures like inspections and checklists to mitigate risks and keep employees safe.
- Regulatory Compliance: Regular safety walks keep you compliant with industry standards and regulations.
- Employee Engagement: Employees feel looked after when management cares about their well-being, so a positive work environment.
- Incident Prevention: By identifying and fixing risks early safety walks reduce workplace injuries and downtime.
- Continuous Improvement: They give you opportunity to refine your safety practices and implement new safety measures based on what you see.
- Emergency Preparedness: Identifying weaknesses in emergency procedures means employees are prepared for potential hazards and less risk in critical situations.
- Reduction in Insurance Costs: Fewer workplace accidents means lower insurance premiums and workers’ compensation claims and cost savings for the business.
Key Elements of an Effective Safety Walk
To make a safety walk effective it needs to be structured and systematic. A safety walk checklist is vital in observing work processes, documenting findings and making sure all safety aspects are covered. Here are the essentials:
1. Planning the Walk
- Define the purpose of the safety walk (e.g. checking emergency exits, PPE usage etc). Safety walks can identify hazards, improve compliance to regulations and promote a safety culture.
- Create a checklist to make sure all critical areas are covered.
- Schedule safety walks at regular intervals to be consistent.
- Assign personnel to lead and document safety walks.
2. Conducting the Walk
- Observe workplace conditions and employee behavior. Label, store and train employees on handling and disposing hazardous materials during safety walks.
- Engage employees by asking them about their safety concerns.
- Take notes and document any hazards found with photos or written descriptions.
- Communicate findings immediately when critical issues are found.
- Observe workflows to make sure safety protocols are being followed without compromising productivity.
- Evaluate the use and condition of personal protective equipment (PPE).
3. Post-Walk Actions
- Compile a report of observations, hazards and recommended actions.
- Assign responsibilities to each hazard.
- Follow up on previous safety walk reports to continue improvement.
- Recognize employees who show commitment to safety to reinforce good behavior.
- Set deadlines for corrective actions and ensure proper follow-through.
Common Hazards During Safety Walks
Some common workplace hazards that safety walks help identify include:
- Slip, Trip, and Fall Hazards: Wet floors, loose cables, uneven surfaces. It is essential for floors to be clean and surfaces free from trip hazards to maintain safety in designated aisles and walkways during safety inspections.
- Fire Hazards: Blocked exits, improper storage of flammable materials, malfunctioning fire extinguishers.
- Electrical Hazards: Frayed cords, exposed wiring, overloaded circuits.
- Machine Safety: Missing guards, improper lockout/tagout procedures.
- Ergonomic Issues: Poor workstation setups leading to musculoskeletal disorders.
- Chemical Safety: Improperly labeled or stored chemicals.
- Environmental Hazards: Poor air quality, inadequate lighting, extreme temperatures.
- Psychosocial Risks: Workplace stress, bullying, and fatigue-related hazards.
Gemba Walk vs. Safety Walk
Gemba Walk and Safety Walk are both important in continuous improvement but serve different purposes and look at different parts of the work environment. Here’s the breakdown:
1. Purpose:
- Gemba Walk: To observe and understand the actual work processes (where the “real work” happens) to find areas for improvement, solve problems and make sure the processes are running well. “Gemba” is Japanese for “the real place” and the Gemba Walk is all about observing the work at the location where value is being created.
- Safety Walk: To ensure workplace safety by finding hazards, risks and unsafe conditions that can harm workers. Safety Walks are about compliance with safety regulations, finding potential dangers and making sure safety protocols are being followed.
2. Focus:
- Gemba Walk: Focuses on operational processes, efficiency, waste reduction and quality. Leaders observe how employees do their jobs, gather feedback and look for opportunities to improve processes.
- Safety Walk: Focuses on worker health and safety. It’s about checking for faulty equipment, unsafe practices, ergonomics issues, fire safety, personal protective equipment (PPE) and environmental conditions like ventilation.
3. People Involved:
- Gemba Walk: Leaders (managers, supervisors etc.) engage with workers on the floor to understand challenges, ask questions and learn from employees. It’s about observing and collaborating to find solutions.
- Safety Walk: Safety officers, supervisors or managers observe workplace safety from a compliance perspective, often with safety experts. It’s about finding hazards and making sure safety protocols are being followed, with less direct involvement in process improvement.
4. Frequency:
- Gemba Walk: Regularly scheduled and more frequent, usually done daily or weekly to monitor performance and improve processes.
- Safety Walk: May be scheduled periodically (e.g. weekly or monthly) but can also be done randomly especially if there’s an ongoing concern or after an incident.
5. Action:
- Gemba Walk: After the walk, the focus is on continuous improvement actions—this could be implementing process changes, employee training or workflow optimization.
- Safety Walk: After the walk, corrective actions are about reducing risks, fixing safety hazards and compliance with safety regulations. These actions aim to remove or control the danger.
6. Outcomes:
- Gemba Walk: Outcomes from a Gemba Walk are about operational improvement, better productivity, quality and waste reduction.
- Safety Walk: Outcomes from a Safety Walk are about a safer work environment, fewer accidents and health and safety practices.
Best Practices for Safety Walks
- Be Consistent: Conduct safety walks regularly and at different times to get a comprehensive view of workplace conditions.
- Encourage Open Communication: Employees should feel comfortable reporting hazards and making suggestions.
- Use Technology: Digital checklists and mobile apps streamline the process and improve reporting efficiency.
- Provide Training: Educate employees and managers on what to look for during a safety walk.
- Act on Findings: Ensure that identified hazards are addressed promptly to demonstrate the organization’s commitment to safety.
- Integrate with Safety Culture: Incorporate safety walks into broader safety initiatives to align with company-wide safety goals.
- Engage Leadership: Senior management should actively participate in safety walks to emphasize their importance.
- Analyze Data: Track trends from safety walk reports to identify recurring issues and implement targeted improvements.
The Role of Leadership in Safety Culture
Management has to play a big role in making safety walks effective. Leaders should participate in walks, support safety initiatives and allocate resources to address safety concerns. A safety culture starts at the top and when employees see that leadership is serious about safety they will follow suit.
Moreover management should create a non punitive environment where employees feel safe to report hazards. Encouraging open dialogue and taking proactive action on feedback will get you a safer and more engaged workforce.
Conclusion
Safety walks are a simple yet powerful tool for workplace safety. By systematically identifying and addressing hazards you can create a safer workplace, reduce accident rates and improve employee well being. Implementing a structured safety walk program requires commitment but the benefits far outweigh the effort. Focusing on safety through regular inspections will give you a proactive approach to workplace risk management and a culture where everyone takes responsibility for a safe working environment.
Organizations that include safety walks as part of their safety strategy will not only see a reduction in workplace accidents but also get increased productivity, improved employee satisfaction and a stronger reputation as a good employer. Investing in safety now will mean a more sustainable future for any organization.
Simplify the way people work and learn at the frontline
See the industry-leading how-to platform in a 30-minute live demo.
Learn more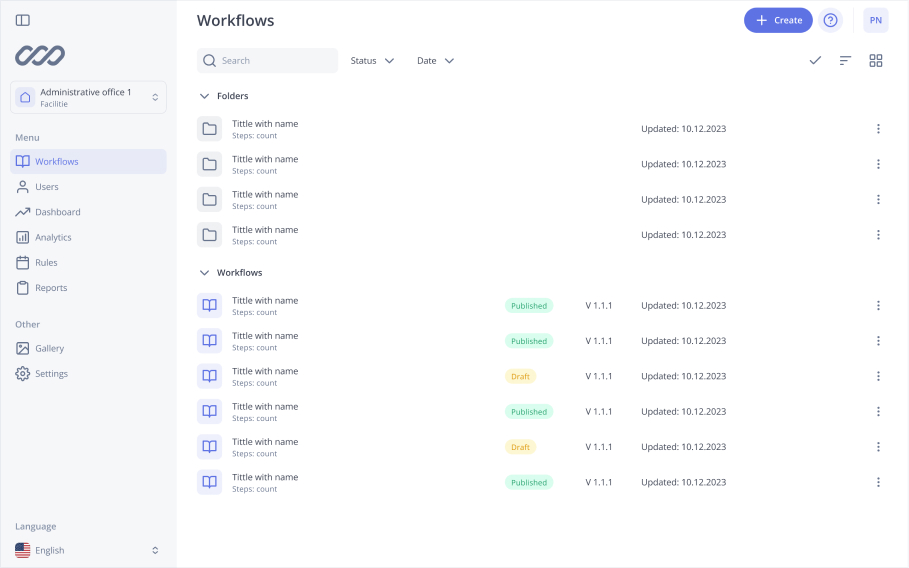
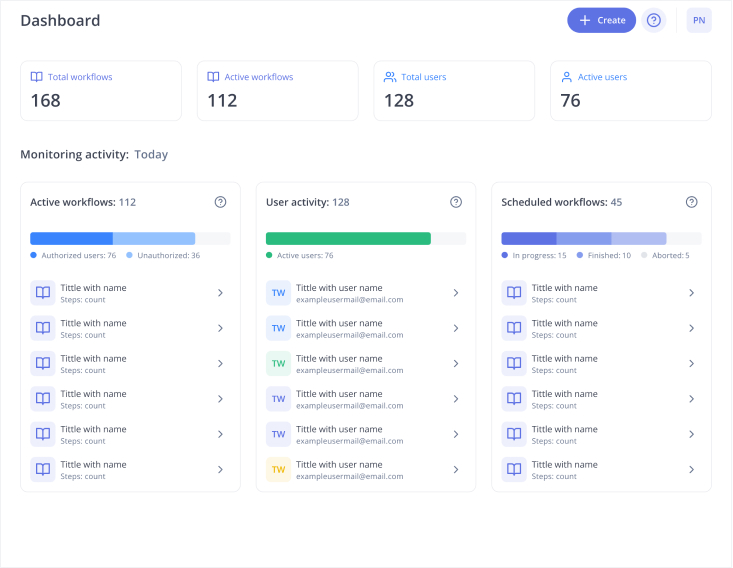