Right First Time
Right First Time or First Time Right (FTR) is Total Quality Management (TQM) concept according to which defect prevention is more beneficial and cost-effective than finding them and implementing appropriate fixes. Right First Time implies that the work is performed correctly the first time, starting from the production line, because mistakes imply the cost of time and money to fix them. FTR is used in the manufacturing process, affecting the reduction of human error, allowing reduced operational costs, and optimizing production processes for better efficiency and quality control.
First Time Right Key Performance Indicator
FTR is one of the main indicators of the effectiveness of quality management (KPI). Activities on the shop floor play a crucial role in determining the FTR metric, as they directly influence productivity and quality control. According to the American Society for Quality (ASQ), FPY is calculated by dividing the units entering the process minus the defective units by the total number of units entering the process. The higher the percentage obtained, the more efficient the production processes can be called.
Why Should Your Organization Rate the First Time Right Score for Customer Satisfaction?
The main advantage of increasing the percentage of FTR is the gradual disposal of 8 types of waste from Lean manufacturing. By reducing unnecessary time, money and tool costs, the organization complies with the principle of continuous improvement (Kaizen). One of the most important consequences of the introduction of Kaizen is to increase customer satisfaction.
Example: Right First Time in a Manufacturing Process
Imagine a company that manufactures electronics, such as circuit boards. Each circuit board must pass a series of quality inspections and tests before it’s approved. For each batch, the company wants to know the RFT percentage, meaning the proportion of boards that passed all quality checks on the first attempt, without any rework.
RFT Formula:
Calculation Example:
- Total units produced: 100.
- Units with no defects or rework on the first attempt: 95.
Using the RFT formula:
Interpreting RFT KPI
- High RFT % (e.g., 95-100%): Indicates a highly efficient process with minimal defects and high-quality standards.
- Low RFT % (e.g., below 90%): Suggests frequent errors, rework, or quality issues, which may signal a need for process improvements, more training, or better quality control measures.
So, the RFT KPI for this batch is 95% (High RFT %), meaning 95% of the units were completed correctly on the first attempt, with no need for rework.
How to Implement Right First Time with Visual Work Instructions?
The main steps are:
- Identification of Common Sources of Defects.
- Creation and Implementation of SOP Documents.
- Quality Control and Process Improvement.
- Data collection and analysis.
By embedding these principles into the organization’s everyday practices, First Time Right concept can improve quality of production, reduce waste, increase efficiency and customer satisfaction. This concept requires both a strong commitment to quality, accountability across the organization, implementation of technical tools and additional applications.
ProcessNavigation can be an excellent example of an application that will allow you to conveniently and instantly document product defects, find solutions and share them with others.
Use ProcessNavigation to successfully implement the First Time Right concept in your production process
Contact us
Simplify the way people work and learn at the frontline
See the industry-leading how-to platform in a 30-minute live demo.
Learn more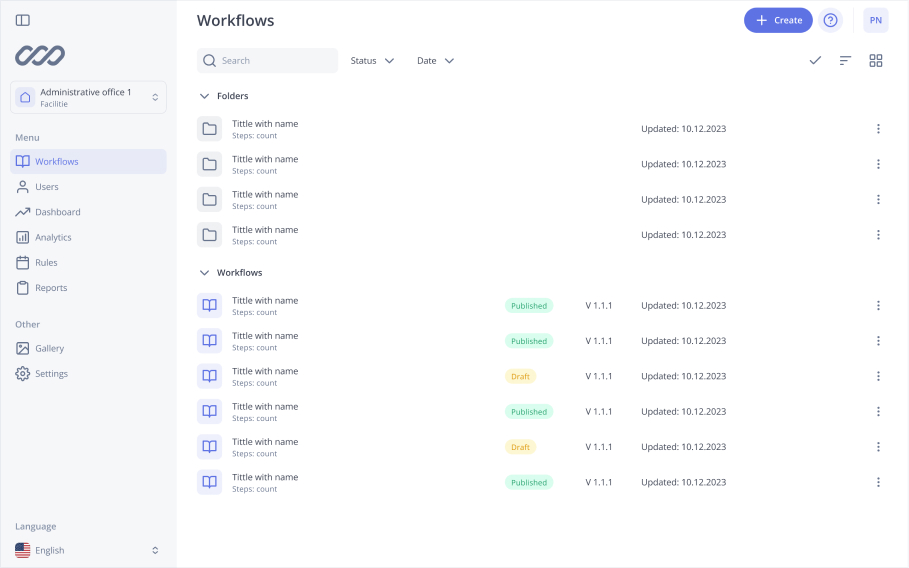
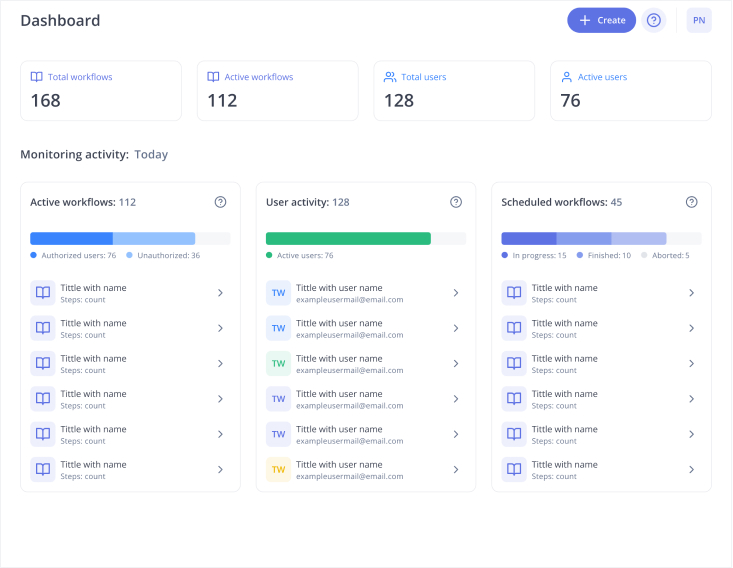