Remote Expert
The manufacturing industry has changed a lot over the last few decades. From CNC machines to additive manufacturing and Industry 4.0, new technologies have completely transformed factory operations. One of the biggest trends in recent years is the rise of remote experts in manufacturing engineering. This not only boosts efficiency but also innovation and reduces operational costs. Remote expert solutions are now part of modern manufacturing, making the industry more agile and resilient.
What is Remote Expertise in Manufacturing?
Remote expertise in manufacturing means providing professional support and problem solving without being physically present at the factory. Thanks to video conferencing, augmented reality (AR), real-time data sharing and other advanced communication tools, engineers and specialists can connect with on-site teams from anywhere in the world. They can help troubleshoot issues, optimise workflows and even provide remote training.
Remote support goes beyond just advice – it includes machine diagnostics, process improvements and real-time collaboration on design or production challenges. With cloud platforms, IoT (Internet of Things) and virtual tools, manufacturers can minimize downtime, enhance teamwork and improve productivity. In critical situations remote assistance can solve problems fast.
How Remote Expertise helps Manufacturing
Cost Efficiency and Smarter Use of Resources
In the past solving complex engineering problems meant flying in experts from other cities or even countries which resulted in high travel costs, delays and extended downtime. Remote expertise has changed this. By shifting to a remote support model manufacturers can reduce travel costs, eliminate the need for on-site visits and get help much faster.
With tools like cloud platforms, live video support and real-time data sharing engineers can troubleshoot issues and provide guidance without setting foot on the factory floor. For example if a machine breaks down or there’s a production delay a remote expert can jump in immediately, analyse the problem, suggest a solution and walk the on-site team through the repair.
This not only gets operations back on track faster but also improves collaboration between teams in different locations, making the manufacturing process more flexible, responsive and cost effective.
Global Talent Access
One of the biggest challenges manufacturers face today is finding the right talent — especially for specialist roles in engineering. In many regions skilled professionals are in short supply which can slow down production and limit innovation. Fortunately remote expert solutions break down geographical barriers and open up a global talent pool.
The ability to virtually connect with subject matter experts from various industries allows manufacturers to find the right professionals for specific tasks — whether it’s maintenance, troubleshooting or project management. This kind of access is especially valuable for complex high precision work or when adopting new technologies.
With software tools designed for real-time collaboration, file sharing and secure communication remote experts can work closely with on-site teams — no matter where they are in the world. It’s a flexible and efficient way to scale expertise and stay competitive.
Faster Problem Resolution and Minimize Downtime
Downtime in manufacturing isn’t just inconvenient — it’s costly. Even a short pause in production can result in significant financial losses. That’s why quick access to expert support is key. With remote assistance manufacturers don’t have to wait for someone to travel to the site. Help is available immediately.
When a machine breaks down a remote expert can log into the system, assess the situation and quickly identify the issue. Using tools like augmented reality they can guide on-site staff through the repair process in real-time, pointing out the necessary steps and ensuring everything is done correctly. This fast response minimizes downtime and the added layer of quality assurance ensures repairs are done right first time, reducing the chance of future problems.
By maintaining constant communication via live video and on-screen annotations remote experts can guide the team just as effectively as if they were on-site which maintains high safety and quality standards.
Improved Collaboration and Knowledge Sharing
Integrating remote expertise does more than just solve problems — it fosters a culture of collaboration and knowledge sharing. When engineers from different disciplines work together they share ideas that can lead to innovation. Remote expert services enable seamless communication between departments and teams, allowing engineers, operators and managers to collaborate in real-time, no matter where they are.
These tools bridge knowledge gaps whether teams are working in the same facility or scattered across the globe. Remote platforms also make it easier to capture and share best practices, troubleshooting tips and insights, so valuable information is available to everyone. This knowledge sharing approach allows employees, no matter where they are, to learn from each other’s experiences which makes the entire organisation more agile and efficient.Also experts can virtually connect with frontline workers to address issues, improve safety and ensure smooth operations on the shop floor. This is about building connections and continuous improvement through shared knowledge.
Training and Skill Development
One of the biggest benefits of remote expertise is its role in training and skill development. Manufacturing is a technical industry and new employees or less experienced workers need guidance when it comes to operating complex machinery and systems. Remote expert technology allows for customised training for each worker, valuable guidance without the need for physical travel.
Remote training can include live video demonstrations, augmented reality simulations and real-time virtual instruction — making the learning process more interactive and hands-on. Experts can guide workers through troubleshooting and maintenance tasks, help them develop the skills they need to do their daily tasks. This not only improves worker competence but also supports continuous improvement initiatives, so employees are equipped to meet the evolving demands of production.
Technologies Enabling Remote Expertise
Several technologies have made remote expertise possible in today’s manufacturing world. These tools don’t just enable remote collaboration — they also improve the quality, speed and effectiveness of the support provided.
Augmented Reality (AR) and Virtual Reality (VR)
AR and VR have taken remote support to a whole new level. With AR glasses or even just a smartphone workers on the shop floor can receive real-time, step-by-step visual guidance from remote experts. This can be a total game-changer when dealing with complex repairs or process adjustments. It’s like having an expert standing right next to you — except they could be halfway across the world.
In more advanced setups virtual reality is used for immersive training. Workers can practice operating machinery in a fully simulated environment before ever touching the real equipment. This is not only safer but also helps build confidence and skills in a more effective way.
Internet of Things (IoT) and Smart Sensors
IoT is one of the key enablers of remote expertise. By using smart sensors embedded in machinery manufacturers can track important performance indicators in real-time — temperature, pressure or vibration. This data is sent directly to remote experts, so they can monitor the health of the equipment and step in before small issues become big problems.
This proactive approach reduces unplanned downtime and keeps operations running smoother. Instead of just reacting to breakdowns remote experts can intervene early to prevent them altogether.
Cloud-Based Platforms
Cloud platforms make it easy to store and access everything from design files to live production data in one place. For remote experts this means they can see what’s happening on the shop floor without being there in person. They can jump into a project, review metrics and collaborate with on-site teams in real time.
Sharing files, live data and even making annotations helps everyone stay aligned. It’s not just about fixing problems – it’s about how teams work together from anywhere.
Video Conferencing and Communication Tools
Sometimes nothing beats a face-to-face conversation – even if it’s over a screen. Video conferencing tools like Zoom, Microsoft Teams and other industry specific platforms allow on-site workers and remote experts to connect instantly. They can talk through issues, share live video, send pictures and exchange documents in real time.
Plus chat and file-sharing features keep the conversation flowing, so important details aren’t lost. These tools ensure communication remains fast and fluid so problems get solved quicker.
Challenges and Considerations
While integrating remote expert services has many benefits, there are also challenges manufacturers need to address to make it work.
- Cybersecurity: As manufacturing becomes more connected the risk of cyber attacks increases. Remote expert solutions require access to production data, control systems and intellectual property. Manufacturers need to have strong cybersecurity protocols in place. Investing in secure communication tools, encrypted data channels and robust authentication mechanisms is critical to protect operations from cyber threats. Conducting risk assessments is also key to ensuring the data being shared between remote experts and on-site teams is safe.
- Reliable Internet Connectivity: Remote expert solutions rely on stable internet connections. In areas with poor internet infrastructure or factories with a lot of interference (like those with heavy machinery) remote collaboration may be a challenge. Manufacturers need to ensure they have reliable internet access to maintain communication with remote experts.
- Integration with Existing Systems: Integrating remote assistance into an existing manufacturing setup may require some changes. Manufacturers need to make sure their machinery, software and infrastructure is compatible with the new remote collaboration tools. This may involve upgrading machines with IoT sensors, installing new communication platforms or training employees on how to use the new technologies.
Remote expert solutions are changing how manufacturers solve engineering problems. They reduce costs, access global talent, downtime and improve collaboration – all of which keeps companies competitive in a fast changing industry. There are some challenges to overcome but the benefits are clear – remote expertise is a must have for modern manufacturing.
As technology advances it’s clear remote expert solutions will play an even bigger part in manufacturing engineering. From operational efficiency to continuous learning the possibilities are endless. Manufacturers who adopt this approach will be better prepared for what’s to come and stay ahead of the curve of innovation and productivity in a digital world.
Conclusion
Remote expert solutions are changing how manufacturers approach engineering problems. They reduce costs, access global talent, downtime and improve collaboration which keeps companies competitive in a fast changing industry. There are some challenges to overcome but the benefits are clear so remote expertise is a must have for modern manufacturing.
As technology advances it’s clear remote expert solutions will play an even bigger part in manufacturing engineering. From improving operational efficiency to continuous learning the possibilities are endless. Manufacturers who adopt this approach will be better equipped to navigate the future and stay at the forefront of innovation and productivity in a digital world.
Simplify the way people work and learn at the frontline
See the industry-leading how-to platform in a 30-minute live demo.
Learn more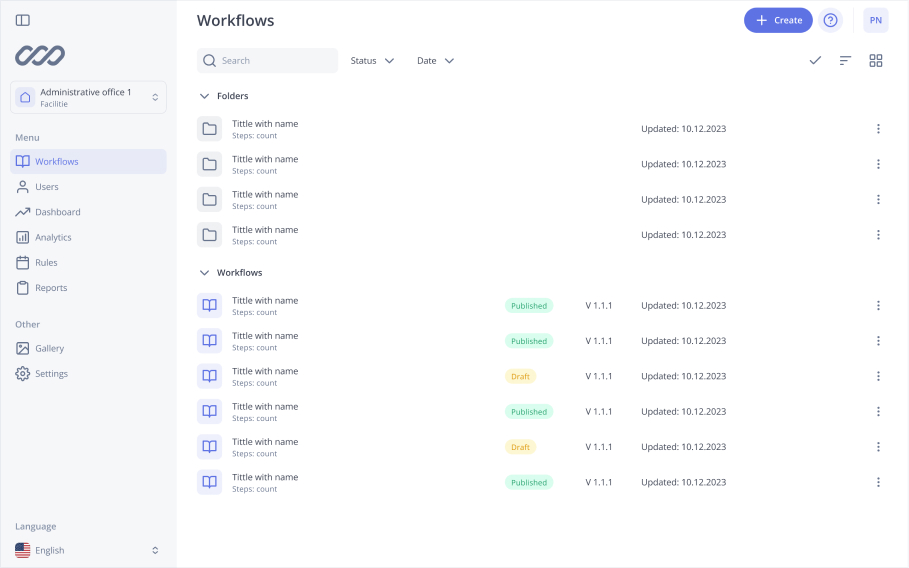
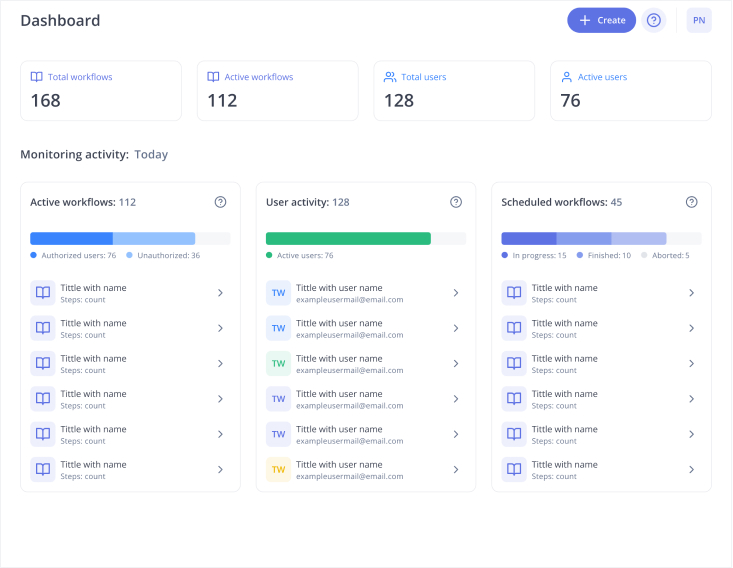