Poka-Yoke (Error Proofing)
What is Poka-Yoke
In any manufacturing environment, humans make mistakes. Small defects can lead to scrap, product recalls or even safety hazards. The Japanese concept of Poka-Yoke, or error protection, has changed the way we approach human error in industry. Poka-Yoke allows humans to prevent or correct errors so they don’t get into the process.
The concept of Poka-Yoke was first proposed in the 1960s by Shigeo Shingo, a manufacturing engineer at Toyota. His idea was simple: make mistakes impossible, or at least detect and correct them before they become big problems.
This isn’t limited to manufacturing; the principles apply to all industries, increase efficiency, reduce waste and create a culture of continuous improvement.
Why Poka-Yoke Matters
Defects don’t just cost money—they damage reputation, disrupt production and in safety-critical industries like automotive or aerospace, they can be life threatening. Poka-Yoke is about prevention, higher quality, smoother operations and stronger customer trust.
This fits perfectly with lean manufacturing principles which eliminate waste and continuous improvement. By catching mistakes early Poka-Yoke prevents small issues from snowballing into big, time consuming problems.
Poka-Yoke Principles
Error defense systems are based on six principles:
- Elimination: Redesign products or processes to make mistakes impossible.
- Prevention: Block errors before they happen.
- Replacement: Swap unreliable systems for dependable ones.
- Facilitation: Simplify tasks to minimize mistakes.
- Detection: Spot errors as soon as they occur.
- Mitigation: Lessen the impact of unavoidable mistakes.
These principles ensure process reliability: error prevention wins whenever possible and detection is the defense when errors happen. And poka yoke implementation is key because it uses advanced algorithms and real-time monitoring to minimize human error and create a quality culture in the process.
Types of Poka-Yoke Systems
There are two main types of Poka-Yoke mechanisms:
- Control Systems: Stop the process completely when an error is detected, no defective products move forward.
- Warning Systems: Use lights or alarms to alert operators of potential errors without stopping the process.
The poka-yoke is a structured approach to quality and production efficiency, using both prevention based methods to stop defects before they occur and detection based methods to detect and correct errors in the process.
Core Methods to Ensure Effectiveness
Each system uses one of three core methods to work:
- Contact Method: Detects physical deviations like size, shape or position.
- Fixed-Value Method: Ensures the right number of steps, repetitions or components in a process.
- Motion-Step Method: Monitors the sequence and timing of actions to make sure they are done in the right order.
These methods can be adapted to different processes, providing versatility across industries.
Examples of Poka-Yoke in Action
A poka yoke device is a tool designed to eliminate human errors in various processes. In manufacturing, examples include:
- Sensors on Assembly Lines: Detect misaligned parts before assembly.Counters in Packaging: Ensure every package has the right number of items.Color-Coded Connectors: Prevent mismatched components during installation.
Steps to Implement Poka-Yoke in Manufacturing
Assessing how effective the implementation of Poka-Yoke measures will be is critical before full implementation. Evaluate the specific errors that can be prevented and ensure that the selected error prevention measures do not interfere with the production process.
Effective implementation of Poka-Yoke requires a structured approach:
- Identify the Root Cause of Errors. Analyze your process to find where human and mechanical errors occur. This can be workflows, equipment or environmental factors.
- Choose the Right Technique. Choose the poka yoke method (contact, fixed-value or motion-step) that fits the problem. For example fixed-value method for repetitive tasks or contact method for shape deviation.
- Standardize the Process. Standardizing the process ensures consistency and reduces variation. Well defined process helps workers to understand their tasks and minimize errors.
- Train Employees. Give your team the knowledge to use Poka-Yoke systems. Training regularly helps workers to recognize errors and correct them fast.
- Integrate Digital Tools. Use smart manufacturing software to monitor and detect errors in real time. Connected systems can give instant feedback, so errors are corrected before they escalate.
- Monitor and Optimize. Continuously evaluate the Poka-Yoke mechanisms and improve them based on feedback and KPIs. This will ensure long term success and create a culture of continuous improvement.
Challenges in Poka-Yoke Implementation
While Poka-Yoke offers immense benefits, challenges can arise:
- Resistance to Change: Employees don’t want to change. Transparent communication and training will fix this.
- High Initial Cost: Some mistake-proofing systems require upfront investment. But the long term savings far outweigh the costs.
- Sustained Effort: Poka-Yoke is not a one time solution. Continuous monitoring and updates are needed to keep it effective.
Poka yoke focuses on preventing errors in manufacturing process, reduces learning time and minimizes reliance on memory. This is key to preventing human errors that cause defects, ensuring safety and efficiency in critical industries like automotive and aerospace. By solving these challenges, you can get the most out of error protection systems.
Conclusion
Poka-Yoke is more than just a technique; it’s a philosophy of prevention and quality. By integrating error-proofing measures into your processes, you can achieve zero defects, enhance customer satisfaction, and foster operational excellence.
Whether your industry involves assembling machinery, packaging products, or creating intricate electronics, Poka-Yoke techniques can help your business to reach new heights of efficiency, quality and innovation.
Simplify the way people work and learn at the frontline
See the industry-leading how-to platform in a 30-minute live demo.
Learn more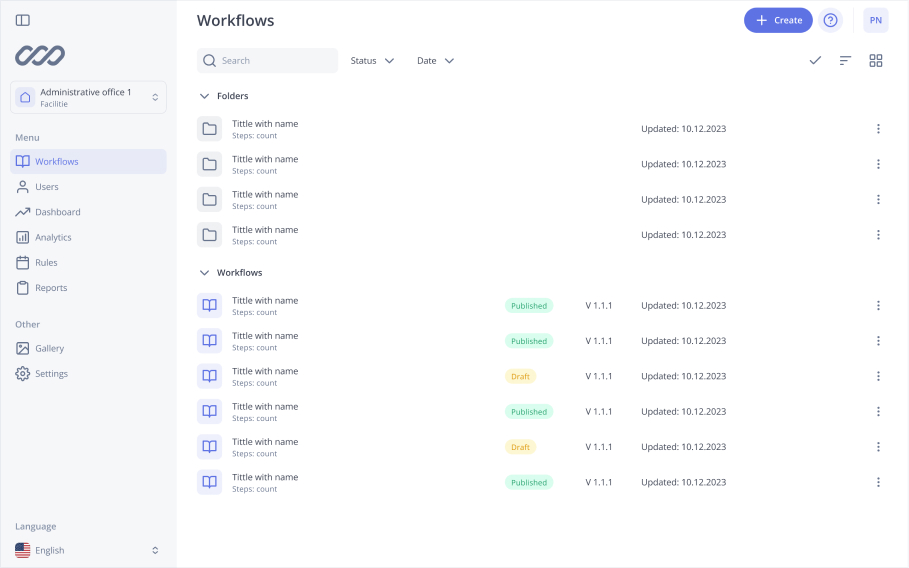
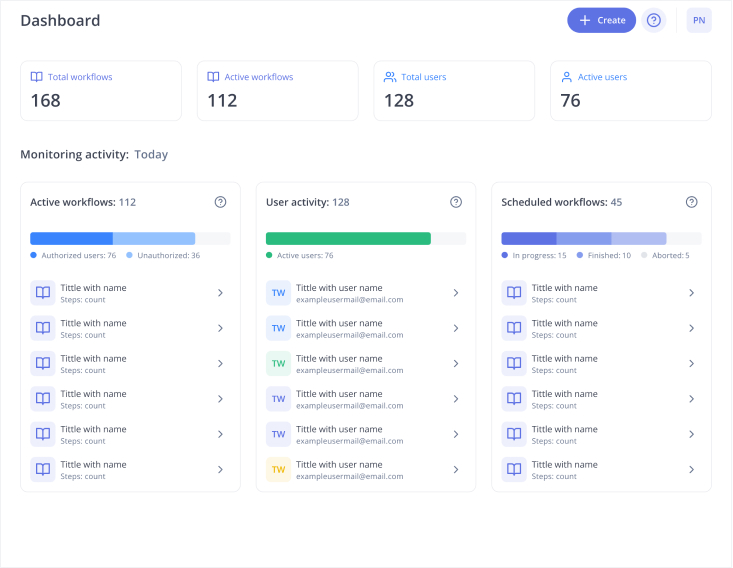