Plant Operator Rounds
Introduction
Operator rounds, especially plant operator rounds, are key to industrial operations, ensuring everything runs smoothly, is safe and equipment is maintained. These rounds involve routine checks, key performance indicators and identifying issues before they become major problems. In this article we’ll look at the importance of plant operator rounds, the benefits and how to optimise them for efficiency and reliability. We’ll also look at how digital operator rounds can increase operational efficiency by reducing administrative overhead, improving data quality and real-time visibility and empowering frontline workers as you transition from paper based processes to digital tracking systems.
What Are Plant Operator Rounds?
Plant operator rounds are scheduled, systematic checks performed by operators in industrial environments like manufacturing plants, power generation facilities and chemical processing units. These rounds typically include:
- Visual checks of machinery and equipment.
- Monitoring of critical parameters like temperature, pressure and fluid levels.
- Identification of abnormalities like leaks, unusual noises or vibrations.
- Logging into digital systems or manual checklists.
- Reporting to maintenance team for proactive action.
Monitoring equipment health is key to avoiding costly outages and smooth running. By doing these checks operators can ensure all systems are running optimally and reduce the risk of breakdowns and downtime.
The Role of Plant Operators in Industrial Efficiency
Plant operators are the first line of defense against equipment failures and operational inefficiencies. Their rounds help in:
- Equipment Reliability: Regular checks reduce mechanical failures.
- Compliance with Regulations: Inspections identify safety hazards and ensure industry standards.
- Reduced Downtime and Maintenance Cost: Catch issues early and prevent costly repairs and production halts.
- Energy and Resource Optimization: Monitor energy consumption and system efficiency for sustainability goals.
- Workplace Safety: Identify hazards ahead of time and reduce accidents and injuries.
Strategies for Effective Plant Operator Rounds
Industries must use best practices to improve operator rounds. Here’s how to do it:
Use Digital Tools for Data Collection on Mobile Devices
Paper checklists are being replaced by digital logbooks and mobile apps that make data collection and documentation of real-time inspection data easy. Mobile devices can access digital forms and collect inspection data in real-time making inspections faster and more accurate. Digital tools provide real-time tracking, automatic alerts and data driven decision making.
Use Predictive Analytics for Early Issue Detection and Equipment Health Monitoring
Integrating IoT sensors with operator rounds can provide real-time equipment condition monitoring through real time data collection. By analyzing data trends potential failures can be predicted and proactive maintenance can be done.
Standardize Inspection Procedures
Creating standard operating procedures (SOPs) ensures consistency in inspections. Well documented guidelines help operators follow same steps, reducing errors and oversights.
Train Operators Ongoing
Ongoing training programs keep plant operators updated on new technologies, best practices and safety regulations. Training improves inspection accuracy and troubleshooting capabilities.
Improve Inter Departmental Communication
Seamless coordination between operations, maintenance and management teams ensures that reported issues are addressed promptly. Mobile devices improve communication and data sharing between departments during operator rounds making the process more efficient. A centralized system for logging and tracking reported anomalies prevents communication gaps.
Use Machine Learning for Optimization
Advanced AI driven analytics can help optimize operator rounds by identifying trends and suggesting priority areas for inspection. Machine learning models can analyze past data to predict which components are most likely to fail.
Challenges with Operator Rounds
Despite the benefits of operator rounds:
- Human error: Manual checks can result in inconsistent data or missed issues.
- No automation: Industries that only manual monitor miss out on automated analytics.
- Resistance to Change: Some operators struggle to move from traditional to digital tracking.
- Data Overload: Without the right tools toanalyse data from checks, too much data becomes overwhelming and difficult to understand.
- Traditional Operator Rounds: Relying on old paper-based systems or siloed digital platforms can expose industries to significant financial risk due to unmonitored maintenance requirements. Modernizing these processes with AI and smart technology can improve predictive maintenance and operational efficiency.
By solving these challenges with technology, training and data management, industries can get the most out of operator rounds.
Future Trends in Operator Rounds
The future of operator rounds is being shaped by emerging technologies such as:
- Augmented Reality (AR) for Virtual Inspections: AR can provide operators with interactive overlays of equipment conditions and step-by-step guidance.
- Drones for Remote Monitoring: In large industrial settings, drones can perform high-risk inspections without human intervention.
- AI-powered Diagnostics: AI can analyze sensor data and operator logs to predict failures with higher accuracy.
- Blockchain for Compliance Tracking: Secure, immutable logs ensure regulatory compliance and accountability.
Additional Benefits of Optimized Operator Rounds
Apart from efficiency and safety, well planned operator rounds contribute to long term asset management strategies and operational efficiency. Documentation and trend analysis allows organizations to extend the life of assets, reduce capital expenditure and increase asset utilisation. A proactive approach to maintenance reduces costs and increases the reliability of critical operations, drives operational excellence.
Another key aspect of modern operator rounds is the impact on employee engagement. When operators are equipped with the right tools and training they can do their job better, so they become a more motivated workforce. Empowered operators contribute to a culture of accountability, safety and continuous improvement.
And finally integrating data analytics into operator rounds allows companies to identify bottlenecks in operations and optimize production schedules. This data driven approach means industrial processes stay agile and responsive to changing demands, ultimately increases profitability and operational resilience.
Conclusion
Plant operator rounds are the backbone of industrial operations, efficiency, safety and reliability. By using digital tools, predictive analytics and AI insight businesses can make rounds more effective, reduce risk and improve operational performance. As technology evolves the role of the plant operator round will become even more critical to industrial excellence.
Invest in smart inspection systems, operator training and real time monitoring and you’ll be ahead of the game and able to optimize your maintenance strategy. By prioritizing plant operator rounds you’ll achieve long term sustainability, reduce operational costs and improve workplace safety.
Simplify the way people work and learn at the frontline
See the industry-leading how-to platform in a 30-minute live demo.
Learn more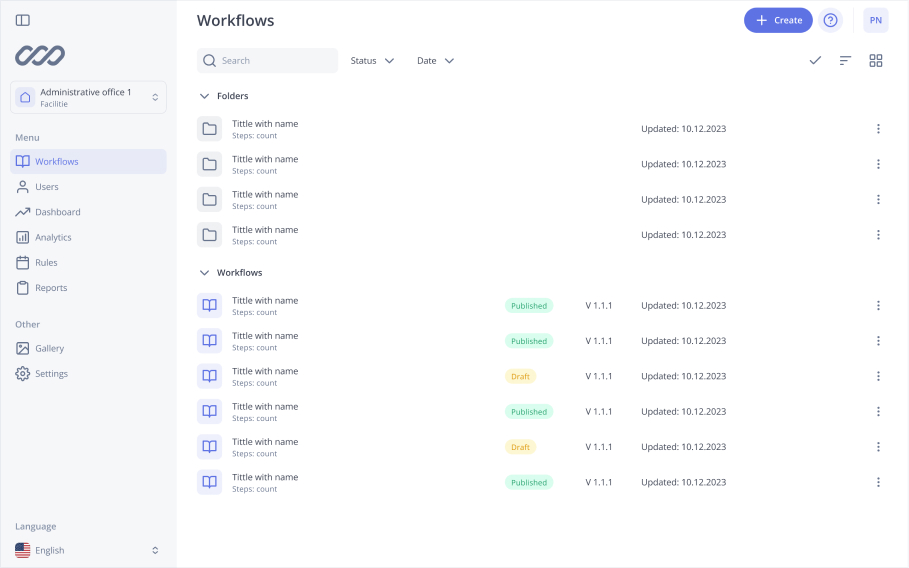
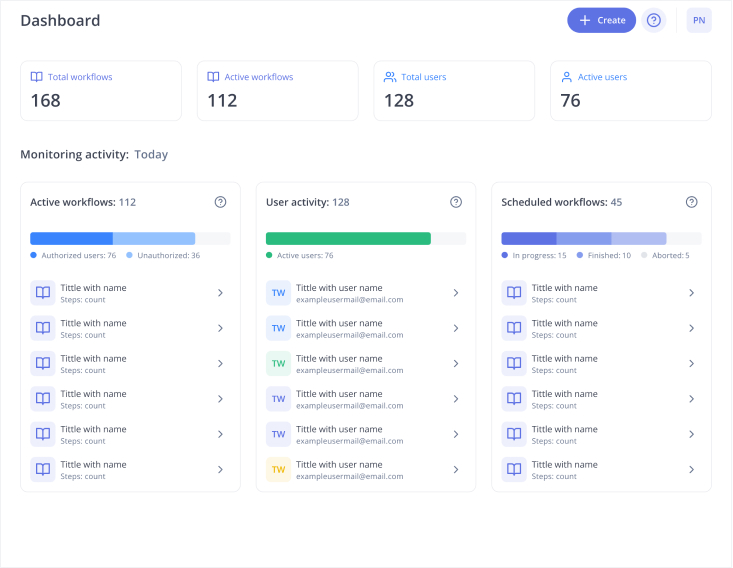