One Point Lesson
In the Lean and continuous improvement world, simpllicity and clarity are key. One of the best tools for that is the One Point Lesson (OPL). These short, focused training documents communicate specific, actionable knowledge in a clear and visual way, providing clear instructions for specific tasks. OPLs simplify complex processes by breaking down a complex process into manageable steps, helping employees grasp the basic meaning in quality standards and expectations for their role, while also building basic knowledge for effective job performance. Whether you’re introducing a new process, preventing recurring mistakes or creating a culture of continuous learning, OPLs are a game-changer for teams and organisations.
One Point Lesson Definiton
A One Point Lesson, also known as a Single Point Lesson, is a practical training tool that conveys one key piece of critical information, often related to a specific task. These documents are typically short — often just one page — and use simple language, supported by visual aids like diagrams, flowcharts or photos, which serve as visual instructions. This allows every team member, regardless of experience level, to quickly understand and apply the knowledge.
In industrial and operational environments, OPLs are often posted on machines or workstations as quick reference guides. OPLs frequently outline a specific procedure in a concise format. Their clarity and precision make them invaluable for learning new skills, understanding safety protocols or adopting best practices — without wading through bulky manuals or sitting through hours-long training.
Want to Get Started Quickly?
Download our One Point Lesson Template to create your first OPL in minutes.
One Point Lesson Objectives
1. Knowledge Transfer
The main goal of an OPL is to transfer knowledge on a specific topic or task. By breaking down complex procedures into bite-sized, digestible chunks, these lessons ensure that all team members — regardless of background — can understand and execute tasks correctly.
Whether it’s an operational method, a quality control tip or a safety instruction, One Point Lessons help eliminate knowledge gaps by identifying and addressing each knowledge gap in employee understanding, ultimately building employee confidence.
2. Preventing Mistakes
Mistakes cause inefficiency, rework, safety issues and waste; so error prevention is key to safe and efficient operations. OPLs prevent these by providing step-by-step instructions, highlighting common mistakes, identifying potential risks and sharing best practices. OPLs also tell workers what to do when a problem occurs so they can have an immediate and practical solution. Workers with clear, visual information are less likely to misinterpret tasks, resulting in fewer errors, smoother workflows and a quick fix for common operational issues.
3. Continuous Improvement
A Lean principle is kaizen, or continuous improvement. OPLs support this by promoting shared learning and a culture of daily, incremental progress, implementing improvements and sharing similar improvements across teams.
When teams regularly create, use and update OPLs it builds a collaborative environment that values improvement and encourages innovation, including introducing new concepts through OPLs. It also supports faster adaptation when standards or processes change and increases efficiency.
4. Standardization
Consistency means predictable and repeatable outcomes and consistent quality throughout operations. While full SOPs (Standard Operating Procedures) are valuable, they can be overwhelming. OPLs provide a more accessible, visual alternative — ideal for quick reinforcement of key procedures.
By using OPLs across different departments or shifts and standardising OPLs across other plants, companies can reduce variability, improve product quality and process control. It’s also important to have the department head review and approve OPLs for accuracy and effectiveness.
5. Communication and Collaboration
OPLs are also communication tools. They provide a clear and simple way to share information and capture team knowledge. When employees contribute to OPL creation, OPLs are created collaboratively and they take ownership of processes, so involving employees in creating OPLs that deliver the necessary knowledge and are more likely to follow and improve them.
With digital one point lessons it’s even easier to distribute updates, reduce onboarding time and eliminate departmental knowledge silos.
Why Do OPLs Work?
OPLs are effective because they are:
- Visual: Most include diagrams, photos, or illustrations to reinforce the content.
- Efficient: They deliver essential information in minutes, not hours.
- Focused: They address one specific topic, reducing information overload.
Single point lessons are a closely related concept, sharing the same concise and targeted approach to training and documentation.
In short, they deliver maximum impact with minimal complexity — making them ideal for lean manufacturing, health and safety, maintenance, and quality assurance, and are specifically designed to address real world scenarios employees face on the job.
How to Create an Effective One Point Lesson
Use a structured format and follow these principles. Using a digital format for OPLs allows for easier creation, distribution, and management, making lessons more accessible and up-to-date:
- Keep it Simple: One topic per lesson. Use plain, jargon-free language.
- Use Visuals: Incorporate photos, diagrams, or flowcharts to enhance understanding.
- Be Practical: Ensure the content is directly relevant to the job or process.
- Collaborate: Involve frontline employees to ensure the lesson is accurate and usable.
- Update Regularly: Revisit OPLs to keep them aligned with evolving standards and feedback.
- Leverage Digital OPLs and Digital Work Instructions: Digital OPLs and digital work instructions provide quick access and are managed in a central location, improving efficiency and consistency.
- Utilize Digital Solutions: Digital solutions streamline the creation and distribution of OPLs, ensuring everyone has the latest information.
- Concise and Visual vs. Text Heavy Documents: OPLs are more concise and visual compared to text heavy documents like SOPs, making them easier to understand and apply on the shop floor.
Examples of One Point Lessons
Here are some examples commonly used on the shop floor of what you can cover with a One Point Lesson:
- Correct way to store hazardous materials
- Quick check for machine calibration
- 5S workstation layout before/after photos
- PPE usage guidelines
- What to do when an error code appears on a machine screen
- Step-by-step sequence for daily maintenance tasks
- Safe equipment operation procedures
- Fire safety protocols and emergency response steps
- Standardized quality procedures for inspections
- Safety OPLs covering first-aid or risk awareness
- How to identify problems during production runs
- Tips for completing tasks efficiently and accurately
Each of these focuses on one concept, reinforcing consistent, high-quality performance.
How OPLs Impact Organizations
Done well, One Point Lessons can redefine how knowledge is shared and retained across departments. They simplify training, reduce onboarding time, and are especially useful for training new employees by providing clear, concise guidance that ensures consistent task execution and compliance. OPLs also support lean initiatives.
Organizations that implement OPLs experience:
- Higher Efficiency: Workers spend less time troubleshooting and more time doing the job right
- Improved Quality: Standardized methods deliver more consistent outcomes
- Increased Safety: Fewer accidents due to better communication of safety procedures
- Regulatory Compliance: Well-crafted OPLs help ensure adherence to industry regulations and standards during various processes
- Stronger Teamwork: Sharing knowledge builds a sense of community and mutual support
Summary
The One Point Lesson is more than just a visual training tool — it’s a cornerstone of efficiency, standardization, and continuous improvement. It aligns with the Lean philosophy by eliminating unnecessary complexity and making learning part of everyday work.
In an increasingly fast-paced and change-driven world, clarity and speed of knowledge transfer are vital. Whether you’re a production supervisor, quality specialist, or operations leader, introducing OPLs can make a measurable difference in outcomes.
Simplify the way people work and learn at the frontline
See the industry-leading how-to platform in a 30-minute live demo.
Learn more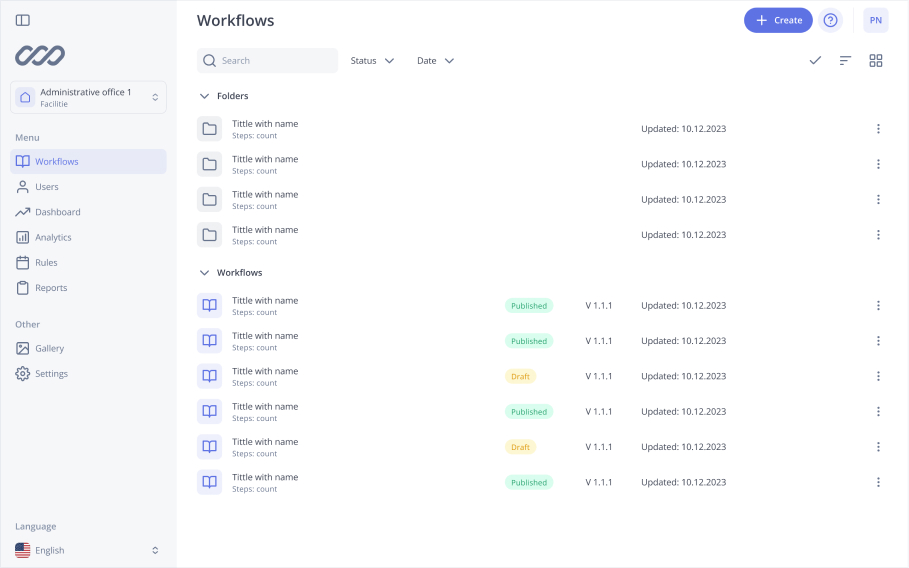
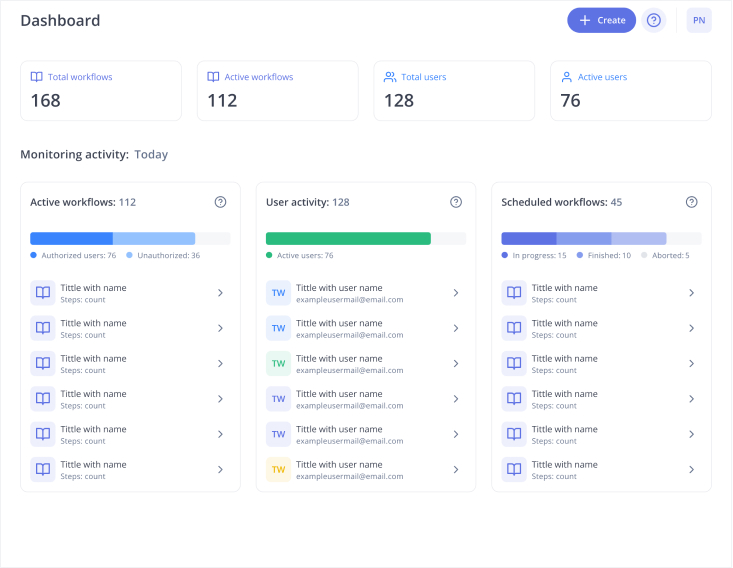