Gemba Walk
Enhance workplace engagement with practical tips for mastering Gemba. Discover effective strategies to connect with your team.
Definitions
Gemba
In Japanese, gemba means “the place where the main actions take place.” Being in the actual place where work is done is key to understanding processes and solving problems. From a management point of view, gemba is where the workflow is executed.
Gemba Walk
Gemba walk is an approach where the manager goes to gemba, gets the information and makes the decisions. In the Japanese management model, it is believed that management should know how the production process works.
The Gemba Walk prevents the gap between the management’s vision and what is happening in the employees’ workplaces. Effective Gemba Walks are key to finding continuous improvement opportunities and process improvement. They help managers to see operations on the floor, to create a quality culture in the organization.
Safety Gemba Walk
Safety gemba walk is a combination of gemba walk and safety walk. This type of gemba walk is to find ways to improve workplace safety and how to implement them.
Main Elements of Gemba Walk
1. Gemba
Go to the workplace where the error was reported from the production stage. Check if all processes are done according to the norms and if gross errors are allowed. This will give the manager a fresh view of what is happening in the workplace. It is important to get information during Gemba walk without interfering with the employees.
2. Gembutsu
Gembutsu means “something real” in Japanese. In gemba, it can mean “machine tool”, “tool”, “product” or “customer request or complaint”. If there is a problem, managers should go to gemba and check the gembutsu.
3. Reason
Try to take temporary countermeasures first. But don’t dwell on them – you always need to find the root cause. The question “why?” is one of the most useful tool in gemba. Employees who use gemba in their work believe that sometimes it is enough to ask it five times – the method is called “The 5 Whys”. Active communication combined with 5 Whys is key to find the root cause of the process problems. Gemba walk as a structured approach helps to solve problems and engage employees.
4. Standartization
When you have created a procedure that will solve the problem found in the previous step or prevent it from happening in the future, then standardize the procedure. Standardization will be the last step of the continuous improvement cycle.
Steps for Effective Gemba Walks
To conduct an effective Gemba walk, leaders should:
1. Notify employees about your plans
Employees will feel more comfortable if they know in advance that you are going to do a gemba walk. If you go to the factory floor or work area suddenly, employees will feel uncomfortable and will worry that something has happened that they were not informed about. It is important to schedule your Gemba walk in advance to not make employees feel uneasy. Planning and doing Gemba Walks as part of a structured approach will improve workplace efficiency and employee engagement.
2. Prepare the questions to get the necessary information
Preparation is key to do effective Gemba walk. It is also important to prepare Gemba walk questions in advance to have effective discussion. You can use the 5 Whys method to get all the information needed to solve the problem during gemba walk.
3. Respect Your Employees
Do not interfere with the workflow as soon as you notice any flaws. By doubting the professionalism of your employees, you undermine their trust and provoke an increase in stress. Collaborate with your employees in the problem-solving process and don’t forget that the main purpose of gemba walks is to observe to identify and eliminate flaws. Showing respect is essential for gaining employee buy-in for quality initiatives.
4. Observe, write down, make conclusions
You and your employees can also use digital checklists, describe the problems there, if needed, attach photo or video and get a hint to solve the problem as fast as possible. A Gemba walk checklist can guide your observation and discussion. Also consider to do virtual Gemba walk using communication tools like video conferencing. This way managers can do one-on-one video calls, focus group discussion and screen-sharing to observe employees in real-time and engage with them through questions.
5. Find the Solution
After the gemba walk and entering the data into digital checklists, share your thoughts with employees, discuss the solutions and changes in the process with them. Determine which procedure to standardize. Analysis and feedback after the Gemba walk is key to prepare for the next Gemba walk.
Conclusion
The Gemba Walk system is an important tool for improving operational efficiency and solving problems, as well as an important management tool because it allows managers:
- To observe the problems directly.
- Communicate directly with employees.
- Identify the root causes of problems.
- Expand the capabilities of teams and promote continuous improvement.
- Make data-driven decisions in a real-world context.
Ultimately, Gemba Walk helps to develop a culture of collaboration, problem solving and accountability, which leads to increased efficiency, quality and effectiveness in the organization as a whole.
Simplify the way people work and learn at the frontline
See the industry-leading how-to platform in a 30-minute live demo.
Learn more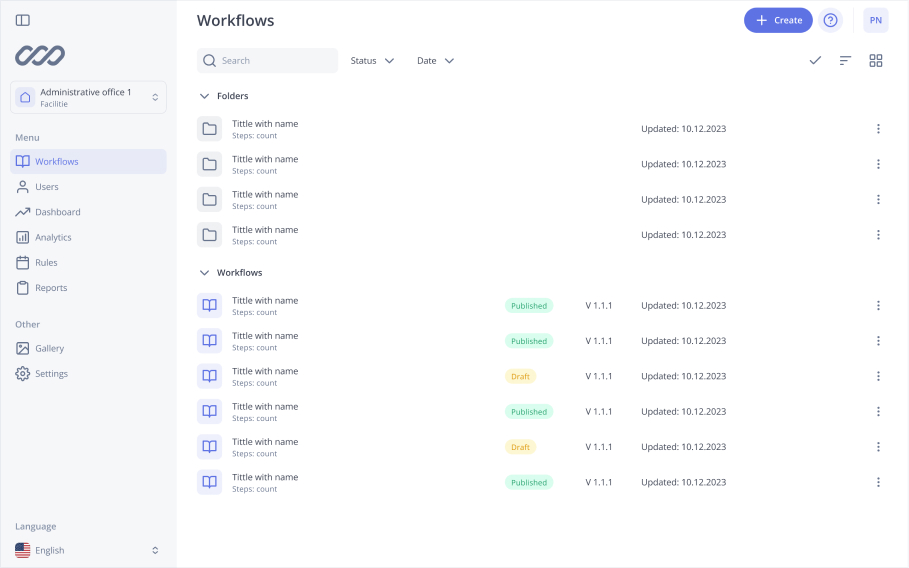
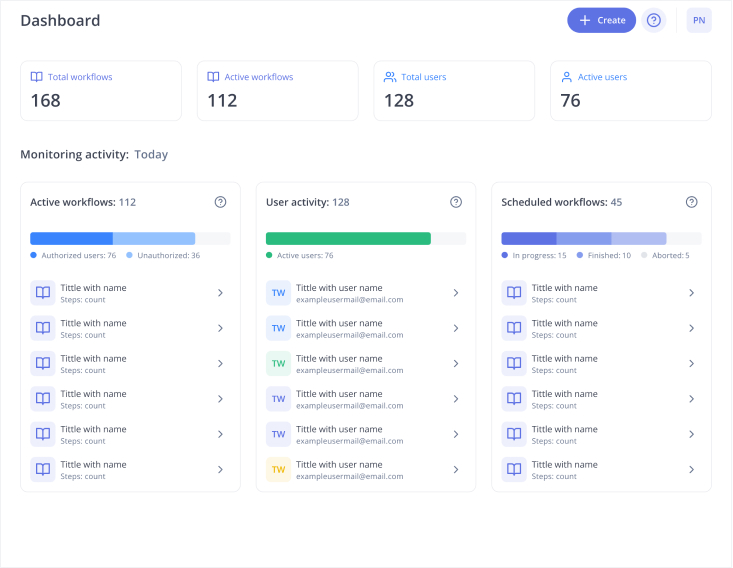