Maintenance Management
In today’s industrial and commercial world, maintenance management is key to operational efficiency, asset performance and downtime minimization — all of which are critical to business success. From manufacturing plants to healthcare facilities, maintenance is no longer an afterthought — it’s a strategic priority. In this guide we will explore what maintenance management is, why it matters and how using a maintenance management program or CMMS software can boost productivity and cost savings.
What is Maintenance Management?
Maintenance management is the process of overseeing and controlling maintenance activities and maintenance processes within an organization to ensure assets run efficiently and reliably. This includes scheduling preventive maintenance, managing maintenance tasks, allocating resources and tracking maintenance costs.
The goals of maintenance management are simple yet vital:
- Extend the life of physical assets
- Minimize equipment downtime
- Reduce maintenance costs
- Ensure safety and compliance
- Improve asset performance
Types of Maintenance
Understanding the several types of maintenance management is key to implementing a maintenance strategy:
- Preventive Maintenance (PM): Scheduled inspections and servicing to prevent equipment failure.
- Predictive Maintenance (PdM): Uses data and sensors to predict when maintenance should occur.
- Reactive Maintenance: Also known as breakdown maintenance, it occurs after equipment fails.
- Routine Maintenance: Regular and repetitive tasks like cleaning, lubrication etc.
- Condition-Based Maintenance: Maintenance based on the actual condition of equipment.
- Reliability Centered Maintenance (RCM): A structured approach to maintaining system functionality.
Maintenance Management System
A maintenance management system is all the tools, processes and policies used to manage maintenance activity. A well-structured system simplifies maintenance, reduces manual errors and improves decision making.
Computerized Maintenance Management Systems (CMMS)
The adoption of computerized maintenance management systems (CMMS) has changed the way organizations manage maintenance. CMMS software automates scheduling, manages maintenance requests, tracks inventory costs and generates maintenance reporting metrics.
Benefits of using a computerized maintenance management system (CMMS) include:
- Automated preventive maintenance scheduling
- Better resource allocation
- Real time monitoring of maintenance data
- Improved coordination of maintenance teams
- Mobile access to work orders and asset history
Preventive Maintenance: The Foundation
Preventive maintenance (which includes regular maintenance) is the backbone of any proactive maintenance management program. It helps in:
- Reducing unscheduled repairs
- Extending asset life
- Avoiding equipment downtime
- Lowering long term operating costs
Implementing an effective preventive maintenance program involves:
- Identifying critical assets
- Creating a maintenance schedule
- Assigning tasks to maintenance technicians
- Using CMMS to monitor compliance
Predictive Maintenance: Smarter Decisions
Predictive maintenance uses AI, IoT sensors and analytics to forecast failures and monitor asset health. Unlike preventive maintenance which is time based, predictive maintenance is condition based and more efficient.
For example vibration analysis or thermal imaging can detect anomalies before a failure occurs. This means:
- Less unexpected maintenance
- Less material waste
- Better asset management
Maintenance Management Software: Beyond CMMS
Beyond traditional CMMS, modern maintenance software including EAM software integrates with enterprise asset management (EAM) and enterprise resource planning (ERP) systems. This holistic approach allows you to:
- Link maintenance to finance and HR
- Optimize inventory management
- Uncover maintenance trends
- Drive continuous improvement
Maintenance Strategy and Planning
Choosing the right maintenance strategy and planning maintenance schedules depends on the type of assets and operational goals. A balanced approach of preventive, predictive and reactive maintenance gives you flexibility and cost savings.
A good strategy includes:
- Clear objectives
- Defined roles for maintenance managers
- KPIs for asset performance and downtime
- Regular audits and feedback loops
Maintenance Tasks and Teams
Managing maintenance tasks efficiently requires a structured workflow within the maintenance department. Maintenance managers must:
- Prioritize work orders based on urgency
- Ensure parts availability via inventory managers
- Allocate skilled maintenance workers
Good maintenance teams are collaborative, trained and tech savvy. Training programs and mobile maintenance software empowers technicians to work smarter.
Maintenance Costs and Optimization
One of the top goals of any maintenance management program is to reduce maintenance costs without sacrificing quality. Techniques for optimizing maintenance costs include:
- Leveraging data from CMMS
- Implementing preventive maintenance strategies
- Conducting root-cause analysis for recurring issues
- Streamlining procurement for spare parts and effective materials management
Asset Management and Performance
Proper asset management ensures long-term sustainability. It involves lifecycle tracking from procurement to disposal. Key practices include:
- Regular performance audits
- Setting benchmarks for an asset’s life
- Using data to improve asset performance
Effective maintenance management directly impacts ROI by reducing capital expenditures and prolonging equipment usability.
Scheduling and Resource Allocation
Maintenance scheduling is a juggling act. It needs to consider:
- Asset criticality
- Technicians’ availability
- Equipment operating hours
Schedule preventive maintenance during off-peak hours to avoid disruptions. Use CMMS to automate recurring tasks and reminders, and to track inventory usage. Efficient resource allocation also reduces idle time and enhances technician productivity.
Maintenance Management Tools and Trends
With rapid technological advancements, maintenance management tools are becoming smarter. From AI-based diagnostics to drones for inspection, new and emerging technologies, including integrations with accounting software, are transforming the maintenance landscape.
Current maintenance trends include:
- Shift from reactive to predictive maintenance
- Use of AR/VR for training and diagnostics
- Cloud-based CMMS maintenance software
- Integration with IoT and smart sensors
Inventory and Facility Operations
Good inventory management means spare parts and consumables for your physical assets are always available. Overstocking means high inventory costs, understocking means downtime.
Facility operations rely heavily on maintenance. Clean environments, functional systems and well-maintained equipment means safe and compliant workspaces.
Conclusion
Investing in a good maintenance program and maintenance care is not a luxury it’s a necessity. A maintenance management system enables you to manage your assets efficiently, reduce costs and improve service delivery.
The combination of technology, strategy and human expertise is what makes good maintenance management. Whether it’s CMMS software, preventive maintenance scheduling or skilled maintenance technicians a forward thinking approach to maintenance is essential for any business that wants to be long term and competitive.
Businesses that adopt smart maintenance will not only extend asset life but also get a big edge in operational resilience, cost control and asset optimization.
In the age of Industry 4.0 maintenance is not about fixing what’s broken it’s about predicting, preventing and perfecting every aspect of asset utilization. And that’s what modern maintenance management is all about.
Simplify the way people work and learn at the frontline
See the industry-leading how-to platform in a 30-minute live demo.
Learn more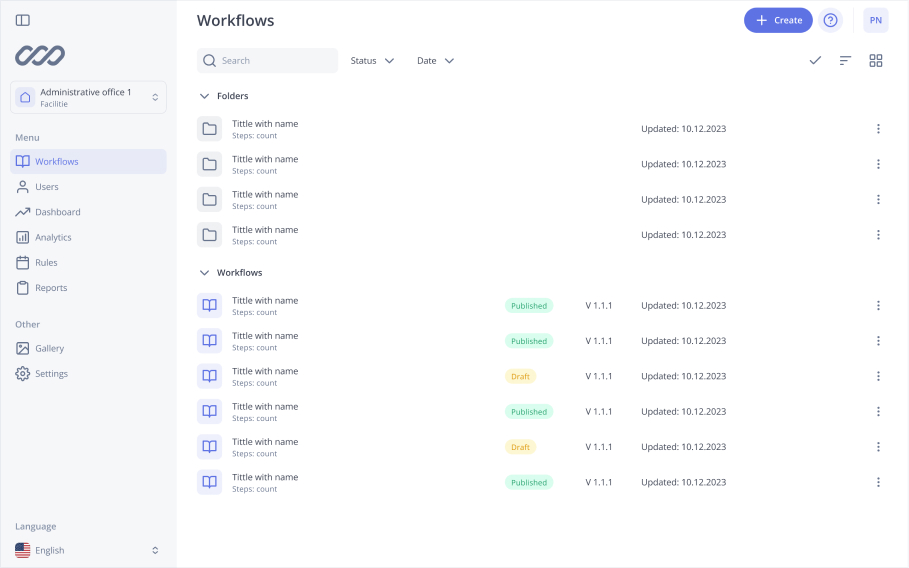
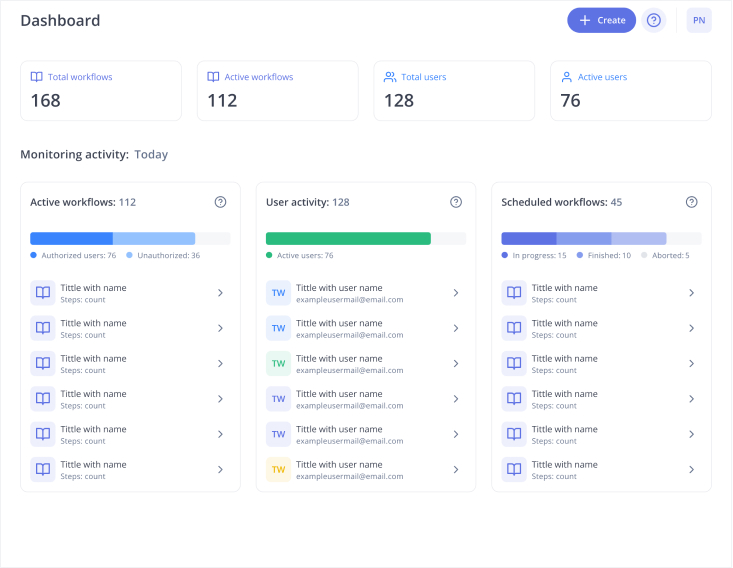