Hidden Factory
Not all processes run as smoothly as they seem. Beneath the surface of a normal operation is what’s called the Hidden Factory — a collection of inefficiencies, waste and rework that’s invisible yet impacts productivity and profit. Understanding this concept and eliminating it is key for companies that want to improve their operations and quality. The Hidden Factory is like a silent drain on resources, sucking away profits and customer satisfaction. By addressing it, manufacturers can get big gains in performance and bottom line.
What is the Hidden Factory?
The term “Hidden Factory” was coined by Armand V. Feigenbaum, the father of Total Quality Control. The hidden factory refers to a critical concept in manufacturing that introduces inefficiencies and variations in processes. It is the part of the company’s manufacturing system that operates outside of the standard value added processes. The Hidden Factory is the undocumented or non-conforming procedures in manufacturing that cause inefficiencies and variations in the process. This hidden segment consists of defects, rework, inefficiencies and unmeasured losses that consume resources without adding to the finished product. Think of it as the “dark side” of manufacturing — activities that don’t show up on the official reports but still cost time, money and effort.
These aren’t always visible but the impact is huge. They cause increased production costs, delays, excess material usage and higher energy consumption. The Hidden Factory is the total of all non-value added activities in a process that can significantly increase operational costs and inefficiency. Identifying and addressing these inefficiencies can yield big cost savings and better product quality. The Hidden Factory is not just for big manufacturers; it’s a universal problem in the industry.
Components of the Hidden Factory in the Manufacturing Process
The Hidden Factory consists of:
- Rework and Scrap: Defective products that need to be fixed or thrown away increase material costs and product waste. This is the most visible part of the Hidden Factory as it hits the bottom line.
- Unnecessary Steps: Extra processing steps that do not add value, often due to old processes or poor workflow design. These steps slow down production and increase labor costs.
- Equipment Downtime: Machines breaking or running inefficiently due to poor maintenance practices. Downtime not only stops production but also rushes work when production resumes and increases the likelihood of mistakes.
- Defective Materials: Low quality raw materials that need extra processing or product failure. This can come from bad suppliers or lack of quality checks.
- Overproduction: Producing more than what is needed and ending up with excess inventory and holding costs. Overproduction is often due to bad demand forecasting or poor planning.
- Inefficient Labor: Employees spend time on non-value adding activities like waiting for materials or fixing errors. This not only wastes time but also demotivates employees.
- Poor Data Usage: Lack of real time monitoring and analysis leading to delayed decision making and missed opportunities. In today’s data driven world not using data is a big mistake.
Finding these inefficiencies is key to getting rid of waste and improving productivity.
Finding the Hidden Factory
The biggest challenge with the Hidden Factory is it operates outside of traditional metrics. Since many of its inefficiencies are invisible, companies must take proactive steps to find them. Here is how:
- Data Analysis: Use advanced data collection and analytics to monitor production performance and find areas of waste or delay. Modern software tools can show you things you could never see before. Look at cycle time differences between shifts to find inefficiencies and hidden factory issues.
- Root Cause Analysis: Investigate recurring defects and inefficiencies using tools like the 5 Whys or Fishbone Diagram (Ishikawa Analysis). These tools help drill deeper into the root cause of problems. Long cycle times mean issues like rework and waste are hidden in the factory.
- Six Sigma Techniques: Use Six Sigma techniques to uncover and address hidden inefficiencies within manufacturing processes. These techniques are critical for revealing waste and flaws that impede production and quality, and they systematically eliminate defects through statistical analysis and structured methodologies.
- Lean Manufacturing Techniques: Use Lean principles like Value Stream Mapping to visualize and eliminate non-value added activities. Lean is designed to expose waste and streamline processes.
- Standard Operating Procedures: Emphasize the importance of establishing standard operating procedures (SOPs) for standardizing processes and ensuring consistent quality in manufacturing. SOPs help maintain control over processes, reduce variations and defects, and lead to more efficient operations and improved training for employees.
- Employee Feedback: Encourage workers to report inefficiencies, bottlenecks and quality issues that may not be visible to management. Frontline employees have the best view of what is going wrong. Manufacturing managers should engage with other departments and look at key metrics like inventory levels and process constraints to get a full view of the factory.
- Gemba Walks: Go to the production floor regularly to see what is happening and find sources of waste in real time. This hands-on approach helps leaders see problems firsthand. Look at activities and performance metrics on the factory floor and plant floor to find issues like too much inventory and variations in process execution.
Removing the Hidden Factory
- Six Sigma: Use Six Sigma methodologies like DMAIC (Define, Measure, Analyze, Improve, Control) to systematically reduce defects and inefficiencies. Six Sigma is a structured problem-solving approach. Six Sigma is used to find and eliminate inefficiencies, waste, and defects in the process.
- Automate Where Possible: Invest in automation to reduce human error and improve efficiency. Automation does repetitive tasks and frees up employees for more value-added work.
- Improve Maintenance Strategies: Implement predictive maintenance to reduce equipment downtime and prevent unexpected failures. Predictive maintenance uses data to prevent problems before they happen.
- Reduce Variability: Control variability in processes through tighter quality control and supplier management. Consistency is the key to removing waste.
- Improve Training Programs: Train employees on Lean principles, process efficiency and how to reduce waste. Well-trained employees are more likely to spot and address inefficiencies. Training programs should also focus on process improvements to continuously improve the manufacturing process. Additionally, training employees in standard operating procedures (SOPs) ensures consistent quality and efficiency.
- Optimize Inventory Management: Implement Just-In-Time (JIT) to prevent overproduction and reduce storage costs. JIT ensures materials are available only when needed.
Benefits of Removing the Hidden Factory
By finding and removing the hidden factory for operational efficiency, manufacturers can get:
- Cost Reduction: Decreasing waste and rework reduces production costs. Every dollar saved on inefficiencies goes straight to the bottom line. By identifying and eliminating non-value-adding activities within the production process, companies can significantly reduce costs.
- Better Product Quality: Fewer defects result in higher customer satisfaction and lower warranty claims. Quality is a key differentiator in competitive markets.
- Greater Efficiency: Process optimization leads to shorter production cycles and better resource utilization. Efficient operations can handle more volume without increasing costs. Fixing the hidden factory can lead to big productivity and profit improvements.
- Competitive Advantage: Companies that optimize their operations can offer better price and higher quality in the market. This makes them stronger against competition.
- Sustainability Gains: Reducing material waste and energy consumption supports green manufacturing. Sustainability is becoming more important to customers and stakeholders.
Conclusion
The Hidden Factory is a silent profit killer. But by finding and fixing inefficiencies and implementing strategic improvements manufacturers can transform their operations, reduce waste and be more efficient. It is all about continuous monitoring, employee involvement and quality management. Companies that fix their hidden factory will get a big competitive advantage and better products at lower cost. In today’s rapidly changing world of manufacturing, repairing a hidden factory is not just an opportunity, it is a prerequisite for long-term success. By exposing those hidden inefficiencies businesses can unlock their full potential and grow sustainably.
Simplify the way people work and learn at the frontline
See the industry-leading how-to platform in a 30-minute live demo.
Learn more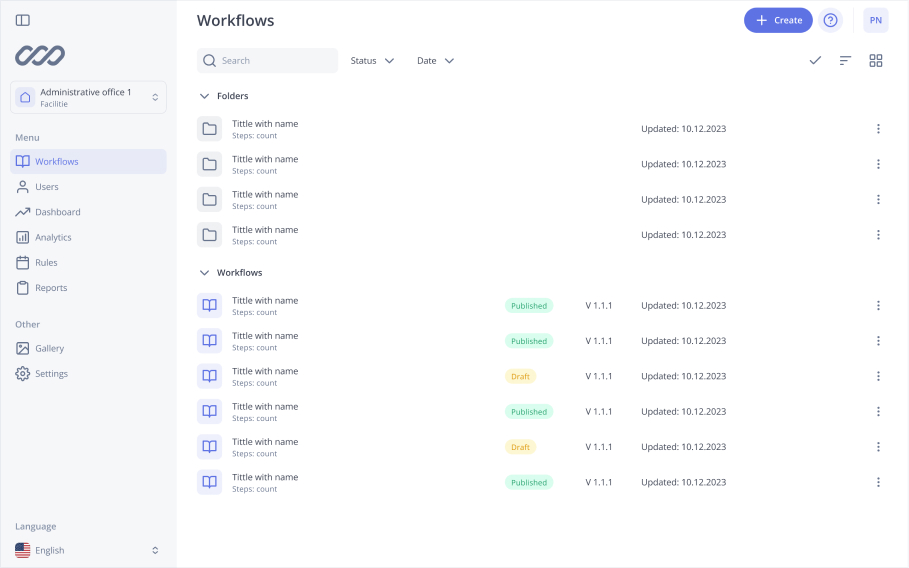
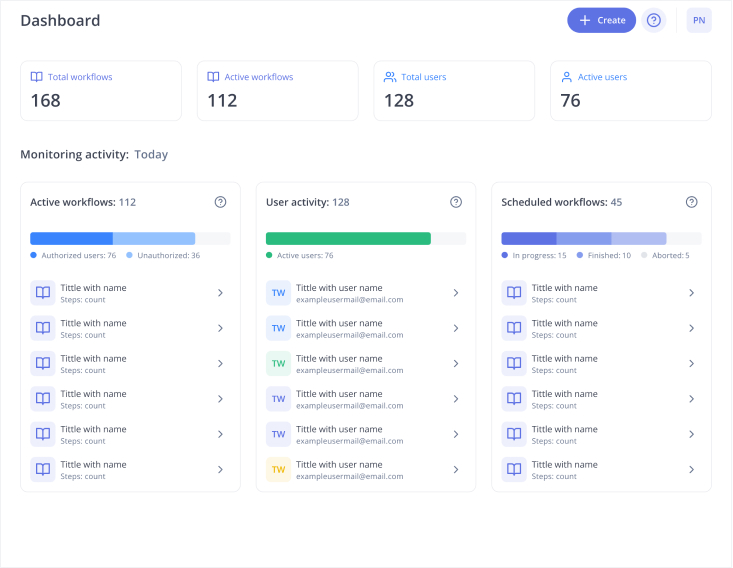