Digitization in Manufacturing
Manufacturing is changing rapidly, and technology is driving this process. They are affecting every part of the production process, from automating tasks to using analytics to make better decisions. One of the biggest changes is the move to paperless manufacturing, allowing real-time visibility of the shop floor. Digitised data from digitization improves production efficiency by making information more visible and manageable, as well as enabling human-machine interaction.
What is Digital Transformation in Manufacturing
Digital transformation in manufacturing is the integration of digital technologies, tools, workflows and approaches into every part of the business, making manufacturing more agile and efficient. It’s not just about tools, but people, processes and technology.
Why is Digitization Important in Manufacturing?
Digitization is key for manufacturing companies who want to stay competitive, reduce costs and increase efficiency. The digitization process brings inefficiencies, from reporting errors to delays caused by old processes. These can stop production, create waste and impact profitability.
As processes change in manufacturing, documentation must keep up. Paper-based systems are hard to update and prone to errors, resulting in inconsistent procedures and rework. By digitizing manufacturing processes, you can avoid these and make sure workers have the latest information.
Key Benefits of Digitization in Manufacturing
- Transparency and Real Time Data: Digitization provides immediate access to digitized data, better decision making and visibility. Real-time analytics helps to find inefficiencies and opportunities to improve.
- Consistency Across Processes: Digital systems standardize procedures so tasks are done the same way no matter who they do. This reduces variability and improves quality.
- Increased Worker Productivity: By replacing paper-based methods with digital tools workers can complete tasks faster and more accurately.
- Safer Workplaces: Digital systems can embed safety protocols into workflows so workers can follow guidelines and avoid accidents.
- Less Waste and Costs: With digitized processes you can optimize resource usage, reduce overproduction, material waste and energy consumption. That saves costs and supports sustainability.
- Better Planning: Real time data from digitized systems allows for better planning and scheduling, less equipment downtime and no problem areas in production.
Digital Solutions for Manufacturing companies
The goal of manufacturing digital transformation is to have real time visibility and simplify tasks for workers. To do that you have to approach digitization of current processes step by step:
1. Review Current Systems
Start by reviewing your paper forms and identify areas to digitize. Focus on high impact processes like standard operating procedures (SOPs), work instructions and compliance reporting. Paper-based methods are inefficient, delayed updates and manual errors so they are prime candidates for digitization.
2. Implement Smart Technologies
Digitization often means digitalization – using technology to automate manual processes. Using tools like IoT (Internet of Things) devices, AI (Artificial Intelligence) and machine learning can simplify operations and decision making. Examples include:
- Industrial IoT Sensors: Monitor production lines and track KPIs.
- Machine Health Monitoring: Detect issues before they become problems, reduce downtime.
- AI-Powered Tools: Automate repetitive tasks and provide data driven insights.
- Predictive Maintenance: Continuously monitor asset health to avoid unexpected failures and downtime.
3. Use a Central Hub
To manage digitized processes with digital technology, use a cloud based platform that consolidates all data and operations. This allows workers, machines and management to communicate seamlessly. Customizable dashboards can be built to meet business goals, to show KPIs and progress.
4. Digital Workflows for Workers
When you go digital prioritize usability. Make sure the digitized instructions are clear, short and easy to follow. Add visual aids like diagrams, videos or step-by-step guides to help understanding.
5. Involve Leadership and Workers
For digitization to work, you need it to be noticed at all levels of the organization. Leadership should promote the initiative and long-term benefits. Workers should get training on new systems and can give feedback to create a culture of collaboration and continuous improvement.
Challenges
Digital transformation in manufacturing is good for industrial companies but not without challenges.
- Investing in the Right Technology: Digital transformation relies on new technology to modernize the manufacturing industry, but finding and implementing the right tools is tough.
- Change Management: Change management is one of the most significant hurdles in digital transformation. Resistance from employees or leadership can slow down progress and impact worker safety.
- Onboarding, Training, Reskilling: As manufacturing goes digital the skill requirements for workers change. Ensuring the workforce is ready to work with new tools is key to success.
- Scale across the organization to avoid silos: Digital transformation initiatives often start in one department or location. Without scaling properly these will create silos that will limit the benefits of organization wide adoption.
Conclusion
Digitization is a must for a manufacturing company to stay relevant in today’s fast-paced industry. By replacing paper-based systems with digital tools, manufacturers can increase efficiency, productivity and accuracy in all processes. The use of real-time data, automation of tasks and standardization of procedures will lead to improved product quality, safety and cost.
Simplify the way people work and learn at the frontline
See the industry-leading how-to platform in a 30-minute live demo.
Learn more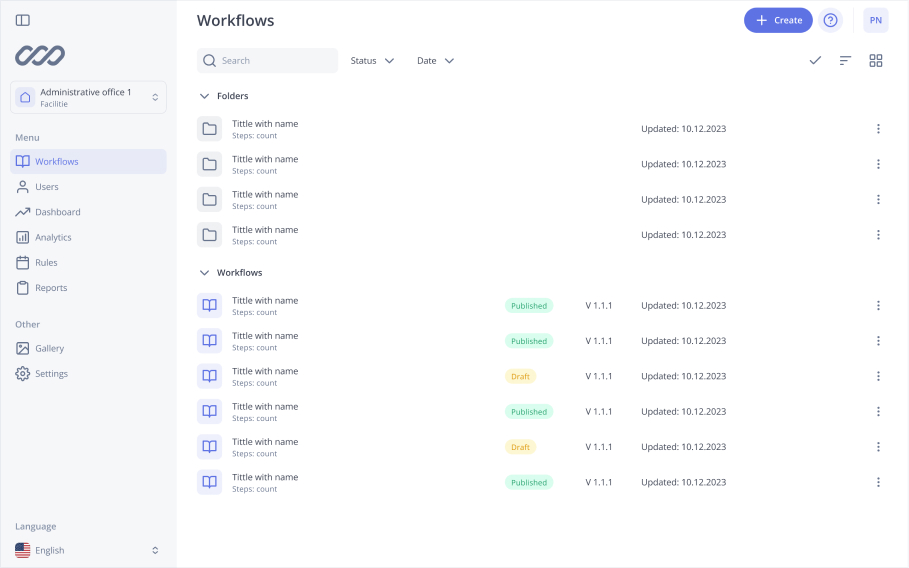
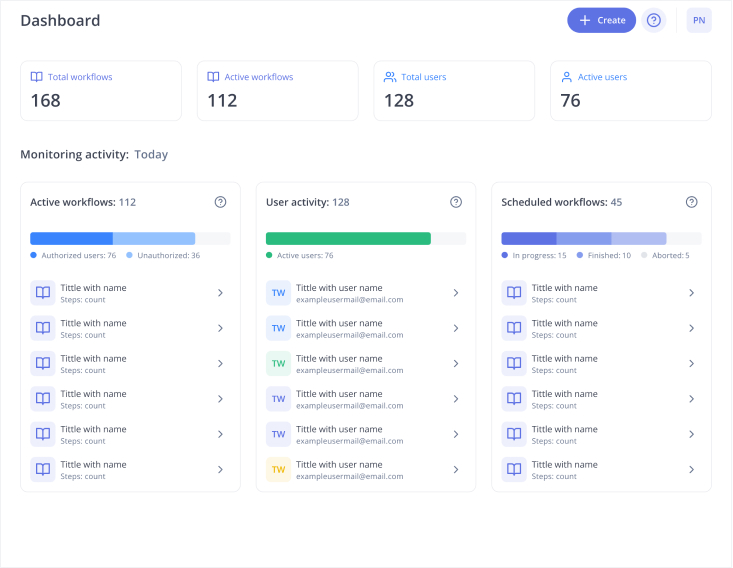