Standardized Work
What is the Standardized Work?
Standardized work processes are tools that allow you to document the standard for performing tasks in production in a certain sequence, ensuring the safety of the work performed while maintaining quality and deadlines, due to continuous improvement by eliminating losses. Standardized work is one of the components of Lean manufacturing.
Standardized Work vs Work Standards
The first thing to note is the difference between the concepts of “work standards” and “standardized work”.
The first concept focuses on the process, that is, standardizes the process. Working standards are set during product and process development. They include work that must be done in such a way that the product is produced as intended when designing that product or service. Formalized documents reflect the main steps of the process and are considered immutable, developed forever (to be more precise, their changes are extremely lengthy, complex and filled with a large number of errors).
The second concept focuses on the customer and his needs. It applies the best experience and is flexible and constantly changing. Unlike the formalization of the process steps, as in the first case, the method formalizes the steps that add value to the product. The main importance for production are the three main conditions of standardized work, which are described in more detail below. Standardized work contributes to customer satisfaction by ensuring high-quality products and services. The Toyota Production System (TPS) plays a foundational role in the development and implementation of standardized work, emphasizing continuous improvement and stability.
Main Components of Standardized Work
There are three main conditions for the implementation of the standardized work method, without which the implementation of the method will not give the necessary results:
- Takt Time, Cycle Time or Takt.
It is a manufacturing term describing the required assembly time of a product required to meet customer demand. And on the other hand, Takt Time is the time limit of the process capabilities.
- Work Sequence.
It implies the sequence of actions of the employee, and not the movement of the product, tool or components. The lack of a constant repeatable sequence leads to the performance of work in various ways, which leads to various errors (defects, breakdowns, improper performance of work and alterations).
- Standard Inventory or In-process Stock.
It is the minimum amount of raw materials and in-process inventory before each operation (stage of the process) required to maintain a smooth flow. The minimum stock of in-process inventory should be calculated based on the time of the cycle, recalculated together with changes in customer needs or standard documentation.
Also, the success of the implementation of the method lies in the active involvement of employees in the process of changes, as well as in the development of standard working documentation.
How to Implement Standardized Work?
The implementation of standardized work can be carried out according to the PDCA cycle:
P – Plan. Collect the available standards and regulations. Organize the work processes, develop work standards, taking into account safety and quality issues.
D – Do. Visualize the main documents of standardized work and conduct staff training (including training of new employees) based on these documents. Use a job breakdown sheet for documenting and standardizing tasks during staff training. Place these documents on the work site, taking into account the circle of persons to whose work process these documents are relevant.
C – Check. After the implementation of standardized work, further monitor the process, identify problem areas that prevent compliance with standardized work.
A – Act. Having identified errors in stage 3, to improve the standardized work. It is important to eliminate the main reasons why work process is disrupted.
Common Challenges
Different execution times for the same workflows. At the first stage of the PDCA, it is necessary to fix all the causes of fluctuations in the execution time of the workflow and eliminate these causes.
Release of low-quality products. Low-quality materials and spare parts lead to work stoppage and additional costs for error correction.
Frequent unplanned equipment shutdowns. It is impossible to organize standardized work without a stable, constantly working production line.
Lack of practical skills in standardized work. Workers with a lack of practical skills hurriedly send low-quality products for subsequent processing and are a limitation to the productivity of the next workers in the stream.
Implementing standardized work procedures can help address these common challenges by promoting continuous improvement and adaptability.
Final Thoughts
Standardized work is the foundation for any successful production system. The result of the implementation of Standardized Work can be considered the execution of operations safely, efficiently, on time and with minimal cost. A standardized work process is crucial for achieving long-term benefits in production quality and employee satisfaction, as it requires ongoing observation and input from employees to continuously improve efficiency.
We can help you implement standardized work in your organization with our application ProcessNavigation!
Contact Us
Simplify the way people work and learn at the frontline
See the industry-leading how-to platform in a 30-minute live demo.
Learn more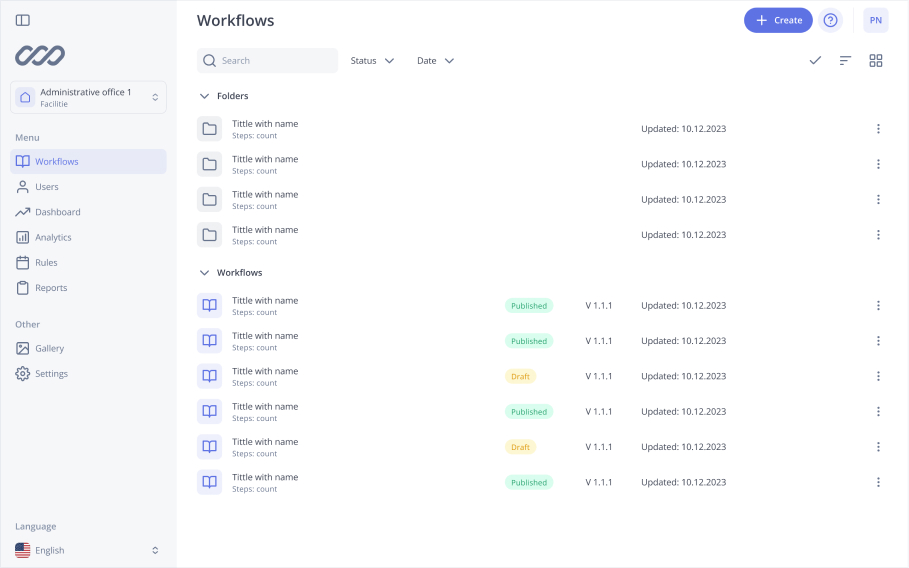
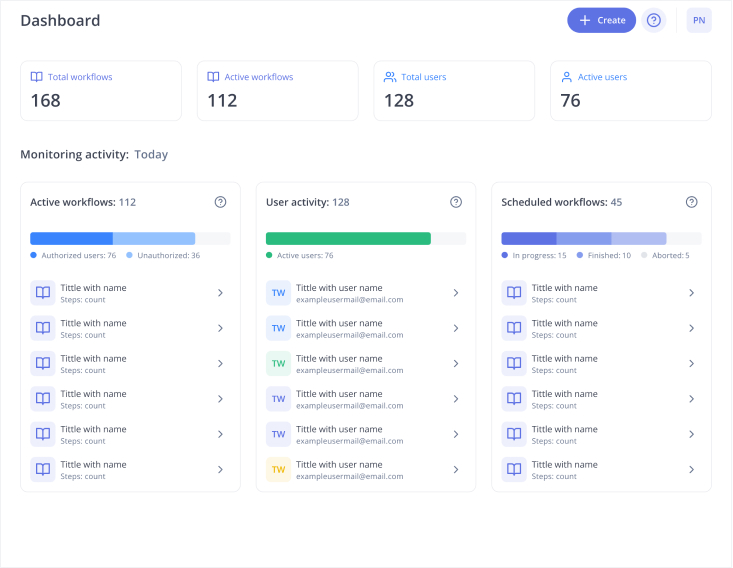