Centerlining
Introduction
In the world of manufacturing and process optimization centerlining is key to consistency, efficiency and quality. Centerlining is critical to maintaining product quality by standardising and measuring variable impacts. Despite its importance many professionals don’t fully understand it or how to implement it. This guide will cover centerlining, its applications, benefits and best practices.
What is Centerlining?
Centerlining (also known as “centre lining” in some countries) is the practice of setting and maintaining optimal process conditions to minimise variability. A centerlined process is key to productivity, reducing defects and cost of production. By finding the best operating conditions manufacturers can improve product quality, reduce waste and increase operational efficiency. The goal is to create a consistent repeatable process that delivers predictable outcomes.
Why is Centerlining Important for Consistent Product Quality?
Variability in manufacturing can lead to inefficiencies, extra costs and product defects. Centerlining eliminates these issues by keeping production within defined boundaries. When a process deviates from its optimal settings centerlining allows quick detection and correction before issues become big. And evaluating product quality against centerline settings is critical. Solid reporting mechanisms to measure quality against these settings, and training for operators, are essential to maintain quality standards and avoid costly mistakes.
Key benefits of centerlining are:
- Better Product Quality: Maintaining conditions results in uniform product quality, less defects and rework.
- Increased Efficiency: By minimizing deviations manufacturers can reduce downtime and material waste. Centerlining improves machine efficiency by standardizing process settings which means consistent shop floor operations.
- Compliance: Many industries have strict regulations. Centerlining ensures compliance by maintaining process consistency.
- Equipment Performance: Optimized settings prevents wear and tear on equipment, extends its life.
Key Elements of Centerlining Process Variables
To centerline you need to focus on the following:
- Critical Parameters: Identify the key process variables that impact product quality and operational efficiency. These are the variables that impact product quality and may be temperature, pressure, speed and material composition.
- Data Collection and Analysis: Collect historical and real time data to understand process trends. This will tell you the optimal setting for each parameter.
- Standardization: Create standard operating procedures (SOPs) based on best practice. Documenting these ensures consistency across different shifts and operators. Centreline process settings give you the flexibility to adapt to external factors.
- Monitoring and Control: Use sensors, automation and software to monitor process parameters. Clearly defined variable limits are critical to monitor and measure centreline processes. Implementing alerts and corrective actions will prevent deviations.
- Continuous Improvement: Centrelining is not a one off process. You need to review and adjust based on new data and technology advancements to maintain efficiency over time.
Centerlining in the Manufacturing Process
Manufacturers in various industries centerline to optimize their operations. Establishing consistent and optimal settings in the manufacturing process is key to quality and efficiency. Here are some common applications:
- Food and Beverage: Consistent ingredient ratios, cooking temperatures and packaging conditions.
- Pharmaceutical Manufacturing: Precise formulations and environmental conditions to meet regulatory requirements.
- Automotive Production: Standardizing assembly line processes to improve product uniformity and reduce defects. Understanding how different variables affect the process and the final product is key to identify areas for improvement and optimize efficiency.
- Chemical Processing: Controlling reaction temperatures and compositions to increase yield and safety.
Centerlining Challenges
Despite the benefits, there are challenges. Some of the common ones are:
- Resistance to Change: Employees accustomed to old ways will resist the new process.
- Data Overload: Managing and analyzing lots of data can be overwhelming without the right tools. The challenges of manual data recording can be mitigated by using software to visualize and analyze a newly centerlined process.
- Initial Costs: Automation and monitoring systems require an upfront investment.
- Lack of Expertise: Proper training is necessary to implement centerlining correctly and avoid bad product.
Overcoming these challenges involves training your employees, using user friendly technology and a culture of continuous improvement.
Getting Started with Centerlining
If you want to centerline in your organization, follow these steps:
- Assess Current Process: Identify areas of high variability and inefficiency.
- Define Objectives: Determine what you want to achieve with centerlining, e.g. improve quality, reduce waste or increase productivity. Emphasize the importance of centerlining in achieving those objectives by ensuring consistent production quality and efficiency.
- Collect Data: Gather historical and real time process data to understand performance trends.
- Establish Baseline Parameters: Define optimal process settings for critical variables based on data to ensure consistency and better product quality.
- Implement Monitoring Systems: Use sensors and automation tools to track and control parameters.
- Train Employees: Educate your staff on centerlining principles and best practices.
- Review and Adjust: Continuously analyze data to optimize processes.
Conclusion
Centerlining is a game-changer for manufacturing and business operations. By keeping process parameters consistent, companies can boost quality, efficiency, and cost savings. While challenges exist, the benefits far outweigh the difficulties, making it a smart investment.
With the right approach and modern technology, businesses can implement centerlining effectively, leading to long-term growth. Whether you’re in food production, pharmaceuticals, automotive manufacturing, or another industry, centerlining helps streamline operations and achieve excellence. It minimizes variability, reduces waste, and ensures products meet high standards. Embracing centerlining isn’t just about efficiency — it’s about staying competitive and continuously improving.
Simplify the way people work and learn at the frontline
See the industry-leading how-to platform in a 30-minute live demo.
Learn more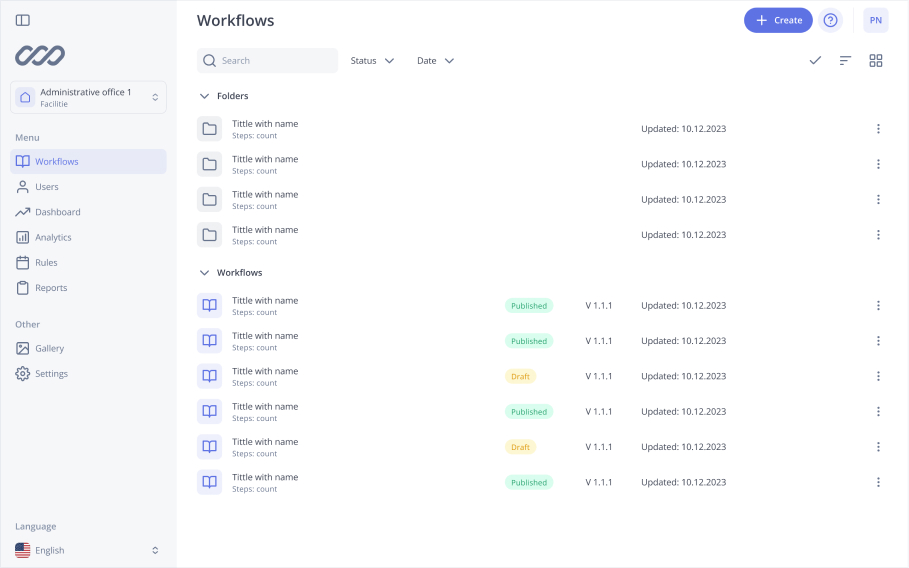
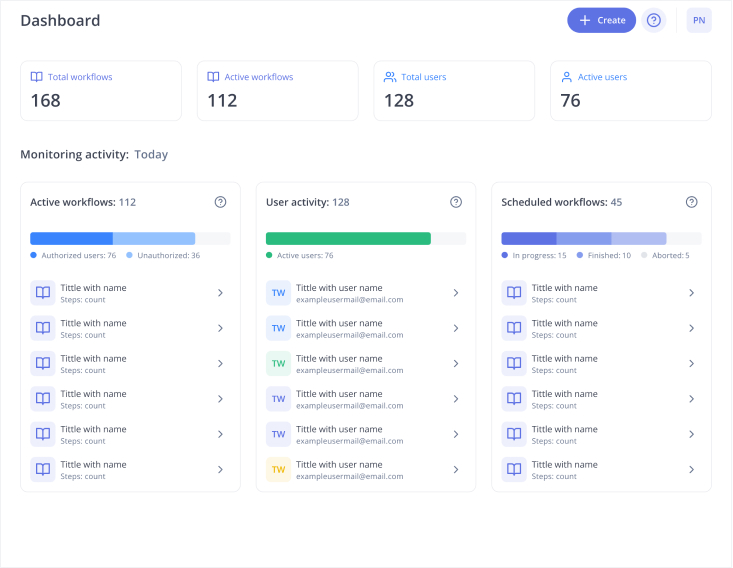