Root Cause Analysis (RCA)
In every field of work, from software development to healthcare, from manufacturing to customer service, problem solving is a must. One of the most important tools to solve problems systematically is Root Cause Analysis (RCA). Effective RCA is built on core principles that improve analysis and gets buy in from stakeholders. Root Cause Analysis is a method to find the root cause of a problem not just the symptoms. By finding the root cause organizations can get long-term solutions, optimize processes and improve performance. This approach is used in many industries to investigate problems, improve quality and prevent recurrence of issues.
What is Root Cause Analysis?
Root Cause Analysis is a systematic process to find the underlying cause of a problem. It’s about digging deeper to find out why something went wrong instead of just fixing the surface level symptoms. The goal is not just to fix the current issue but to prevent the same problem from happening again in the future. RCA provides a framework to analyze situations and is critical to ensure solutions are sustainable and effective. The process typically involves gathering data, identifying causes and evaluating factors.
Why Identify Root Causes
Identifying the root cause is critical because solving the symptoms without addressing the underlying cause will lead to repeated failures. For example in manufacturing if a machine keeps failing, fixing the machine temporarily may not solve the long term issue. The root cause could be a faulty part, poor maintenance practices or a design flaw. Only when these root causes are identified and fixed can the issue be solved permanently.
Moreover focusing on root causes and underlying issues instead of symptoms saves time and resources. By not addressing the cause of the problem companies can waste money on ineffective solutions and experience recurring issues that affect productivity, quality and customer satisfaction.
Methods of Root Cause Analysis
Root Cause Analysis isn’t a one-size-fits-all solution; there are several ways to determine the true cause of an issue. The method chosen often depends on the problem, the industry and the resources available. Doing RCA not only when things fail but also when things go right can be super valuable. Here are some of the most popular RCA methods:
1. The 5 Whys
The “5 Whys” is one of the simplest and most effective root cause analysis techniques. It’s asking “why” 5 times (or as many times as needed) to drill down into the problem and find the underlying cause. For example if a machine breaks down you might ask:
- Why did the machine break down? (The motor stopped working.)
- Why did the motor stop working? (The motor overheated.)
- Why did the motor overheat? (There was insufficient lubrication.)
- Why was there insufficient lubrication? (The lubricant reservoir was empty.)
- Why was the lubricant reservoir empty? (It wasn’t refilled during the maintenance schedule.)
This iterative process helps you find the root cause by eliminating surface level answers and encourages teams to dig deeper into each new piece of evidence, focusing on the real underlying issue.
2. Fishbone Diagram (Ishikawa)
The Fishbone diagram, also known as the Ishikawa diagram or cause-and-effect diagram, is another great tool for RCA. It visually maps out all the possible causes of a problem, categorizing them into people, processes, machines, materials, environment and measurements, like the anatomy of a fish skeleton. This method allows teams to look at all the possible contributing factors in a structured way. It’s particularly useful in complex situations with multiple contributing causes. By looking at all the possible causes the team can focus on the ones that have the biggest impact.
3. Failure Mode and Effect Analysis (FMEA)
FMEA is a proactive method that identifies potential failure modes in a system or process before they occur. It evaluates the severity, frequency, and detectability of failures to prioritize which issues should be addressed first, including system failures that could impact product quality and customer satisfaction. This technique is widely used in industries like aerospace and automotive, where safety is critical. FMEA helps identify potential root causes early in the design phase, allowing corrective actions to be implemented before failures occur.
4. Pareto Analysis
The Pareto principle, often referred to as the 80/20 rule, is used in RCA to focus on the most critical causes that are responsible for the majority of problems. According to this principle, 80% of the problems come from 20% of the causes, highlighting the cumulative impact of these few critical factors. Pareto analysis helps prioritize which root causes to address first by focusing on the few causes that lead to the majority of the issues.
5. Barrier Analysis
Barrier analysis focuses on identifying the barriers that failed to prevent the problem from occurring. In this approach, the goal is to evaluate the effectiveness of safety measures or other preventative actions. By understanding what barriers failed and why, organizations can strengthen their systems with a focus on preventing recurrence of issues.
Contributing Factors in Root Cause Analysis
While finding the root cause is important, it’s equally important to understand the contributing factors that led to the problem. These are the elements that, combined with the root cause, create a perfect storm for failure. They are usually the conditions or circumstances that make it easier for a problem to happen.
Contributing factors could be lack of training, poor communication, no resources or systemic inefficiencies. A thorough RCA looks at both the root cause and these contributing factors so you understand everything and improvements address all parts of the problem.
RCA Tools and Resources
There are many tools and resources to help you with root cause analysis. These tools help streamline the process, make it more efficient and make sure you don’t miss anything. Some of the most common tools are:
And there are many root cause analysis resources such as articles, case studies and publications to help you with RCA.
1. Data Analysis Software
Modern data analysis tools help organizations collect, analyze and interpret large amounts of data. These tools can be used to find patterns, trends and anomalies that point to root causes. Whether it’s through statistical analysis, predictive modelling or machine learning these tools can dig deeper into the data to find hidden causes of problems. And there are many analysis resources, articles, case studies and publications to help you apply these tools for comprehensive data analysis.
2. Root Cause Analysis Templates
Templates give you a structured way to do an RCA. They guide the team through the process from problem to solution. Templates ensure everything is followed and nothing is missed. They can be used for simple and complex problems, so are a versatile tool for any industry. By guiding the team through each step templates ensure the right solutions are identified and implemented.
3. RCA Training
Root Cause Analysis is a skill that needs training and practice. There are many resources available to help individuals and teams learn RCA methods and techniques. Training ensures employees have the skills to identify root causes, analyze data and implement solutions.
4. Expert Consultants
For complex problems organizations may bring in expert consultants who specialize in Root Cause Analysis. These experts can bring an objective view, apply advanced techniques and facilitate the analysis. Their experience and knowledge can be invaluable in tackling tough problems and ensuring solutions are effective and sustainable.
Challenges in Root Cause Analysis
Despite its importance Root Cause Analysis is not always easy. Here are some challenges you may face:
1. No Data
Data is key to RCA. Without data you can’t trace the problem to the root cause. Inadequate or incomplete data will lead to wrong conclusions and wrong solutions. Understanding the historical context is important as it allows you to go deeper by considering all the factors that contributed over time.
2. Biases and Assumptions
The team doing RCA may be influenced by biases or assumptions that cloud their judgment. You must approach the analysis with an open mind and not jump to conclusions based on preconceived notions. Finding the real root cause is key to accurate analysis and to prevent recurrence.
3. Complex Problems
Many problems are multi faceted and have multiple root causes. RCA can be difficult when problems have many contributing factors and it’s hard to determine which are the most critical. Using different root cause analysis methods can help you identify and address these underlying issues.
4. Resistance to Change
Once you have found the root cause the next step is to implement the corrective actions. But resistance to change can be a big barrier to success. Employees or management may be reluctant to adopt new processes which can delay or prevent the problem from being solved. Do a thorough change analysis to examine the timeline and relevance of the changes to understand and overcome this resistance.
To overcome these challenges you must do root cause analysis thoroughly and systematically.
Implementing Effective Solutions
Once you’ve identified the root cause, you need to implement solutions that fix the problem. The solution should be tailored to the root cause and any other contributing factors, so the problem is fully fixed. You also need to monitor the solution and adjust as needed. And testing solutions is key to verifying how they fix the underlying issues.
Corrective actions may include changes to processes, training, new policies or new technology. For example, if the root cause analysis shows frequent machine breakdowns are caused by poor maintenance practices, the solution could be to change the maintenance schedule, train employees on proper maintenance or upgrade the machines to more reliable models.
Conclusion
Root Cause Analysis is a must-have tool for any organization that wants to improve continuously. By fixing the root cause of a problem you can eliminate recurring issues, improve processes and customer satisfaction. The methods and tools for RCA provide a structured approach to problem solving that can be applied across many industries. But successful implementation requires data analysis, a systematic approach and a commitment to ongoing improvement. When used correctly Root Cause Analysis fixes problems and drives long term success and growth. And by addressing future issues through preventative measures, you’ll avoid similar problems and continuous improvement.
Simplify the way people work and learn at the frontline
See the industry-leading how-to platform in a 30-minute live demo.
Learn more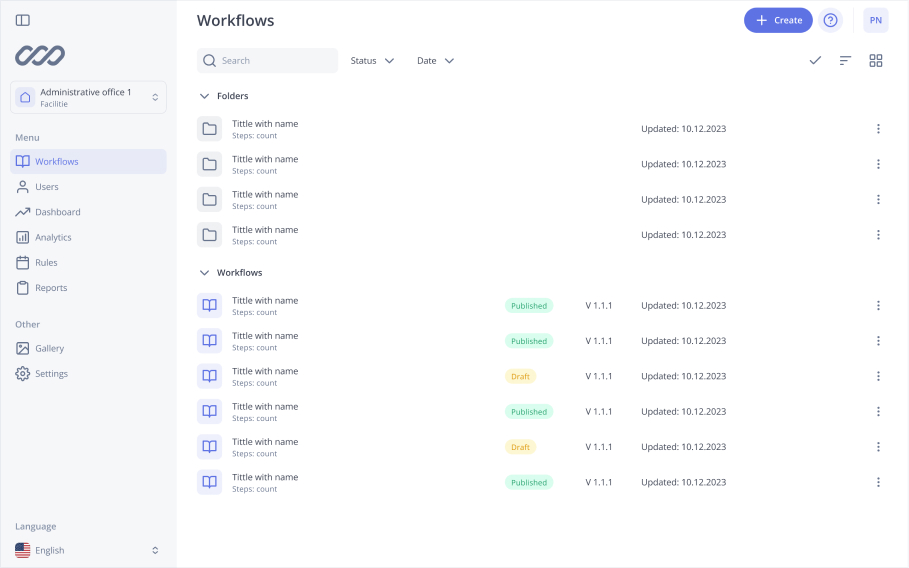
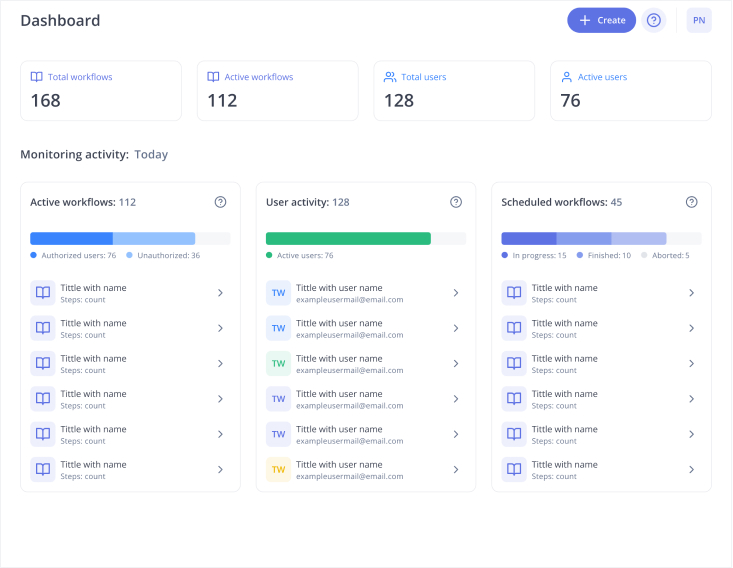