Machine Availability
Machine availability is a big deal in manufacturing and industry, it’s a direct factor in productivity, efficiency and profitability. Knowing how to measure, analyze and improve machine availability helps to minimize downtime and maximize output. This guide covers the basics of machine availability, definition, calculation, affecting factors and how to improve it. By using equipment data to refine maintenance strategies and reduce downtime manufacturers can gain valuable insight into machine behaviour. They can then take a proactive approach to maintenance and find opportunities to increase efficiency.
What is Machine Availability?
Machine availability is the amount of time a machine is running and ready to run compared to the total scheduled running time. Machine availability measures the uptime of a machine vs the total scheduled time. It’s a key part of Overall Equipment Effectiveness (OEE) which measures equipment performance. High machine availability means well maintained and reliable equipment with minimal downtime, low availability means frequent breakdowns and inefficiencies.
Machine availability is a big part of production planning as it affects the whole operation. Having machines up and running not only increases production output but also safety in the workplace and reduces operational costs. Companies that focus on machine availability have lower failure rates, better product quality and a smoother production process.
Machine Availability Calculation
Machine availability is typically calculated using the following formula:
Availability = Equipment Uptime ÷ Total Scheduled Time
Where:
- Actual Operating Time (Equipment Run Time): The actual time the machine is running and producing.
- Scheduled Operating Time (Planned Production Time): The total time the machine is supposed to be running, excluding planned downtime.
For example, if a machine is scheduled to run for 10 hours a day but only runs for 8 hours due to breakdowns, its availability is: 8 ÷ 10 × 100% = 80%.
This formula is simple yet effective to measure machine availability and identify areas for improvement. Tracking availability over time will help you to identify patterns and trends that needs attention.
Factors Affecting Machine Availability
Several things can impact machine availability:
- Scheduled Maintenance. Maintenance is needed to make machines work at their best. But excessive maintenance because of unnecessary and inefficient practices can cause downtime. Maintenance should be planned carefully to balance maintenance need with production need.
- Unplanned Downtime. Breakdowns, malfunctions and unexpected failures reduce machine availability and requires equipment repair that affects production. Identify the root cause and implement preventive measures to mitigate these. Unplanned downtime can be very costly especially in industries where equipment failure directly affects revenue streams.
- Changeovers and Setup Time. Frequent production changeovers and long setup times reduces the effective running time of the machine. Reduce changeover time through proper planning and the machine availability will increase.
- Supply Chain Disruption. Lack of raw materials, spare parts or tools can cause machine idle time and affects availability. A well managed supply chain ensures that essential resources are always available when needed.
- Operator Efficiency. Human factors such as operator error, training deficiency and manpower shortage also affects machine availability. Provide adequate training and clear operational guidelines to minimize errors and increase machine uptime.
- Environmental Factors. Extreme temperatures, humidity, dust and other environmental condition can affects machine performance and life. Proper climate control and protective measures can mitigate these risks.
- Aging Equipment. Older machine are more prone to breakdown and inefficiencies. Regular upgrade, refurbish or replace can help maintain high machine availability.
How to Improve Machine Availability
Keeping machines running efficiently is essential for any business that relies on production. Downtime can be costly, so improving machine availability should be a priority. Here’s a step-by-step guide to help you reduce downtime and keep your equipment in top shape:
- Use Predictive Maintenance. Instead of waiting for a machine to fail, predictive maintenance helps you catch issues before they become serious. By using IoT sensors and data analytics, you can monitor machine performance in real time and address problems early. This reduces unplanned downtime and keeps operations running smoothly.
- Optimize Preventive Maintenance. Routine maintenance is important, but if it’s not scheduled properly, it can either be excessive or insufficient. Finding the right balance ensures that machines get the care they need without unnecessary downtime. Review your maintenance schedules and adjust them based on real usage data rather than fixed intervals.
- Reduce Setup and Changeover Times. Long setup and changeover times slow down production. Implementing lean manufacturing techniques, such as Single-Minute Exchange of Die (SMED), can make transitions faster and smoother. The less time spent switching between tasks, the more efficient your machines will be.
- Train Your Operators. A well-trained operator can prevent many problems before they happen. Teaching workers how to properly use and troubleshoot machines reduces the risk of errors and improves response time in case of an issue. When operators know how to handle minor problems, they can prevent unnecessary downtime.
- Implement Smart Monitoring and Automation. Automated monitoring systems provide real-time data on machine performance. This allows businesses to spot inefficiencies, detect early warning signs, and take action before a problem escalates. Smart technology reduces human error and ensures machines are running at optimal performance.
- Keep Essential Spare Parts on Hand. Nothing is worse than having a machine break down and realizing you don’t have the right parts to fix it. Keeping a well-managed inventory of critical spare parts can save time and prevent long delays in production.
- Conduct Regular Machine Audits. Performing regular audits helps you identify recurring issues and areas for improvement. By analyzing machine performance and maintenance records, you can make better decisions about repairs, upgrades, and process improvements.
- Invest in Quality Equipment. Cheaper machines might save money upfront, but they often lead to more breakdowns and higher long-term costs. Investing in reliable, high-quality machines with good warranties and support services reduces downtime and improves overall productivity.
Machine Availability vs Equipment Availability
Machine availability refers to the uptime of an individual machine, while equipment availability considers the entire production line, including supporting systems. Understanding this difference helps businesses develop better strategies for improving efficiency and reducing bottlenecks.
By using a combination of predictive maintenance, operator training, and smart technology, businesses can increase machine availability, reduce downtime, and improve overall productivity.
Conclusion
By understanding machine availability, calculating it and implementing strategies to improve it, companies can increase productivity and reduce operational costs. Predictive maintenance, machine scheduling and training operators is the way to higher availability and seamless production.
Simplify the way people work and learn at the frontline
See the industry-leading how-to platform in a 30-minute live demo.
Learn more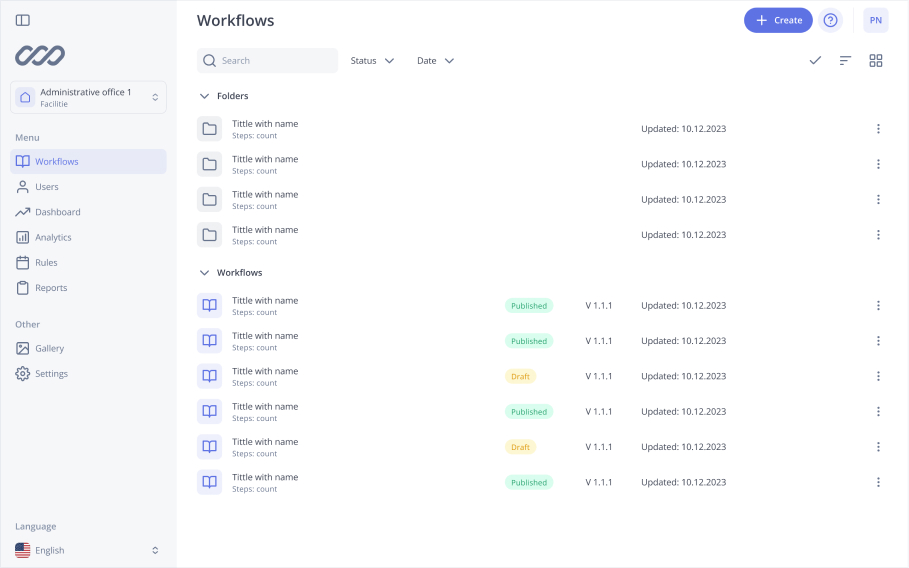
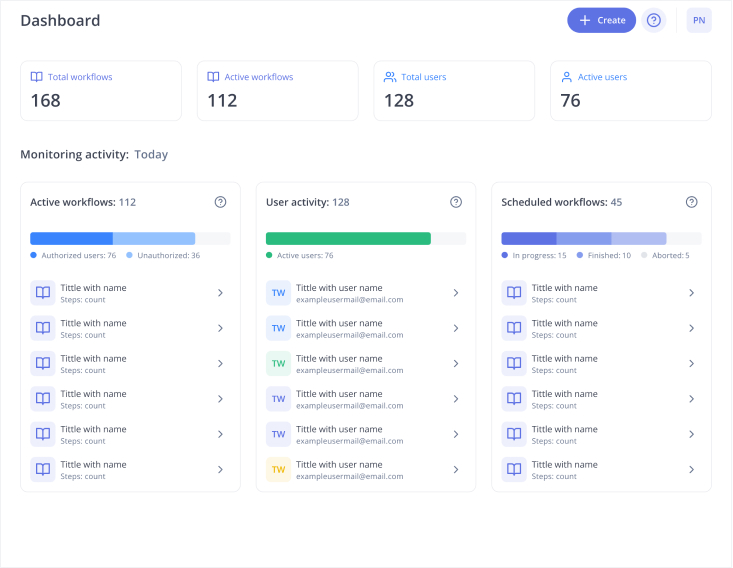