Implementing Digital Instructions: Enhancing Industrial Facility Maintenance
3 weeks
Time to implement
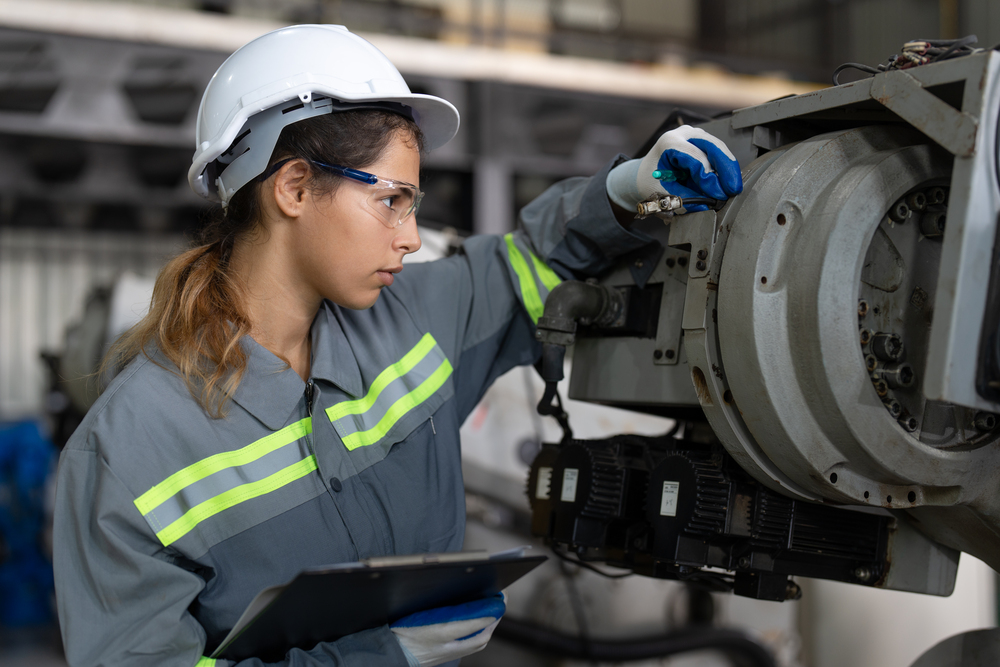
Our client, a leading industrial manufacturing company specializing in precision engineering, faced significant challenges in maintaining high standards of cleanliness and equipment maintenance across its production facilities. Despite their best efforts, inconsistencies in cleaning and maintenance procedures led to operational inefficiencies, equipment failures, and difficulties in training new maintenance staff.
Problem
The company identified several key issues that affected their maintenance and cleaning operations:
- Lack of Standardized Procedures: Maintenance staff followed varying methods, resulting in inconsistent equipment upkeep and potential safety hazards.
- Quality Control Challenges: Supervisors struggled to ensure that all maintenance tasks were completed to the required standard due to a lack of structured oversight.
- Training Difficulties: New employees faced steep learning curves, and without clear, standardized instructions, their performance varied significantly.
- Misinterpretation of Maintenance Requirements: Ambiguous or incomplete guidelines led to errors, such as improper use of cleaning agents or missed crucial maintenance steps.
- Inefficient Communication Between Teams: Staff often lacked real-time updates on completed tasks, leading to redundancies and increased downtime.
Objectives
To address these challenges, ProcessNavigation was entrusted with the following goals:
- To implement a structured and systematic approach to facility cleaning and maintenance.
- To enhance quality control measures to ensure compliance with industry safety and performance standards.
- To streamline the training process for new employees with clear, step-by-step digital instructions.
Solution
To resolve these issues, ProcessNavigation developed and implemented a comprehensive digital instruction and checklist system tailored to the client’s industrial environment. Our solution included the following key components:
- Development of Custom Digital Checklists: We designed detailed checklists for each maintenance and cleaning task, specifying exact steps, required tools, and safety precautions.
- Interactive Mobile Application: We deployed an easy-to-use mobile app that allowed maintenance personnel to access digital instructions, track task completion, and report issues in real time.
- Automated Quality Control System: Supervisors gained access to a dashboard with real-time updates, enabling them to monitor progress, verify completed tasks, and ensure compliance with quality standards.
- Comprehensive Training Modules: We created digital training materials, including video tutorials and interactive guides, to facilitate onboarding and skill development for new employees.
- Integrated Communication Platform: Our solution incorporated a messaging system that enabled team members to coordinate tasks, report malfunctions, and request assistance instantly.
Results
Following the implementation of ProcessNavigation’s digital solution, the industrial company experienced significant improvements:
- Increased Operational Efficiency: Maintenance times were optimized, reducing equipment downtime and enhancing production output.
- Improved Safety Compliance: Consistently followed maintenance protocols ensured a safer work environment.
- Enhanced Staff Performance: Maintenance personnel adapted more quickly and adhered to best practices with greater accuracy.
- Stronger Quality Assurance: Supervisors could easily track performance metrics and ensure compliance with industry regulations.
Conclusion
By integrating digital instructions and checklists, our client successfully transformed its facility maintenance operations. This modernized approach eliminated inefficiencies, improved team coordination, and ensured regulatory compliance. As a result, the company strengthened its reputation for reliability, safety, and operational excellence.
Simplify the way people work and learn at the frontline
See the industry-leading how-to platform in a 30-minute live demo.
Send request-
+25%
improvement in maintenance task completion rates
-
-30%
reduction in equipment-related safety incidents
-
-45%
decrease in maintenance errors and missed procedures