Enhancing Equipment Maintenance: A Digital Transformation
1 month
Time to implement
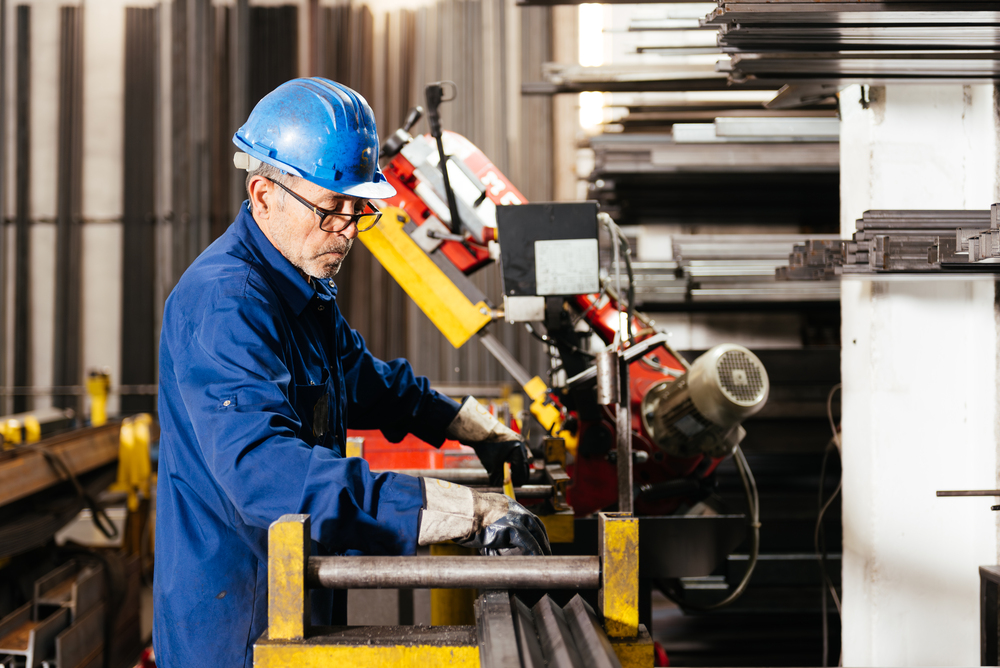
Our client, a major industrial enterprise, faced significant challenges in maintaining operational efficiency due to inconsistencies in equipment maintenance procedures. Without standardized instructions, employees struggled with inefficiencies, errors, and safety risks.
Problem
Traditional maintenance processes presented several issues:
- Inconsistency and Lack of Structure: Employees performed maintenance tasks in varying ways, increasing the likelihood of errors and missed steps.
- Slow Execution and Inefficiency: Without standardized procedures, workers relied on memory, leading to delays and decreased productivity.
- Increased Risk of Injuries and Equipment Damage: Incorrect execution of maintenance steps posed safety hazards and led to equipment failures.
- Lack of Process Analysis and Improvement: The absence of data collection made it difficult to identify recurring problems and enhance maintenance procedures.
Objectives
ProcessNavigation was entrusted with the following goals:
- To Standardize Maintenance Procedures: Implement structured digital instructions to ensure consistency.
- To Enhance Safety Measures: Minimize risks associated with incorrect maintenance practices.
- To Enable Data-Driven Process Improvements: Facilitate continuous optimization through data collection and analysis.
Solution
To overcome these challenges, ProcessNavigation introduced a comprehensive digital solution:
- Structured Digital Checklists: Step-by-step maintenance guides ensured clarity and adherence to best practices, reducing human error.
- Instant Access via QR Codes: Each piece of equipment featured a QR code, allowing technicians to access digital checklists instantly on mobile devices.
- Automated Data Collection and Analysis: Maintenance activities were logged automatically, providing valuable insights for process improvements.
Results
Following the implementation of digital maintenance instructions, the client achieved remarkable outcomes:
- Improvement Efficiency: Employees completed maintenance tasks faster and more effectively.
- Reduced Risk and Errors: Clear, structured instructions minimized safety hazards and equipment damage.
- Enhanced Process Optimization: Data-driven insights allowed for continuous refinements in maintenance procedures.
Conclusion
By adopting digital instructions and checklists from ProcessNavigation, our client revolutionized their equipment maintenance operations. This transformation led to greater efficiency, improved safety, and a structured approach to process improvement. As a result, the company significantly enhanced operational reliability and positioned itself as a leader in modernized industrial maintenance.
Simplify the way people work and learn at the frontline
See the industry-leading how-to platform in a 30-minute live demo.
Send request-
+35%
operational efficiency has increased
-
-62%
equipment failure incidents have decreased
-
-47%
maintenance-related downtime has reduced