Operational Excellence
What Is Operational Excellence?
Operational excellence in manufacturing is a management philosophy that prioritises continuous improvement in all areas of business. It’s about creating systems and processes that are efficient, consistent and high quality so you can serve your clients better and stay ahead of the competition. At the heart of this philosophy are the core principles of operational excellence that guide you towards better performance.
Operational excellence is driven by:
- Delivering customer experience by providing reliable and high-quality products or services.
- Simplifying processes to reduce waste and cost.
- Creating a company culture of adaptability and resilience to market changes.
Operational excellence is not a one-time initiative, but a long journey. It requires long-term commitment, strategic thinking, and changes at all levels of the organization.
Continuous Improvement in Operational Excellence
Achieving operational excellence is the foundation. and increase production efficiency. It’s about regularly reviewing and improving processes to eliminate inefficiencies, improve quality and increase production productivity. Organizations can use various operational excellence methodologies such as Lean Manufacturing, Six Sigma and Kaizen to achieve this.
Here’s how continuous improvement works in practice:
- Identify Opportunities: Look for areas where performance is lagging or processes are outdated.
- Prioritize Changes: Focus on changes that will have the greatest impact on efficiency or customer satisfaction.
- Analyze Data: Use metrics and analytics to understand key problems and potential solutions.
- Validate Results: Implement changes on a small scale, test, refine and then scale up.
Creating a Culture of Excellence
Operational excellence is not just about tools or processes, but also about people. To really succeed organizations need to create a culture that values excellence, collaboration and innovation. Adopting an operational excellence mindset is key to identifying productivity and profit in non-traditional areas.
Key Steps to Building a Culture of Excellence:
- Focus on the Customer: A customer-centric approach means that the organisation stays focused on delivering value and gaining a competitive advantage.
- Empower Employees: Give team members the training, tools and autonomy to make decisions that drive improvement.
- Set Clear Goals: Employees need to know how their work contributes to the bigger picture.
- Encourage Feedback: Create an environment where employees feel comfortable sharing their ideas and concerns.
- Use Technology: Use analytics tools to find hidden inefficiencies or predict future problems.
Proven Operational Excellence Methodologies
Here are three of the most widely accepted approaches:
1. Lean Manufacturing
Lean manufacturing is a methodology aimed at minimizing waste and maximizing the quality and value of the final product. By optimizing work processes and eliminating non-essential steps, lean manufacturing reduces costs and increases efficiency.
2. Six Sigma
Six Sigma is a data-driven methodology aimed at improving process quality by identifying and eliminating defects. It uses statistical tools and techniques to achieve perfect results.
3. Kaizen (Continuous Improvement)
Kaizen, which means “change for the better” in Japanese, is a philosophy of continuous, incremental improvement. Kaizen focuses on small, step-by-step changes that lead to long-term growth.
Roadmap for Operational Excellence
Achieving operational excellence needs a clear roadmap. Here is a step-by-step guide to get you started:
- Define the Vision: Get leadership aligned to the principles of operational excellence and communicate the vision to the whole organization.
- Assess Current State: Do a full audit to see how your manufacturing operations are performing. Focus on the production processes to identify opportunities to improve operational efficiency and quality design.
- Set Priorities: Identify areas where improvements will have the most significant impact.
- Engage Employees: Encourage collaboration and feedback across the organization.
- Implement Changes: Start small and gradually scale up successful initiatives.
- Review and Refine: Monitor performance indicators and refine your approach based on results.
Challenges
Common challenges include:
- Resistance to Change: Employees may be hesitant to implement new processes or tools. Clear communication and training is key to overcoming this.
- Disjointed Operations: Closed departments prevent collaboration and efficiency gains. Cross-functional teams and integrated systems bridge these gaps in the production process.
- Inconsistent Metrics: Without reliable data you cannot measure progress. Invest in data collection and analysis tools to ensure data accuracy.
Conclusion
Operational excellence is a long journey that requires dedication, collaboration and flexibility. By applying the principles of continuous improvement, using proven methodologies and leveraging technology, organizations can achieve long-term success.
In an ever-changing world, operational excellence provides the stability and flexibility needed to succeed. With the right mindset and tools, your organization can reach its full potential and deliver exceptional customer value for years to come.
Simplify the way people work and learn at the frontline
See the industry-leading how-to platform in a 30-minute live demo.
Learn more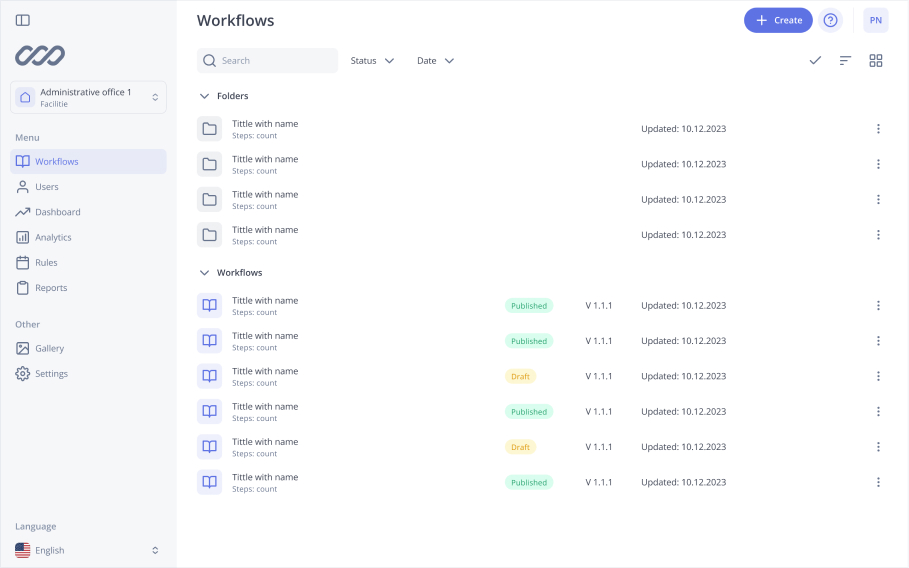
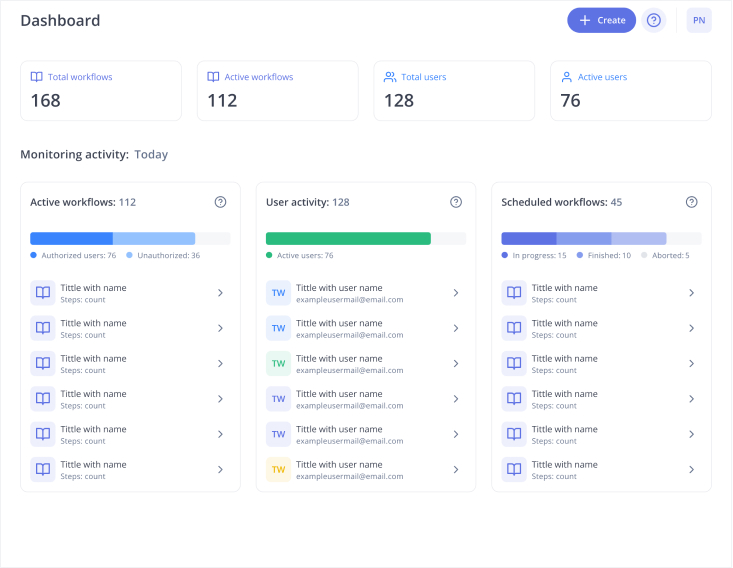