Shop Floor Management
Shop Floor Management (SFM) is the foundation of operational excellence in manufacturing as it makes processes more efficient and adapts to technology. This is where leadership, process improvement and continuous improvement meet on the shop floor. According to lean principles SFM means management involvement in the oversight and improvement of value adding processes. This guide will help you understand shop floor management better and give you practical advice on how to do it.
What is Shop Floor Management?
Shop floor management is the process of monitoring, controlling and improving manufacturing processes on the shop floor. It’s about managing resources, monitoring resource availability, tracking labour costs, achieving production targets, and using real time data to improve operational procedures and inventory and labour management. Effective shop floor management will save you time by improving collaboration and leadership, resulting in faster response and better workplace safety. By bringing management and employees together SFM will improve productivity, quality and efficiency in the manufacturing facility.
SFM Core Components
The SFM components are:
- Shop Floor Leadership: Managers are on the shop floor, communicating and deciding in real time, showing best practice.
- Visual Management: KPI’s, production metrics and goals are displayed visually using visual tools like whiteboards and dashboards, to create the production schedule.
- Standardized Communication: Structured meetings, defined escalation paths and transparent reporting protocols so information flows across the whole organisation, to inform better decision making.
- Continuous Improvement: SFM uses lean tools like Kaizen, PDCA cycles and root cause analysis to find and solve inefficiencies in a consistent way.
- Employee Empowerment: Employees are encouraged to solve problems, which means they take ownership.
Shop Floor Management Goals
- Increase Productivity: Productivity is increasing by eliminating inefficiencies and unnecessary movement. Efficiency and productivity is improved by defining standard operating procedures and better communication.
- Improve Product Quality: SFM is the process of ensuring quality standards are met by implementing quality control, regular inspections, maintenance and immediate response to any deviations from the standards.
- Reduce Waste: The processes in the production process are improved through daily meetings to reduce waste, material, time or labour. These meetings help to coordinate various operations, to improve collaboration and to use technology to streamline workflows to improve overall efficiency in manufacturing environments.
- Be Transparent: Real time monitoring and open communication will help to identify and fix issues early, which will improve efficiency.
- Engage employees: By actively involving employees and recognizing their efforts to identify inefficiencies, SFM will give them a sense of ownership and job satisfaction.
How to Implement Shop Floor Management
Step 1: Leadership on the Shop Floor
To implement SFM effectively, leadership needs to focus on efficient production. This means direct interaction with employees on the production floor and the ability to solve problems in real time. And prioritise overall equipment effectiveness to improve productivity and performance.
Best Practices:
- Do Gemba walk-throughs regularly.
- Engage employees to understand problems and get ideas for improvement.
- On-site coaching for teams.
Step 2: Visual Management Tools
Visual tools are the key to SFM, forming part of the five pillars that give real-time visibility into performance and issues.
Tools to use:
- Shop Floor Boards: This tool displays KPI’s, targets, and faults in one place.
- Andon systems: Instantly show problems for quick fixes.
- Digital dashboards: Real-time updates and access to the whole facility.
- Visual management tools: Quickly communicate information, optimize layout and material flow, improve lean organization and collaboration.
Step 3: Standardized communication
Shop floor management refers to a consistent and structured communication strategy that will prevent miscommunication and ensure everyone is on the same page.
Implementation Tips:
- Daily shift meetings under 15 minutes.
- Meeting agendas to keep focus on specific actions.
Step 4: Continuous Improvement
Use proven methods to find and eliminate inefficiencies:
- Emphasize “value creation” by focusing on areas where processes and actions lead to productivity and efficiency.
- Utilize clear communication channels to enhance collaboration and transparency, which mitigates misunderstandings and improves overall productivity.
- Toyota Production System tips to drive continuous improvement.
- SFM uses tools like root cause analysis and PDCA cycles
Step 5: Employee Empowerment
Employees are the core of effective shop floor management, and utilizing specialized software can further enhance their capabilities. Understanding the manufacturing process and involving employees in decision making will give them commitment and innovation.
How to Empower Employees:
- Training on lean tools and methods.
- Recognize contributions to improvement.
- Create and maintain cross functional teams.
Common Issues
- Resistance to Change: Resistance to change will be found at different levels of the organisation, even among employees and managers. This can be overcome by strong leadership and communication, especially when automating repetitive tasks to allow workers to focus on more complex activities.
- Technical Barriers: Data collection and analysis is hindered by old systems. Invest in digital tools to simplify production processes and overall equipment effectiveness by optimising equipment performance.
- Sustainability: Without continuous effort the initial gains will disappear over time. Training and reinforcement of the principles is key, particularly in managing materials efficiently to enhance productivity and minimize waste.
Conclusion
Shop Floor Management focuses on improving productivity, quality, and transparency in manufacturing. A systematic approach is essential, incorporating leadership presence, visual management, employee empowerment, and continuous improvement.
With shop floor management boards and modern tools, SFM will give you a culture of sustained success and innovation.
Simplify the way people work and learn at the frontline
See the industry-leading how-to platform in a 30-minute live demo.
Learn more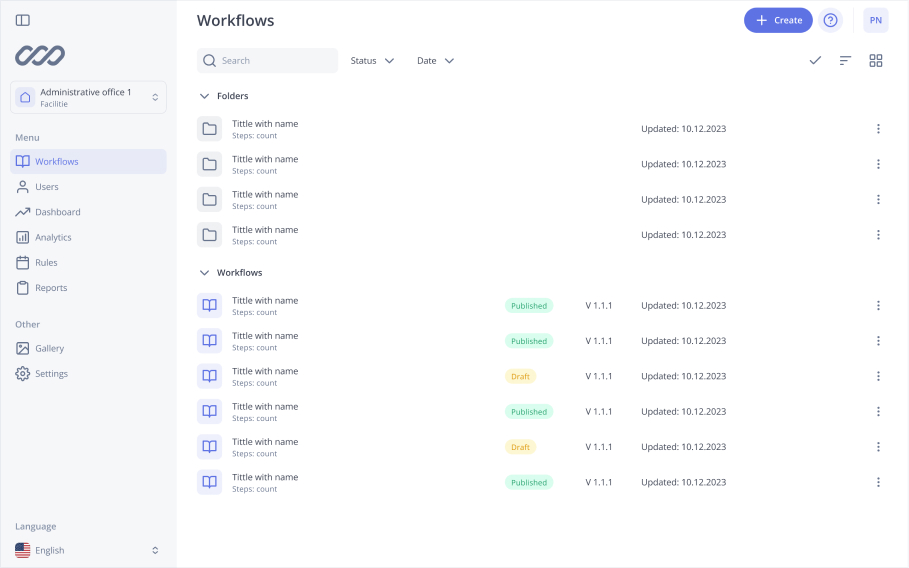
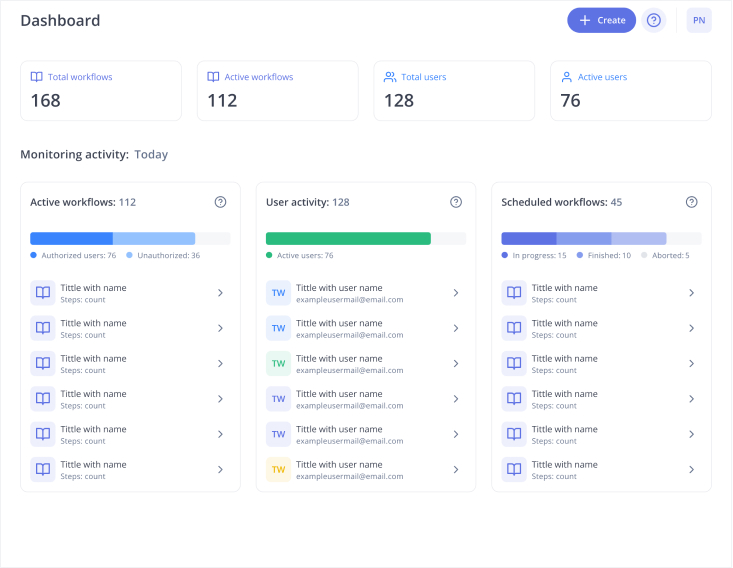