5S Methodology
In the world of lean and operational excellence the 5S methodology is a proven system to improve efficiency, safety and productivity. Originated at Toyota Motor Company as a part of Toyota Production System (TPS), the 5S methodology has gone global and is used in many industries around the world. The manufacturing industry has adopted the 5S methodology and has seen huge benefits by improving processes and competitiveness.
This guide goes into the philosophy, practical application and benefits of 5S. You will get the knowledge to improve performance and build a culture of continuous improvement.
5S Philosophy
The main purpose of 5S is simplification – simplify processes, remove waste and improve functionality. But the impact of this methodology goes beyond just tidying up:
- It gives employees ownership and accountability.
- It sets the foundation for lean manufacturing principles like just in time and continuous flow.
- It improves safety, reducing accidents and hazards.
- It makes a more pleasant and efficient work area, improving morale and productivity.
And 5S creates a organized work environment that improves efficiency and reduces waste. These add up to real results like lower costs, better quality and faster lead times.
1. Seiri (Sort)
The first step, Seiri, is to identify and remove unnecessary items from the workspace. A messy space impacts productivity and safety by creating hazards and inefficiencies, wasting time and potential worker injuries. By cleaning up, organisations can reduce distractions, improve space utilisation and streamline processes.
Actions:
- Conduct a full inventory of tools, materials and equipment.
- Separate necessary items from unnecessary.
- Dispose of or move items not used regularly.
- Label and categorize items to be kept for future reviews.
Outcome: A clean and tidy workspace that promotes efficiency and reduces confusion.
2. Seiton (Set in Order)
Once the unnecessary items are removed, the next step is to organise the remaining items for maximum visibility. Seiton means everything has its place and can be found easily.
Actions:
- Assign tools and materials to specific locations based on their use and sequence.
- Use visual aids like labels, colour codes and diagrams to show where things go.
- Set up shadow boards and tool racks to make it easier to identify and store tools.
- Use floor marking tape to define areas and keep things in order.
- Keep walkways and workstations clear.
Outcome: A simple layout that reduces time searching for items and improves productivity.
3. Seiso (Shine)
Cleaning the workspace is more than just a cosmetic exercise; it’s a part of Seiso in the 5S methodology. Regular cleaning maintains equipment, identifies potential problems and keeps the workplace clean and safe.
Actions:
- Establish daily cleaning procedures for each workstation.
- Inspect equipment and tools for wear, damage, or leaks during cleaning.
- Provide employees with cleaning tools and supplies.
- Establish a cleaning schedule with responsibilities.
Outcome: A clean area that’s safe, reduces downtime and improves employee morale.
4. Seiketsu (Standardize)
Consistency is the key to maintaining the successes achieved in the previous steps. Seiketsu is about creating standard operating procedures (SOPs) in an organization.
Actions:
- Standardize workplace organization and maintenance.
- Use standard labels, markings and documentation.
- Train employees on standards and monitor compliance.
- Use tools such as checklists and audits to enforce standards.
- Use visual controls to standardize practices and maintain order.
Outcome: A uniform zone that reduces variation and simplifies handoffs between tasks or shifts.
5. Shitsuke (Sustain)
The final step Shitsuke is about discipline and continuous improvement. 5S is embedded in the organization’s culture and sustained long term. Making processes safer and more efficient is part of sustaining 5S.
Actions:
- Conduct regular trainings to reinforce the 5S principles.
- Recognize and reward employees who adhere to the 5S principle.
- Encourage feedback and suggestions for improving 5S implementation.
- Regularly review and update the 5S to meet changing needs.
Outcome: A culture of excellence where employees own the area and look for improvements.
These principles may seem simple, but implementing them requires thought and a commitment to continuous improvement. Self-discipline is the key to 5S and making it sustainable.
The 6th “S”
It is also often recognized that there is a 6th “S” that underlies the entire 5S methodology: Safety. By eliminating clutter, improving organization and cleaning up, 5S as a consequence becomes safer.
Safety benefits:
- Prevention of accidents by eliminating hazards.
- Ergonomics by arranging tools and equipment correctly.
- Faster response to emergencies with clear pathways and accessible safety equipment.
Incorporating security into 5S not only protects employees, but also reinforces the overall goal of operational excellence.
Challenges
While 5S has many benefits, implementation can be tough. There are some common challenges:
- Initial Investment: Time and resources to train staff and reorganize areas.
- Resistance to Change: Employees don’t want to change their habits.
- Over Standardization: Too much rigidity can stifle creativity and adaptability.
- Sustainability: Without continuous improvement improvements will erode over time.
To overcome these challenges requires strong leadership, good communication and commitment to continuous improvement.
Summary
5S is more than just a workplace organization system, it is a philosophy of continuous improvement and efficiency. By implementing and maintaining 5S, you can unlock new levels of efficiency, safety and employee engagement.
As you begin your 5S journey, remember that what matters most is commitment, collaboration, and openness to change. With these principles in place, 5S will transform your workplace into a center of productivity and innovation.
Simplify the way people work and learn at the frontline
See the industry-leading how-to platform in a 30-minute live demo.
Learn more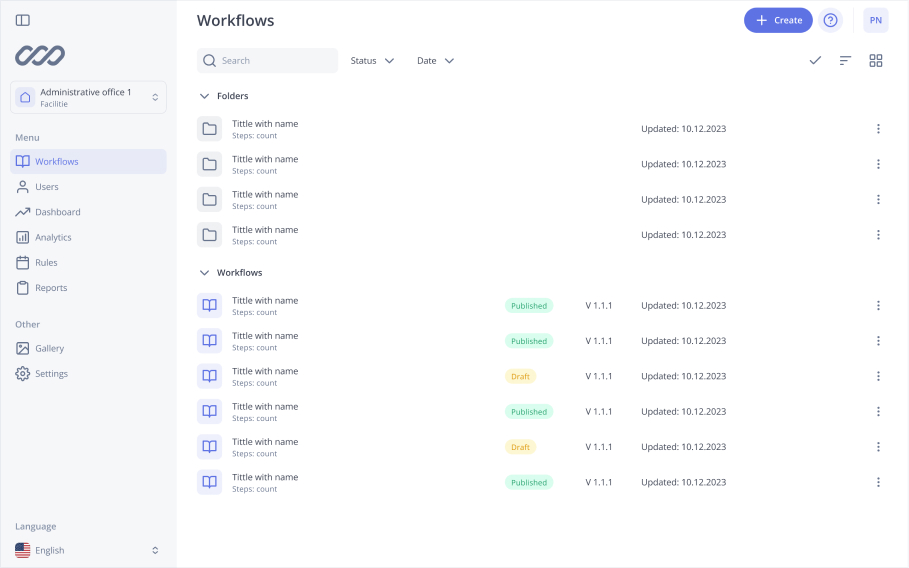
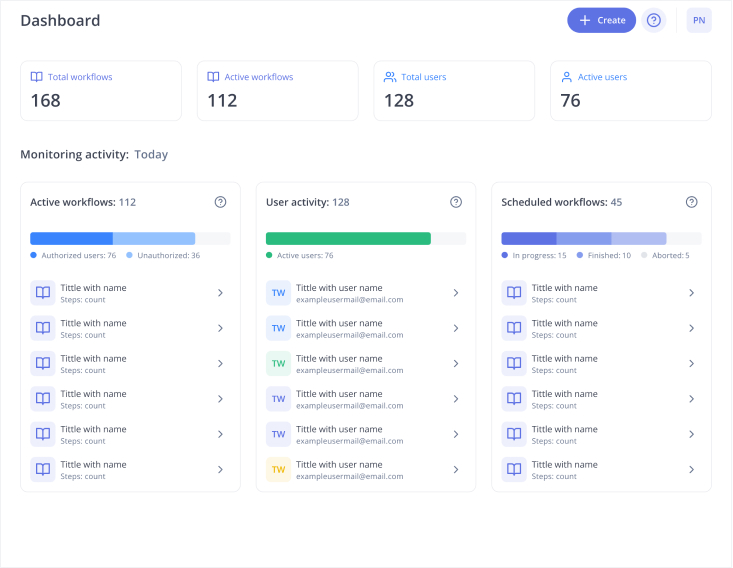