Connected Worker Platform
Industrial Workforce Digitalization
Connected worker platforms have become a new technology that is changing the way employees are managed, supported, and empowered in an ever-changing and rapidly changing world of industrial operations. The connected worker strategy is a transformational approach that increases efficiency, job satisfaction and safety within the organisation.
Today’s industrial leaders are embracing the latest solutions that use artificial intelligence, real time data and intelligent connectivity to deliver unprecedented levels of productivity, safety and efficiency. Over the past 10 years, the industrial workforce has changed dramatically. Traditional training, supervision and performance management are being replaced by digital platforms that offer:
- Analytical information based on artificial intelligence.
- Real-time employee performance analysis.
- Individual training recommendations.
- Forecasting security risks.
- Workflow optimization.
- Integrated communication systems.
- Interaction between entire operational groups.
- Real-time knowledge sharing.
- Instant access to expert support.
- Tools for collaborative problem solving.
- Data analysis.
- Continuous improvement metrics.
Why Connected Worker Solutions Matter
Connected worker platform can help companies to solve modern industrial problems. For instance, common problems include aging workforce, growing skill gaps, increasing complexity of technology and need for fast and continuous learning.
Embracing digital transformation can enhance workforce productivity and collaboration, facilitating the transition to modernized operations. A connected worker approach is the solution to these complex problems by increasing operational efficiency and supporting the frontline worker. Connected worker platforms do this by:
- Democratizing expert knowledge.
- Reducing training time.
- Increasing workplace safety.
- Overall operational efficiency.
What to Look for in Connected Worker Platforms
1. Intelligent Guidance
The best platforms do more than just monitor. They offer active real time guidance to help workers:
- Navigate complex processes.
- Access step by step instructions through digital work instructions.
- Get instant performance feedback.
- Learn and improve productivity.
2. Worker Safety Monitoring
Maintaining a safe working environment is of great importance. Connected worker platforms can play a significant role in the detection of hazards in real time, in monitoring the health and fatigue of workers and in compliance with safety regulations.
3. Knowledge Management and Skill Development
Frontline workers play a crucial role in how organizations capture, share and develop corporate knowledge. Creating a connected workforce significantly increases job productivity. Digital knowledge libraries, mentoring and knowledge transfer tools, and a continuous learning environment can help in knowledge management and skill development.
4. Performance Analytics and Optimisation
Data is the foundation of modern human resources management, integrated with existing manufacturing systems such as MES, ERP and SCADA. Using connected work platforms to optimize production processes, you can:
- Track productivity down to individual employees.
- Predict performance modeling.
- Create individual and team optimization strategies.
- Objectively measure performance.
How to Implement Connected Worker Platforms
Deployment Roadmap
- Assessment of the Current Workforce:
- Skills audit.
- Technological readiness.
- Workflow mapping.
- Choose the Right Platform:
- Platform compatibility.
- Scalability.
- Integration.
- Change Management:
- Employee engagement Plan.
- Training.
- Resistance management.
- Starting the System:
- Limited deployment.
- Constant feedback.
- Continuous improvement.
Implementation Challenges
The implementation of any improvement in an existing system will certainly cause some difficulties. The most common challenges include:
- Technological Resistance. Employees and management who have been used to working with paper materials all their lives may resist the introduction of digital technologies.
- Integration of Legacy Systems. Legacy work systems will be more comfortable and familiar for employees to use, and they may have difficulty switching to other ones.
- Initial Performance Degradation. The transition to new systems certainly entails a temporary decrease in performance at first, but later the system will become more familiar to use and performance will increase.
To reduce the impact of these problems on the workflow and for a more comfortable implementation, it is necessary not to forget about clear and clear communication with employees, explaining to them the tangible benefits of implementation and constant support.
Summary
Connected worker technology is a holistic approach to workforce optimisation. The future of industrial workforce management is intelligent connected platforms that combine connected workers with technology. Organisations that implenent connected worker solution will get more productivity, better safety, continuous learning and data driven decision making.
Simplify the way people work and learn at the frontline
See the industry-leading how-to platform in a 30-minute live demo.
Learn more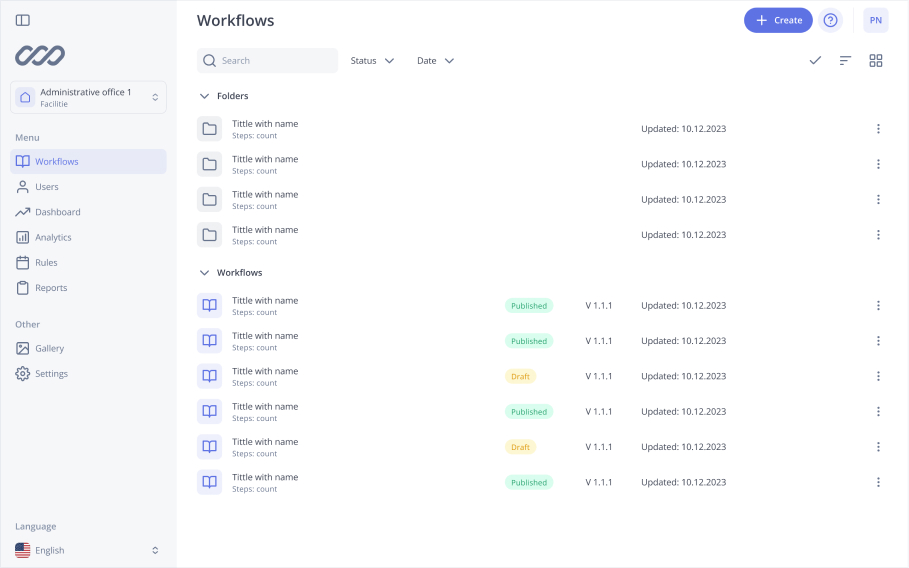
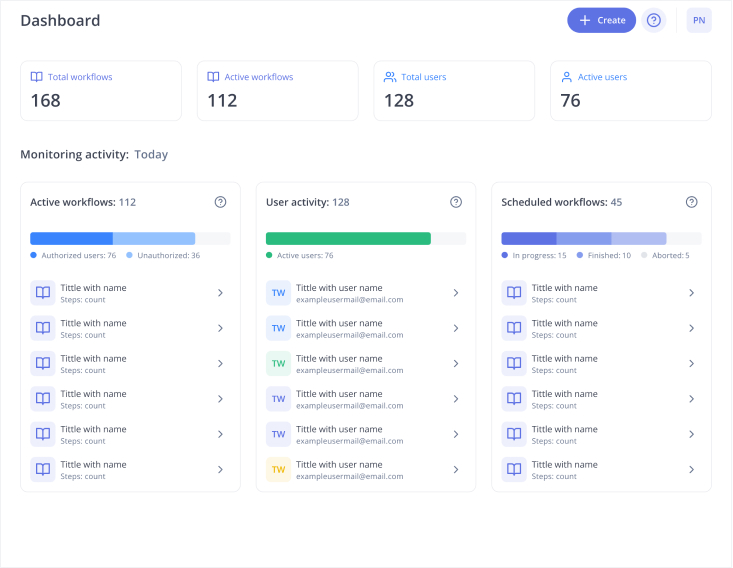