Just-in-Time-Manufacturing
In the fast-evolving world of manufacturing, companies continuously seek ways to enhance productivity, cut costs, and maintain a competitive edge. Just-in-Time (JIT) production has emerged as a transformative methodology, enabling organizations to optimize their production processes, lower inventory expenses, and adapt swiftly to market demands.
Understanding JIT Manufacturing
JIT manufacturing isn’t just a production strategy — it’s a mindset that redefines how businesses approach resource management, inventory control, and production workflows. It centers on producing the exact quantity of goods needed, precisely when they are required, while eliminating unnecessary waste.
A Brief History
JIT manufacturing originated with Toyota production system in the 1970s and is rooted in the Japanese principles of lean manufacturing. This innovative approach broke away from traditional practices that depended on large inventories and mass production. By prioritizing precision, continuous improvement, and efficiency, Toyota demonstrated how operational costs could be dramatically reduced without compromising quality.
Five Essential Strategies for JIT Manufacturing
1. Demand Driven Production
The foundation of JIT system lies in responding to real-time demand rather than relying on forecasts or historical trends. By leveraging advanced analytics and live data, businesses can create agile production schedules.
Modern technologies for the JIT inventory system include:
- Real-time customer order tracking.
- Analysis of purchasing behaviors.
- Predictive tools for short-term demand shifts.
- Dynamic adjustments to production plans.
2. Optimized Supply Chain Management
Effective co-production requires a well-coordinated and synchronized supply chain. Companies must build strong and reliable relationships with suppliers who can deliver raw materials fast and stable.
Critical elements of supply chain optimization include:
- Establishing strong supplier relationships.
- Deploying effective communication systems.
- Adopting flexible procurement practices.
- Using predictive logistics solutions.
3. Continuous Improvement and Waste Elimination
Central to JIT is the principle of Kaizen, which focuses on ongoing process evaluation and improvement to minimize waste.
Techniques to drive continuous improvement:
- Routine process assessments.
- Employee empowerment and skill-building.
- Investment in automation and smart technologies.
- Data-backed performance tracking.
4. Technology Integration
Modern JIT production relies heavily on technological advancements, such as IoT sensors, artificial intelligence (AI), and machine learning (ML). These tools bring unprecedented efficiency and accuracy.
Benefits of technology integration:
- Real time equipment monitoring.
- Predictive maintenance.
- Automated inventory tracking.
- Flexible and dynamic scheduling.
5. Resilience and Risk Mitigation
With its lean nature, JIT manufacturing can be vulnerable to disruptions. Companies must adopt proactive risk management strategies to maintain continuity.
Common Challenges in Just-in-Time Manufacturing
While JIT offers significant benefits, its implementation comes with hurdles:
Supply Chain Risk
One of the most critical challenges is supply chain fragility. JIT production requires exact timing and supplier reliability. Any disruption – natural disasters, geopolitical tensions or transportation breakdowns – can stop production instantly. A single supplier delay can create a domino effect and stop entire production lines and cost millions.
Demand Forecasting Complexity
Accurate demand forecasting remains a challenge. JIT production requires near perfect demand forecasting which is hard in a dynamic market. Consumer preferences can change, economic fluctuations or seasonal variations can render carefully planned production schedules useless overnight.
Technological Integration Barriers
Implementing real time tracking and production management systems requires significant investment and expertise. Many organizations struggle with:
- High implementation costs.
- Complex software integration.
- Staff training and skill development.
- Ongoing system maintenance and upgrades.
Risk Management Limitations
The lean nature of JIT manufacturing provides minimal buffer for unexpected events. Without substantial inventory reserves, manufacturers become extremely sensitive to production interruptions, requiring sophisticated risk mitigation strategies.
Quality Control Constraints
With minimal inventory and fast production cycles quality control is tough. Any quality variation can quickly become an operational problem and potentially cause production delays and extra costs.
Successful JIT implementation demands a holistic approach, combining technological innovation, strategic planning, and adaptive management techniques.
Empowering JIT with Advanced Solutions
To truly unlock the potential of JIT manufacturing, companies need powerful, intuitive tools that simplify complex operational processes.
ProcessNavigation is designed to change how manufacturers manage production. Our app enables businesses to:
- Manage production schedules.
- Reduce inventory costs.
- Enhance supply chain visibility.
- Make data driven decisions instantly.
Simplify the way people work and learn at the frontline
See the industry-leading how-to platform in a 30-minute live demo.
Learn more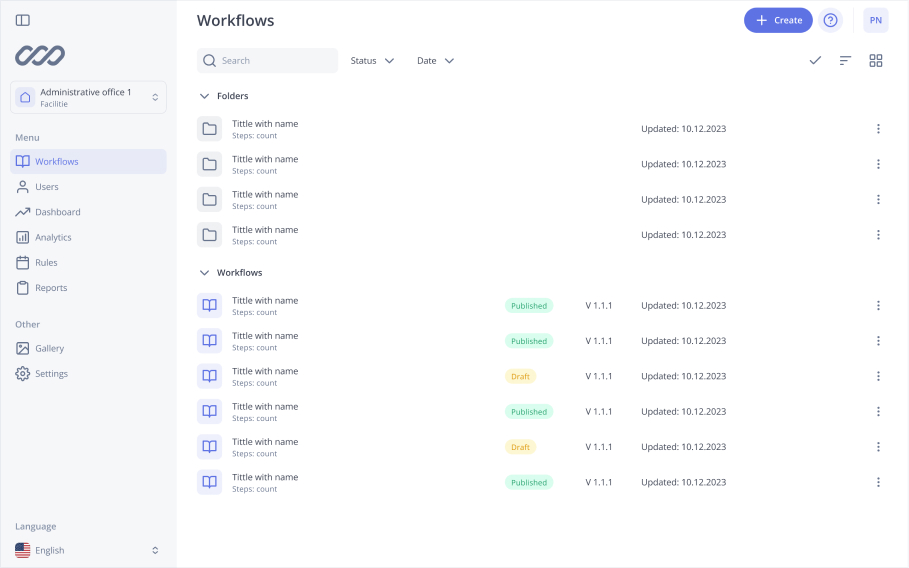
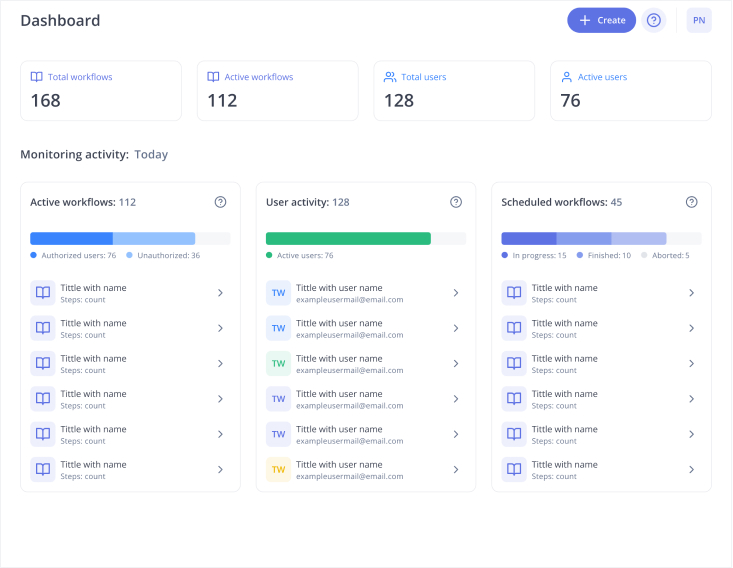