Changeover Time
Changeover time, also known as changeover process or changeover times, is key in modern production and manufacturing industries. It is the total time it takes to switch a machine, system, or process from one product to another. Sounds simple but changeover time has big implications for production efficiency, output, flexibility, and cost. In this article we will dive deep into what changeover time means, why it matters, how to optimize it and what other terms are used interchangeably with “change over time.”
What is Changeover Time
Changeover time is often misunderstood or oversimplified. In industrial terms it is not just the time to shut down and restart a process but all the activities in between: disassembling previous settings or tooling, cleaning, maintenance, calibration, testing and starting the new run. Organization of materials and tools at the production line is critical to minimizing downtime during this transition. It starts when the last item of the previous production batch is complete and ends when the first good item of the next batch is produced. This period is from the last good part of the previous run to the first good part of the next product.
In manufacturing dies refers to special tools used to shape or cut materials and quick replacement of these is key to reducing changeover time. Changeover time is not limited to manufacturing. Changeover times are relevant in sectors such as logistics, service delivery, IT systems and even healthcare. Anytime resources are reallocated or repurposed changeover time becomes a consideration.
Change Over Time vs. Changeover Time
While “changeover time” generally refers to the technical time needed to change a system or machine from one configuration to another, “change over time” is broader and more abstract. It often denotes long-term transformations or trends. For example, in business, it might describe organizational shifts over decades.
Thus, when people look for “another word for change over time,” they might be referring to terms like:
- Transformation
- Evolution
- Development
- Progression
- Shift
- Trend
These words, while similar, do not replace “changeover time” with industrial terminology. It is important to distinguish between the two in professional settings.
Why Changeover Time Matters
In production, time is money — literally. Every minute a machine is not producing saleable product is lost revenue. Long or inefficient changeover times means decreased equipment utilization, higher labor costs, lower output and less responsiveness to market demand. Manufacturers can implement specific ways to be more efficient and lower costs during changeover. Optimizing changeover times can make a significant difference in overall efficiency by reducing downtime and workflow.
Plus, in just-in-time (JIT) manufacturing, changeover time becomes a bottleneck. These systems run on minimal inventory and rapid transitions. A slow changeover time will break the entire supply chain by causing delays, excess inventory or idle workers. Reducing changeover time is key to maximizing production efficiency. Supervisors track and measure changeover time to find areas to improve and ensure smooth transitions.
Components of the Changeover Process
- Preparation: Gather tools, parts, instructions, resources before change begins. Reduces time spent searching during changeover.
- Machine Shutdown: Machine or process is stopped. Depending on industry, this may mean locking up moving parts, depressurizing systems, or discharging materials.
- Remove Previous Setup: All equipment or settings from previous run are removed. This could be dies, molds, raw materials, or software programs.
- Clean: Machines and surfaces are cleaned to prevent contamination or malfunction.
- Install New Setup: New components or configurations are installed. This could be new tools, software programs or new raw materials.
- Test and Calibrate: Machine is tested with new setup. Adjustments may be needed to meet specs.
- Production Startup: Production begins. First few units are monitored to ensure quality.
Strategies to Reduce Changeover Time
Changeover isn’t just about speed, it’s about continuous improvement. Here are the strategies:
- SMED (Single-Minute Exchange of Die): Developed by Shigeo Shingo, SMED aims to get changeovers down to single digit minutes. The method separates internal setup (tasks done while the machine is stopped) from external setup (tasks that can be done while it is running). Implementing SMED involves analyzing each step to see what can be done while the machine is still running, so you minimize downtime. It separates internal setup from external setup so you can do tasks in parallel and minimize downtime.
- Standardization: Using standardized tools and procedures reduces variability and errors during changeovers.
- Visual Management: Visual aids like color codes, markings or diagrams can speed up identification and reduce mistakes. This is especially useful in die changes where quick identification and replacement are critical.
- Quick-Release Mechanisms: Replacing bolts or screws with clamps or levers reduces tool time.
- Cross-Training Employees: When employees are trained on multiple machines or tasks, bottlenecks during changeovers can be reduced.
- Automation: Automated systems can change settings or configurations with minimal human intervention.
Changeover Time in Different Industries
While it started in manufacturing, it applies everywhere: In a manufacturing plant, changeover time is key to high productivity and efficiency. Changeover time is important for anyone working in manufacturing and other industries.
- Healthcare: Operating rooms need to be cleaned between surgeries — a kind of changeover.
- IT: Server updates, software rollouts and platform switches require technical changeovers. In a manufacturing facility, reducing changeover time can make a significant impact on operational efficiency. Teams adjust machinery and assembly lines to produce a product efficiently. Shop floor engagement is key to successful changeover time reduction.
- Food Services: Changing a menu or recipe in a restaurant kitchen means adjusting equipment and processes.
- Airlines: Turnaround time between flights means cleaning, refueling, boarding and paperwork—a classic changeover.
Challenges in Changeover Optimization
While faster is better, it’s not without its challenges:
- Quality Control: If changeovers are rushed, quality suffers. Accurate measurement of changeovers is key to ensuring quality is maintained while optimizing efficiency. A full understanding of procedures is required to maintain quality during faster changeovers.
- Equipment Wear: More frequent or aggressive changeovers means more maintenance costs. More frequent changeovers means you need to inspect every internal component to ensure durability.
- Workforce Resistance: Not all employees are comfortable with new procedures or faster pace. Regular adjustments and feedback loops are needed to sustain improvements.
- Training Costs: New systems require initial investment in training. Continuous improvement initiatives can help you identify where to train to get the biggest efficiency gains.
Changeover Times Tracking
Key performance indicators (KPIs) to monitor changeover efficiency:
- Total Downtime per Changeover
- Average Changeover per Shift
- Number of Changeovers without Rework
- Uptime after Changeover
Measuring the time from one production run to the next is key. In a lean environment, reducing changeover time is critical to being efficient. Better changeover time management means more production.
Supervisors should track changeover time to find areas to improve and to make sure transitions are as smooth as possible. Tools like OEE (Overall Equipment Effectiveness) roll up changeover data into other metrics. Accurate changeover time measurement is required for these tools to be meaningful.
Conclusion
Changeover time is more than a technical metric — it is a strategic lever that affects cost, efficiency, quality and responsiveness. Companies that understand and master the changeover process have a competitive advantage in a dynamic market. By reducing changeover time, a company can save money and produce more. Lower changeover times means companies can produce products more efficiently.
Meanwhile the broader concept of change over time reminds us that adaptation is not optional but essential. Whether it is changing machines or business models, success depends on the ability to evolve fast and smart.
Master changeover times is not just about squeezing seconds out of a process — it is about unlocking operational agility. Continuous improvement in changeover processes leads to sustained productivity and cost savings. The companies that get this right are not just faster. They are smarter, more resilient, and ultimately better prepared for whatever comes next.
Simplify the way people work and learn at the frontline
See the industry-leading how-to platform in a 30-minute live demo.
Learn more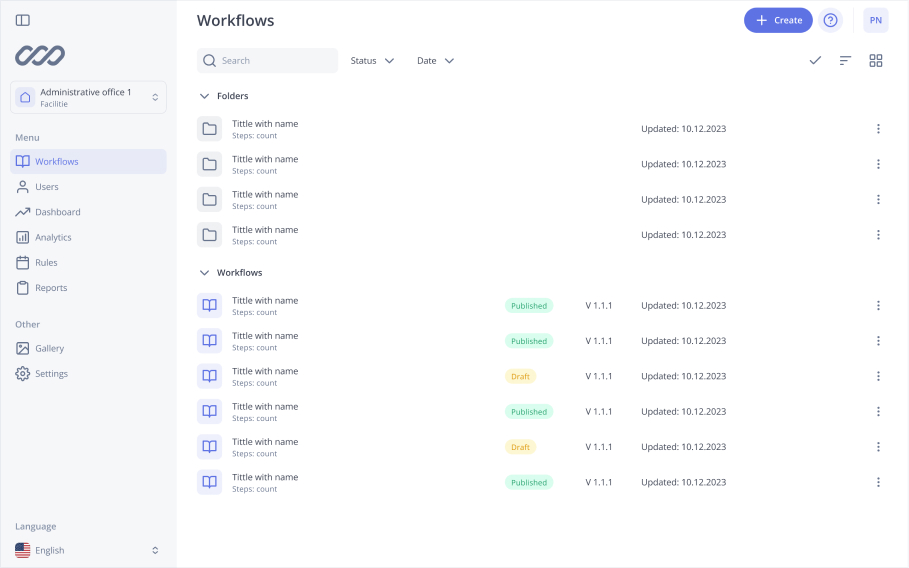
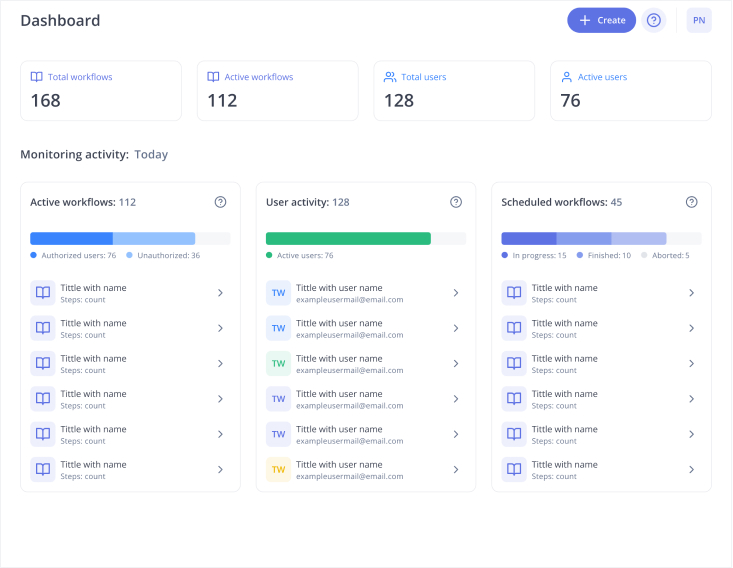