Digitizing Quality Assurance in Pharmaceutical Production
3 weeks
Time to implement
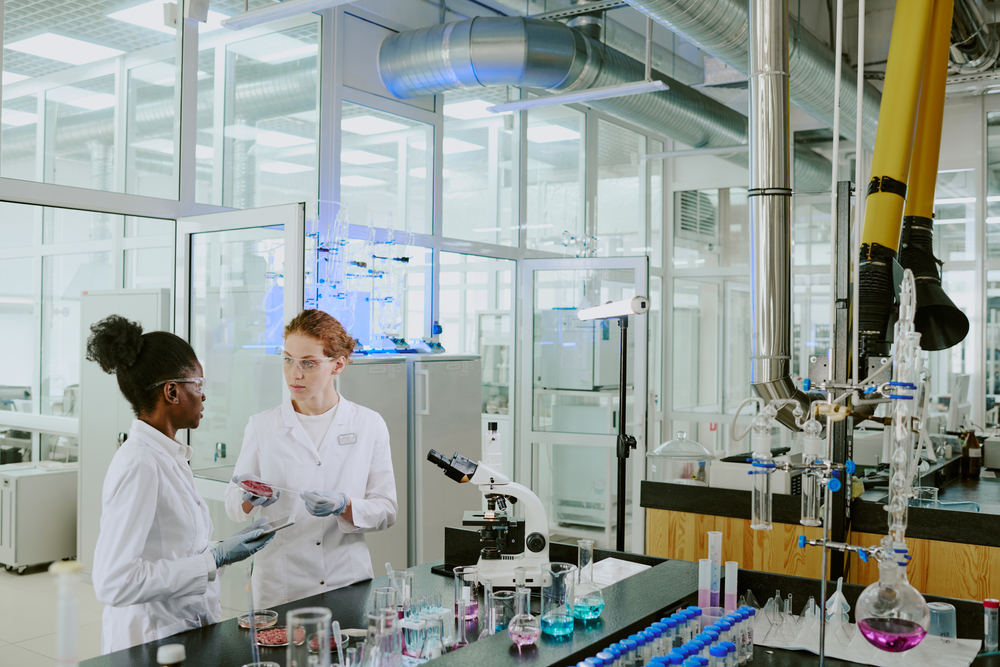
A pharmaceutical company producing prescription medications for international markets approached ProcessNavigation to enhance accuracy and transparency in their quality control processes. Despite a high level of equipment automation, they continued to face issues stemming from manual documentation and inconsistent procedural compliance
Problem
The company encountered several critical challenges:
- Manual Data Entry Errors: Operators frequently made mistakes or omitted key quality checks due to the reliance on handwritten forms.
- Lack of Real-Time Visibility: Management had no way to monitor GMP compliance or process deviations as they happened.
- Time-Consuming Audit Preparation: Internal and external audits required extensive time and effort to gather and verify paper-based records.
- Regulatory Compliance Risks: Incomplete or inconsistent documentation could lead to batch recalls, failed inspections, or regulatory penalties.
Objectives
ProcessNavigation was tasked with the following goals:
- To digitize all quality control procedures to eliminate reliance on paper.
- To reduce errors in quality checks through guided, structured processes.
- To rrovide real-time visibility of quality operations to supervisory teams.
- To streamline audit preparation and ensure data traceability.
Solution
We implemented a comprehensive digital system tailored to pharmaceutical quality control needs:
- Interactive Digital Protocols: All QC steps were converted into structured, interactive checklists with built-in logic validation to prevent omissions or incorrect entries.
- Integration with Production Equipment: Where possible, QC data was automatically pulled from production lines to reduce manual input.
- Traceable User Sign-offs: Each step was digitally signed and time-stamped, ensuring full accountability and audit readiness.
- Real-Time Dashboard for Supervisors: Management gained instant visibility into task completion, procedural adherence, and exception alerts.
- Audit Mode Functionality: Full digital logs could be exported for inspections or compliance reporting in just a few clicks.
Results
Just three weeks after implementation, the client reported major improvements:
- Reduction in QC Errors: Digital validation and automation significantly cut down manual mistakes.
- Audit Preparation Time Reduced: Data was centralized, structured, and accessible instantly.
- Enhanced Transparency: Supervisors could proactively identify issues and intervene in real time.
- Improved Staff Confidence: Operators had access to clear, easy-to-follow instructions and no longer felt burdened by confusing paperwork.
Conclusion
By digitizing its quality assurance operations with ProcessNavigation, the pharmaceutical company mitigated compliance risks, increased operational efficiency, and simplified audit readiness. This transformation strengthened internal trust and positioned the company for smoother regulatory engagement and future scalability.
Simplify the way people work and learn at the frontline
See the industry-leading how-to platform in a 30-minute live demo.
Send request-
+35%
Operational Efficiency Increased
-
−62%
Reduction in Quality-Related Incidents
-
−47%
Decrease in Audit Preparation Time