Clean, Inspect, Lubricate (CIL)
In industrial operations, infrastructure planning and asset management, equipment durability, safety and efficiency are not a nice to have, it’s a must have. One of the key principles to effective maintenance strategies is the CIL acronym which stands for Clean, Inspect, Lubricate. Despite its simplicity CIL is a powerful and proactive approach to equipment care that reduces downtime and extends the life of the machine. CIL ensures equipment is in optimal condition and performance and longevity.
This article will look at the concept, etymology and importance of CIL, its role in preventive maintenance and practical steps to implement this across various industrial environments.
What Does CIL Stand For?
CIL — a term you’ll likely encounter in manufacturing and engineering — stands for Clean, Inspect, Lubricate. That’s a maintenance strategy used within Total Productive Maintenance (TPM) and Autonomous Maintenance programs. Each of those three elements contributes to a structured routine aimed at keeping operations running smoothly and supporting long-term development.
1. Clean: Beyond Aesthetics
At its core, cleaning is more than just tidying up. It’s about systematically removing contaminants, debris and residues. That helps you uncover hidden defects—like leaks or wear—that can be costly to fix down the line. You also improve energy efficiency and reduce your environmental impact. Safety in the workplace improves too, as you eliminate hazards. That supports better planning and regulatory compliance. And let’s not forget about community expectations around transparency and sustainability. Cleanliness is often tied to compliance with council or governmental standards in regulated industries.
In that sense, cleaning is not just a necessary part of infrastructure care, it’s a business imperative. And that’s what drives real innovation and progress in manufacturing and engineering.
2. Inspect: Spot Problems Early
Inspecting equipment regularly is where problems are spotted before they cause any real headaches. That’s where operators come to check components for signs of stress, misalignment or corrosion. That involves (among other things) checking fasteners and fittings, monitoring pneumatic and hydraulic systems, and evaluating the condition of electrical and mechanical connections. You document your findings so leadership can review them and plan accordingly.
A well-documented inspection process helps you develop maintenance strategies that are in line with your organization’s broader efforts to be more informed. When you do the inspection right, you get a much clearer picture of your assets’ health — and that supports the decisions you make about upgrades or replacements down the line.
3. Lubricate: Reduce Friction, Extend Life
Lubrication is key to keeping equipment running smoothly — and that means doing it right. According to the manufacturer’s specifications and regulations, you apply the right lubricants, avoid over-lubricating (which can happen when you don’t follow best practices), make sure lubrication points are accessible and clean. And you log that maintenance activity so you can refer to it later.
Lubricating systems are often a major part of autonomous maintenance in many industries. That means they’re directly tied to the availability of funds and the training your staff gets. And that, in turn, affects how smoothly your operations run.
Benefits of CIL
A good CIL program gives you:
- Less Downtime: Regular inspection and cleaning prevent unexpected failure.
- Longer Equipment Life: Clean, lubricated systems last longer, no need to replace.
- Safety: Fewer hazards when equipment is well maintained.
- Better Production: Stable operation means consistent results.
- Lower Maintenance Costs: Preventive action means no emergency repairs.
- Employee Engagement: Operators become the leaders of their equipment, higher workplace morale.
Implementing a CIL Program
To get CIL working:
- Training: Teach operators what each maintenance step means.
- Standardization: Create visual forms and log sheets.
- Documentation: Record everything, observations and issues.
- Monitoring and Evaluation: Analyze operational data for patterns and trends.
- Continuous Improvement: Review abbreviations, steps and schedules regularly.
This framework helps leadership support the long-term goals of the organization. It also helps councils and developers meet project requirements for infrastructure.
CIL as a Cultural Shift
CIL is more than a maintenance routine — it’s a cultural shift. By including cleaning, inspecting and lubricating in daily procedures organizations:
- Show respect for equipment, teams and community resources
- Improve cross departmental communication
- Build leadership in frontline staff
- Meet operational and regulatory requirements
The pronunciation of the acronym “CIL” may vary but the form and function is the same across industries, it’s the shift to proactive intelligent asset management.
Conclusion
The methodology CIL — Clean, Inspect, Lubricate — is the foundation of modern industry. It supports regulations, respects resource constraints and works across all environments. By doing CIL consistently you get less downtime, more efficiency and better alignment to stakeholder expectations including community infrastructure levies and sustainability targets.
As new technologies and systems emerge the basics of maintenance — defined and supported by CIL — will remain important. Whether in manufacturing, utilities or infrastructure development the future of reliable operations depends on getting the basics right.
Simplify the way people work and learn at the frontline
See the industry-leading how-to platform in a 30-minute live demo.
Learn more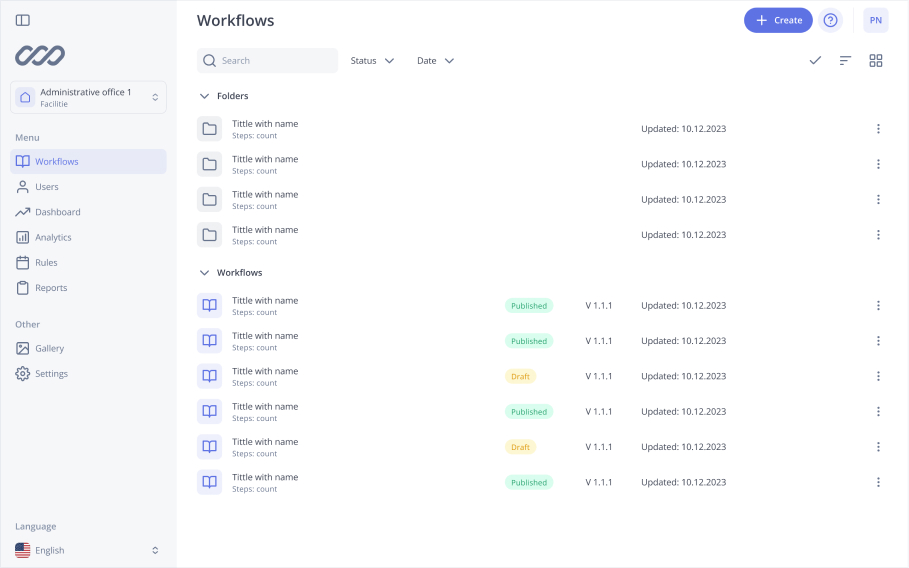
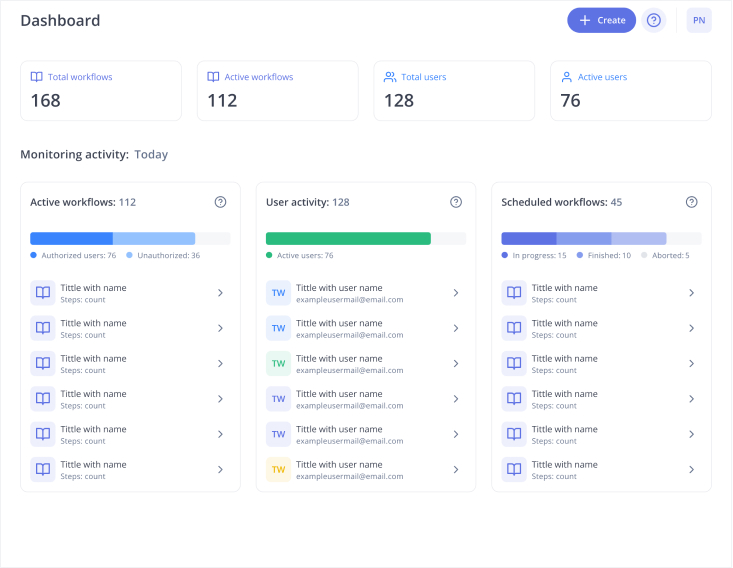