House of Quality
The House of Quality (HoQ) is a key concept in product development and quality management. It’s a structured approach to translating customer requirements into engineering characteristics so the final product meets customer expectations and delivers quality. The House of Quality is a core part of Quality Function Deployment (QFD), a methodology used by companies to combine customer feedback and technical specifications during the design and production process. It helps turn customer needs into product specifications that guide development processes.
The House of Quality is part of the planning process in product development, so customer requirements are systematically addressed. Design parameters affect the alignment between customer needs and design requirements, particularly using a relationship matrix, which illustrates how varying design elements, such as cost and features, impact customer satisfaction and priority.
In this article we will explore what the House of Quality is, what it’s for and how to use it, and the steps to create a HoQ. By the end of this article you’ll understand this tool, its role in the product development process and how it contributes to a successful product.
What is a House of Quality?
The House of Quality (HoQ) is a visual tool to help teams identify and prioritise customer needs and expectations while addressing technical requirements to meet those needs. It’s a communication bridge between marketing, design, engineering and manufacturing. By using the House of Quality companies can ensure their product is developed with a clear understanding of both customer wants and engineering constraints.
The House of Quality looks like a matrix that connects two sets of information:
- Customer requirements (WHATs): These are the features, attributes or specifications customers expect from the product. These are gathered through market research, surveys, focus groups, customer interviews and feedback.
- Engineering characteristics (HOWs): These are the technical aspects or design specifications the product must meet to satisfy customer requirements. These could be material choices, production methods, dimensions, performance specifications etc. The operating system can influence factors such as the expected lifespan of a product and its overall cost to customers.
The matrix itself is shaped like a house which is where the term “House of Quality” comes from. The “roof” of the house represents the relationship between different engineering characteristics, the “walls” and “floor” help to prioritize and evaluate the most important parts of the product development process. The matrix helps in calculating the relative importance of various product attributes and parameters for decision-making.
The Importance of House of Quality
In any product development cycle customer needs must be aligned with technical capabilities for success. Without the right tools and processes misunderstandings can occur and products don’t meet customer expectations. The House of Quality is a systematic way to ensure customer requirements are understood and translated into engineering solutions.
Here are the top reasons why the House of Quality is so important in product development:
- Customer Focused Design: The HoQ tells you to listen to and prioritize customer feedback. It keeps the voice of the customer at the heart of product design and development.
- Cross Functional Collaboration: The House of Quality encourages collaboration between different departments within an organization. Marketing, design, engineering and manufacturing teams work together to make sure the product meets customer needs.
- Better Decision Making: The matrix format of the House of Quality helps teams prioritize customer requirements and engineering characteristics. It gives you a clear visual of what needs to be done and enables better decision making.
- Reduced Risk of Failure: By addressing customer needs early in the design process and aligning them to technical specifications the risk of developing a product that doesn’t meet market expectations is greatly reduced.
- Optimization of Resources: The House of Quality helps you identify the most critical engineering characteristics that will have the biggest impact on customer satisfaction. This allows you to allocate resources more effectively and focus on what matters most.
- Higher Customer Satisfaction: By using the House of Quality, you can ensure customer needs are integrated into the product design process and get higher customer satisfaction.
- Increase Customer Satisfaction: Employing models like the House of Quality and the Kano Model facilitates collaboration among various departments and leads to better planning and development. By incorporating the voice of the customer into project planning, these strategies ensure that products meet user needs, ultimately increasing customer satisfaction.
The House of Quality Matrix
The House of Quality matrix is divided into several key sections, each serving a specific purpose in the process of aligning customer needs with engineering characteristics. These sections include:
- WHATs (Customer Requirements): This section lists the customer requirements or attributes that the product must satisfy. These requirements are typically gathered through market research and customer feedback. Examples might include product durability, ease of use, or aesthetic appeal.
- HOWs (Engineering Characteristics): This section lists the engineering characteristics or technical specifications that will address the customer requirements. These might include material choice, production methods, design features, and so on.
- Relationship Matrix: This is the core of the House of Quality. The relationship matrix shows how each design parameter affects customer needs. Ratings are typically strong, moderate, weak. This matrix helps to determine which engineering characteristics have the greatest impact on customer satisfaction.
- Customer Requirements Prioritization: In this section, customer requirements are ranked by importance. This ranking helps the team to focus on the most critical customers’ needs and allocate resources according to importance.
- Correlation Matrix (Roof of the House): The roof of the House of Quality shows the interrelationships between the different engineering characteristics. It shows how changes in one characteristic affect others, identifying potential conflicts or synergies in the design.
- Competitive Benchmarking: This section compares the company’s product with competitors’ products to identify strengths and weaknesses. By understanding how the product compares to others, the team can make informed decisions on what to improve. This competitive analysis helps to understand how the product performs against others in the market.
- Technical Difficulty or Cost Evaluation: In this section, the team evaluates the technical difficulty or cost of each engineering characteristic. This helps to determine which features can be implemented within the given constraints.
Benefits of the House of Quality
- Customer Centric: The HoQ ensures the product is designed for the customer. By matching customer needs to technical specs companies deliver products that meet customer demand.
- Improved Communication: The House of Quality breaks down silos and makes teams work together towards a common goal.
- Better Resource Allocation: By prioritizing customer requirements and engineering characteristics the HoQ helps to focus on the most critical areas. Reduces waste of resources and better product outcome.
- Risk Reduction: The HoQ identifies potential issues early in the design process, reduces the risk of costly mistakes later on.
- Competitive Advantage: By including customer feedback and engineering challenges the House of Quality helps to create products that are more competitive in the market.
- Higher Customer Satisfaction: Using the House of Quality can increase customer satisfaction by integrating customer needs into the product design process.
- Quality Example: An example of the House of Quality is in the development of a smartphone where customer ratings and design attributes are systematically assessed to create a successful product.
Conclusion
The House of Quality is a way to make customer requirements become engineering solutions. It brings together cross-functional teams and ensures products are designed for both customer and technical constraints. By following this process you can improve quality, reduce risk and get a competitive advantage. Whether you are creating a new product or refinement to an existing one the House of Quality is the tool to guide your product development and make sure the end product meets or exceeds customer needs.
Simplify the way people work and learn at the frontline
See the industry-leading how-to platform in a 30-minute live demo.
Learn more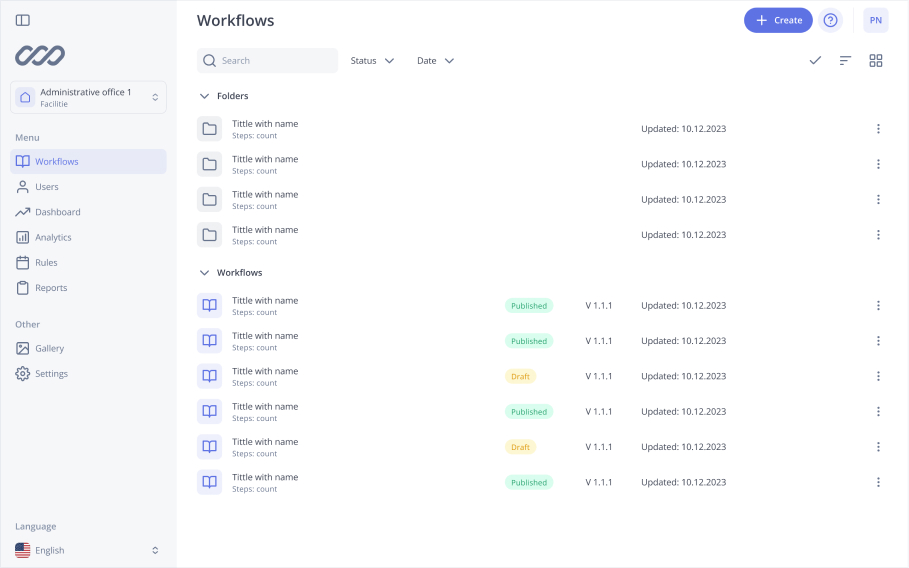
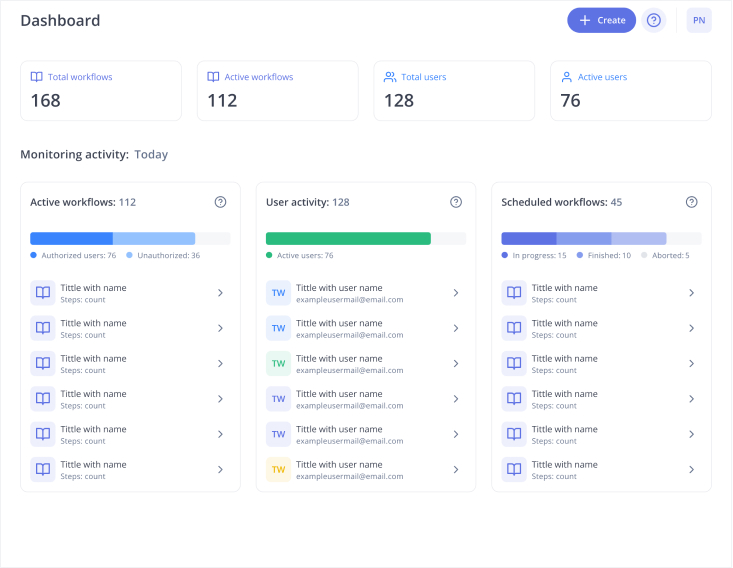